没有合适的资源?快使用搜索试试~ 我知道了~
温馨提示
此参考设计介绍了适用于车载充电器的 6.6kW 图腾柱 (TTPL) 无桥功率因数校正 (PFC) 解决方案。功率级由 C2000™微控制器 (MCU) 通过 SiC 隔离式栅极驱动器 实现碳化硅 (SiC) MOSFET 的驱动。此设计采用了三相 交错技术并在连续导通模式 (CCM) 中运行,在 240V 输 入电压和 6.6kW 全功率下可实现 98.60% 的效率。 C2000 控制器可实现切相和自适应死区时间控制,从而 改善轻载条件下的功率因数。栅极驱动器板(参见 TIDA-01605)实现了增强型隔离,可承受超过 100V/ns 的共模瞬态抗扰度 (CMTI)。栅极驱动器板还包含两级关 断电路,可在短路情况下保护 MOSFET 抵御电压过 冲。
资源推荐
资源详情
资源评论





















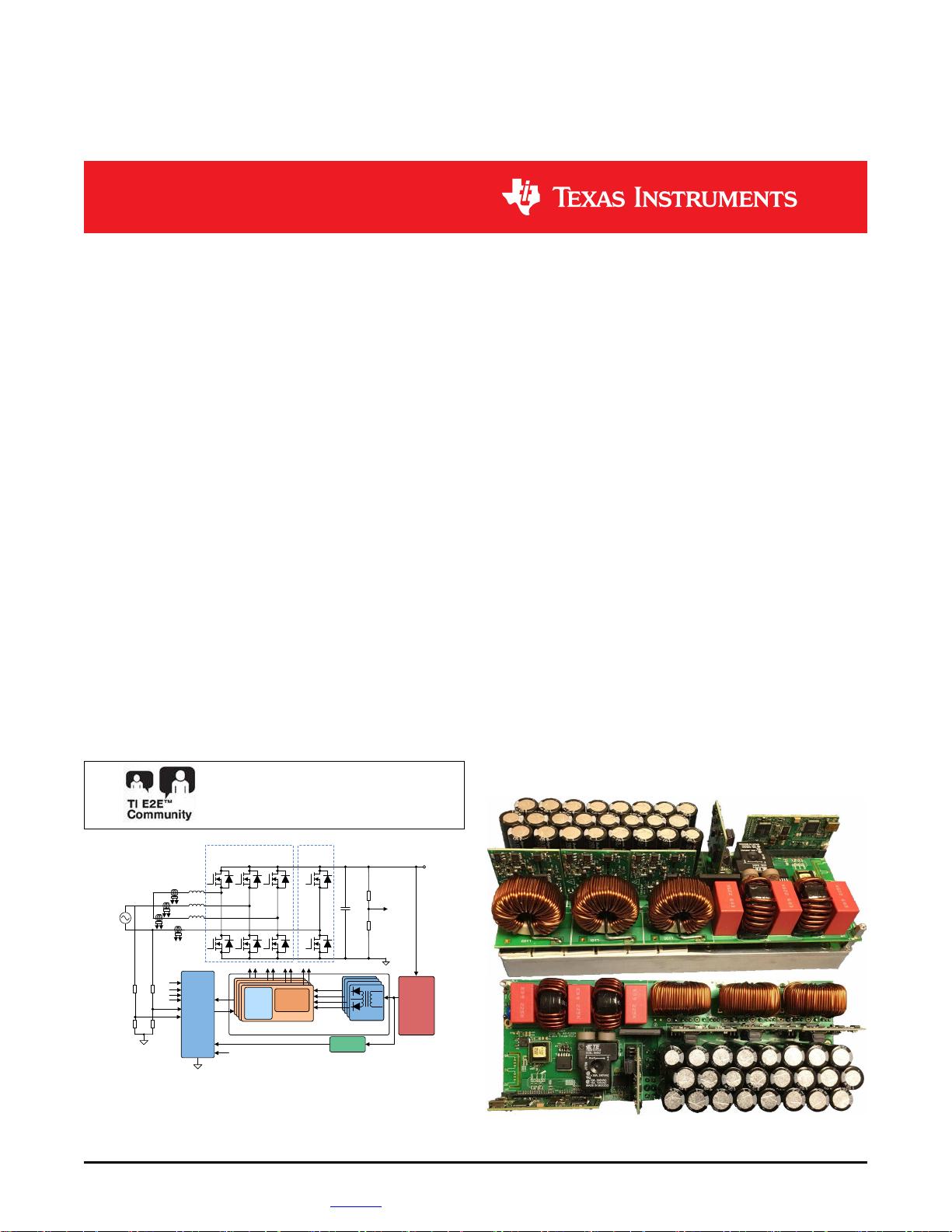
0
Driver
Vdc
Vdc Sense
Line
Voltage
Sense
Neutral
Voltage
Sense
SiC MOSFET
(High Frequency)
Si/SiC (Low
Frequency)
Power Grid
V_N
Ineu
Vdc Sense
F28004x
C2000
TM
MCU
V_L
UCC28700-Q1
TLV71333-Q1
Vdc
5 V
3.3 V
F28004x Control Card
F28004x Control Card
