
weixin_38660058
- 粉丝: 5
- 资源: 920
最新资源
- 电信口令兑换0.88~100亓话费.mp4
- 抖店精细化运营详细的精细化运营抖店玩法.mp4
- 抖看小说app 覆盖各类题材.mp4
- 抖音快手小红书养号工具,安卓手机通用不限制数量,截流自热必备养号神器解放双手.mp4
- C语言实践作业飞机大战.zip
- 抖音热门华语劲爆车载DJ歌曲合集.mp4
- 抖音评论采集抓取获客系统v2.4.mp4
- 基于Android Studio开发的安卓的音乐播放器app源码+报告(安卓期末大作业)
- 抖音小红书留微信不屏蔽生成工具.mp4
- 独居治愈系视频制作,日变现多张,多平台发布(抖音、视频号、小红书).mp4
- 短视频上热门的20个流量密码实战案例.mp4
- 多邻国语言Duolingo v6.10.4.0解锁vip付费版.mp4
- 发光霓虹灯文字闪烁特效源码.mp4
- 番茄小说领券0.01亓撸书本等.mp4
- 锂电池项目 欧姆龙NJ501-1400系列plc程序 自动二封机,PLC程序,无触摸屏程序 1.松下A6系列总线伺服驱动器控制,位置模式控制 2.雷赛总线节点步进电机控制,参数读写,电流,极性,感应器
- 饭团追书app 拥有非常多的分类.mp4
资源上传下载、课程学习等过程中有任何疑问或建议,欢迎提出宝贵意见哦~我们会及时处理!
点击此处反馈


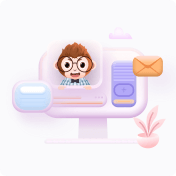