
weixin_38744270
- 粉丝: 329
- 资源: 2万+
最新资源
- 【岗位说明】主任药师的岗位职责.docx
- 【岗位说明】中医皮肤科门诊医师岗位职责.docx
- 【岗位说明】XX服装产品开发部工作职责.doc
- 【岗位说明】纺织行业部门岗位职责说明.doc
- 【岗位说明】服装厂工作制度职责及要求.doc
- 【岗位说明】服装代理公司各岗位职能详细表.doc
- 【岗位说明】服装公司岗位说明书(大全).doc
- 【岗位说明】服装公司岗位说明书.doc
- 【岗位说明】服装公司岗位职责01.doc
- 【岗位说明】服装公司岗位职责03.doc
- 【岗位说明】服装公司岗位职责02.doc
- 【岗位说明】服装公司组织架构及岗位职责.doc
- 【岗位说明】服装公司营运部各岗位职责与工作内容.doc
- 【岗位说明】服装品牌岗位职责.docx
- 【岗位说明】服装制衣厂工作职责.doc
- 【岗位说明】服装销售员岗位职责.doc
资源上传下载、课程学习等过程中有任何疑问或建议,欢迎提出宝贵意见哦~我们会及时处理!
点击此处反馈


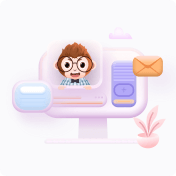