SN6501-Q1
G8
Ic
Ib
Ia
Ineu
Ic
Ib
Ia
15 V & -4 V
15 V & -4 V
15 V & -4 V
G1
G2
G3
G4
G5
G6
PFC Vout
Hall
Sensor
Hall Sensor
x 3
La
Lb
Lc
ISO7721-Q
Fault
Reset
5 V
G7
15 V & -4 V
UCC21520-Q1
4 × TIDA-01605
G1 G2 G3 G4 G5 G6 G7 G8
1
ZHCU459A–March 2018–Revised August 2018
TIDUE54 — http://www-s.ti.com/sc/techlit/TIDUE54
版权 © 2018, Texas Instruments Incorporated
效率为
98.6%
且适用于
HEV/EV
车载充电器的
6.6kW
图腾柱
PFC
参考设计
TI Designs
::
TIDA-01604
效效率率为为
98.6%
且且适适用用于于
HEV/EV
车车载载充充电电器器的的
6.6kW
图图腾腾柱柱
PFC
参参考考设设计计
说说明明
此参考设计介绍了适用于车载充电器的 6.6kW 图腾柱
(TTPL) 无桥功率因数校正 (PFC) 解决方案。功率级由
C2000™微控制器 (MCU) 通过 SiC 隔离式栅极驱动器
实现碳化硅 (SiC) MOSFET 的驱动。此设计采用了三相
交错技术并在连续导通模式 (CCM) 中运行,在 240V 输
