
xiaowu198809
- 粉丝: 13
- 资源: 17万+
最新资源
- 城市起重机市场分析:预计2030年全球市场销售额将达到19.84亿美元.pdf
- 储能PCS市场分析:预计2030年全球市场销售额将达到115.8亿美元.pdf
- 串口服务器行业分析:预计2029年全球市场销售额将达到28亿元.pdf
- 低密度造影剂行业分析:预计2030年全球市场销售额将达到8.36亿美元.pdf
- 电动汽车保险市场分析:预计2030年全球市场销售额将达到162.5亿美元.pdf
- 电动EGR阀行业分析:预计2030年全球市场销售额将达到15.95亿美元.pdf
- 电流传感器市场研究:欧洲是全球最大的市场,占有约28%的份额.pdf
- 电推剪市场分析:预计2030年全球市场销售额将达到12.59亿美元.pdf
- 电子批记录(EBR)软件市场研究:预计2030年全球市场销售额将达到11.72亿美元.pdf
- 电子级二氧化硫(SO2)市场研究:预计2030年全球市场销售额将达到0.3亿美元.pdf
- 对位芳纶纤维市场研究:美国是最大消费国,占约41%的市场份额.pdf
- 非离子型碘造影剂市场研究:预计2030年全球市场销售额将达到54.66亿美元.pdf
- 肥料添加剂市场研究:预计2030年全球市场销售额将达到43亿美元.pdf
- 供应商关系管理系统市场研究:预计2030年全球市场销售额将达到183.5亿美元.pdf
- 工业视觉成像相机市场调研:欧洲是全球最大的市场.pdf
- 光电芯片测试仪市场研究:北美、欧洲、中国和日本是全球的主要地区.pdf
资源上传下载、课程学习等过程中有任何疑问或建议,欢迎提出宝贵意见哦~我们会及时处理!
点击此处反馈


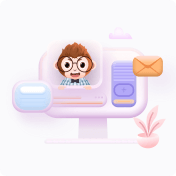