
xiaowu198809
- 粉丝: 13
- 资源: 17万+
最新资源
- 基于移动平台的远程在线诊疗系统+ssm-微信小程序毕业项目,适合计算机毕-设、实训项目、大作业学习.rar
- 基于微信小程序的跳蚤市场设计与实现ssm-微信小程序毕业项目,适合计算机毕-设、实训项目、大作业学习.rar
- 基于微信小程序的影院选座系统+ssm-微信小程序毕业项目,适合计算机毕-设、实训项目、大作业学习.rar
- 基于微信小程序的水果销售系统的设计与实现springboot-微信小程序毕业项目,适合计算机毕-设、实训项目、大作业学习.rar
- COMSOL光学模型:一维光子晶体nanobeam三维模型仿真(包含场分布,透射光谱)
- 家具购物小程序+php-微信小程序毕业项目,适合计算机毕-设、实训项目、大作业学习.rar
- 计算机实验室排课与查询系统+ssm-微信小程序毕业项目,适合计算机毕-设、实训项目、大作业学习.rar
- 家庭财务管理系统的设计与实现+ssm-微信小程序毕业项目,适合计算机毕-设、实训项目、大作业学习.rar
- 基于微信小程序的小说阅读系统ssm-微信小程序毕业项目,适合计算机毕-设、实训项目、大作业学习.rar
- 基于微信小程序的外卖点餐系统设计与实现ssm-微信小程序毕业项目,适合计算机毕-设、实训项目、大作业学习.rar
- 基于微信小程序的网约巴士订票平台的设计与实现ssm-微信小程序毕业项目,适合计算机毕-设、实训项目、大作业学习.rar
- 家庭事务管理微信小程序+ssm-微信小程序毕业项目,适合计算机毕-设、实训项目、大作业学习.rar
- 家庭大厨微信小程序+ssm-微信小程序毕业项目,适合计算机毕-设、实训项目、大作业学习.rar
- 家政服务管理系统+ssm-微信小程序毕业项目,适合计算机毕-设、实训项目、大作业学习.rar
- 基于微信小程序的校园兼职系统-微信小程序毕业项目,适合计算机毕-设、实训项目、大作业学习.zip
- 汇川MD500E变频器开发方案 源码+解析+控制板原理图, MD500E代码方案和解析文档+原理图+送仿真资料 资料全 包含pmsm的foc控制算法,电阻、电感、磁链等参数的辩识算法,死
资源上传下载、课程学习等过程中有任何疑问或建议,欢迎提出宝贵意见哦~我们会及时处理!
点击此处反馈


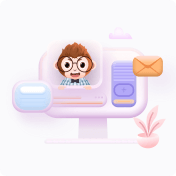