入电压和 6.6kW 全功率下可实现 98.60% 的效率。
C2000 控制器可实现切相和自适应死区时间控制,从而
改善轻载条件下的功率因数。栅极驱动器板(参见
TIDA-01605)实现了增强型隔离,可承受超过 100V/ns
的共模瞬态抗扰度 (CMTI)。栅极驱动器板还包含两级关
断电路,可在短路情况下保护 MOSFET 抵御电压过
冲。
资资源源
TIDA-01604 设计文件夹
UCC21520-Q1 产品文件夹
TMS320F280049 产品文件夹
UCC28700-Q1 产品文件夹
TL1963A-Q1 产品文件夹
ISO7731-Q1 产品文件夹
C2000WARE-
DIGITALPOWER-SDK
工具文件夹
咨询我们的 E2E™ 专家
特特性性
• 高功率密度、高效率 PFC 设计,可为高达 6.6kW
的系统供电
• SiC MOSFET 具有 TI 驱动器,能够为客户提供更高
的集成度
• 具有增强型隔离和两级关断保护功能的半桥型和紧
凑型隔离式栅极驱动器
• 完全数字化控制,通过高性能 C2000™ 控制器实现
先进的控制方案
• 峰值效率为 98.86%,功率因素大于 0.99,且总谐波
失真 (THD) 小于 2%
• 三相交错运行方式,具有切相控制功能
• 400V 至 600V 的可编程输出电压
应应用用
• HEV/EV 牵引逆变器
• HEV/EV 车载充电器
• 电子控制单元
• HEV/EV 直流/直流转换器
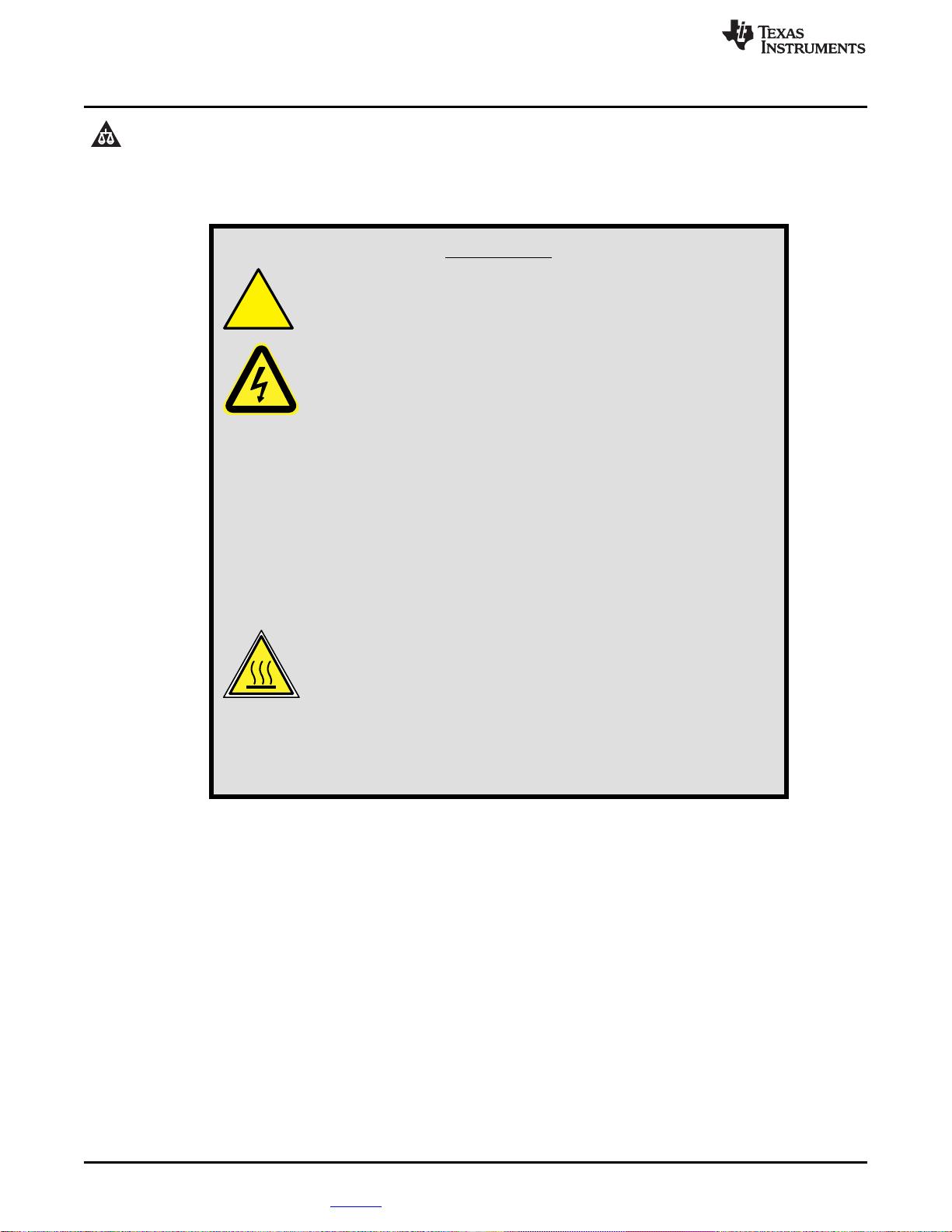
!
System Description
www.ti.com.cn
2
ZHCU459A–March 2018–Revised August 2018
TIDUE54 — http://www-s.ti.com/sc/techlit/TIDUE54
版权 © 2018, Texas Instruments Incorporated
效率为
98.6%
且适用于
HEV/EV
车载充电器的
6.6kW
图腾柱
PFC
参考设计
该 TI 参考设计末尾的重要声明表述了授权使用、知识产权问题和其他重要的免责声明和信息。
1 System Description
WARNING
Do not leave the device powered when unattended.
High voltage! There are accessible high voltages present
on the board. Electric shock is possible. The board operates at
voltages and currents that may cause shock, fire, or injury if not
properly handled. Use the equipment with necessary caution and
appropriate safeguards to avoid injury or damage to property. For
safety, use of isolated equipment with overvoltage and overcurrent
is highly recommended. TI considers it the user's responsibility to
confirm that the voltages and isolation requirements are identified
and understood before energizing the board or simulation. When
energized, do not touch the design or components connected to
the design.
Hot surface! Contact may cause burns. Do not touch!
Some components may reach high temperatures > 55°C when the
board is powered on. The user must not touch the board at any
point during operation or immediately after operating, as high
temperatures may be present.
1.1 Benefits of Totem-Pole Bridgeless PFC
All plug-in hybrid electric vehicles (PHEVs) require an onboard charger (OBC) between the power grid and
the high-voltage battery pack located inside the vehicle. Implementing a power factor correction (PFC)
converter is mandatory to connect directly to the power grid for AC/DC power conversion and maximize
the real power that flows to the downstream DC/DC converters.
Conventional PFC converters implement a passive diode bridge for rectification, which is now known as a
passive PFC technique. The advantages of such a scheme are: simple design, reliability, slow-system
control loop, and low cost. However, the disadvantages are also very obvious: the passive components
are heavy with a low-power factor and generate significant power losses, which results in bulky heat sinks
and a lot of heat dissipation. Further investigation into the matter shows that an input bridge consumes
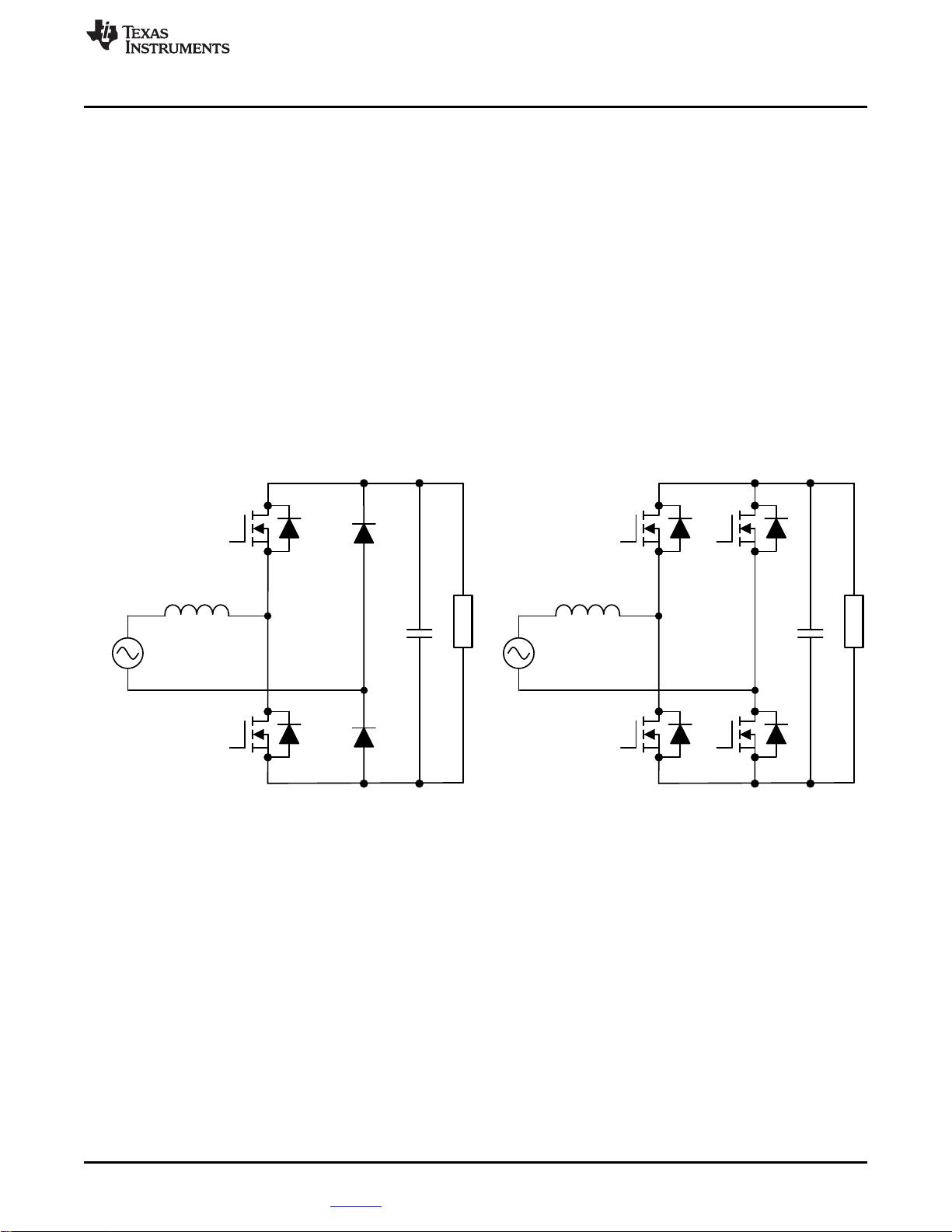
Power Grid
V
AC
Load
SiC
1
SiC
2
Si
1
S
i2
L
(b)
+
-
Power Grid
V
AC
Load
SiC
1
S
2
D
1
D
2
i
L
(a)
+
-
www.ti.com.cn
System Description
3
ZHCU459A–March 2018–Revised August 2018
TIDUE54 — http://www-s.ti.com/sc/techlit/TIDUE54
版权 © 2018, Texas Instruments Incorporated
效率为
98.6%
且适用于
HEV/EV
车载充电器的
6.6kW
图腾柱
PFC
参考设计
approximately 2% of the input power at the low line of a wide mains application. If the designer can
suppress one of the series diodes, then they can save 1% of the input power, which allows the efficiency
to rise from 94% to 95% (Turchi; Dalal; Wang; Lenck 2014). Due to previously-mentioned drawbacks, the
power rating of bridged traditional PFCs is limited under hundreds of watts, especially in a hybrid-electric
vehicle (HEV) or electric vehicle (EV) where reduced space and weight are the key design parameters.
As a result, the trend continues to move toward a bridgeless architecture with the elimination of the
traditional diode bridge. The OBC is based on a silicon power device and has limitations such as low
efficiency, low power density, and high weight. With the advantages of the SiC MOSFET, the designer can
greatly improve these limitations by utilizing the superior performance of fast switching, low reverse
recovery charge, and a low R
DS(ON).
图 1 shows the basic structure of the totem-pole bridgeless PFC boost rectifier. The component consists
of a boost inductor, two high-frequency boost SiC switches (SiC
1
and SiC
2
), and two components for
conducting current at the line frequency. The line frequency components can be two slow diodes, as 图 1
shows. Side (A) shows two silicon MOSFETs (Si
1
and Si
2
). Side (B) shows that the use of Si
1
and Si
2
further increases the efficiency.
图图 1. Totem-Pole Bridgeless PFC Boost Converter Topology:
(A) Diode for Line Rectification (B) MOSFET for Line Rectification
The inherent issue in the totem-pole PFC is the operation mode transition at the AC voltage zero-crossing.
When the AC input changes from the positive half line to the negative half line at the zero-crossing, the
duty ratio of the low-side high-frequency switch SiC
2
changes from 100% to 0%, and the duty cycle of SiC
1
changes from 0% to 100%. Because of the slow reverse recovery of the high-side diode (or body diode of
the MOSFET), the voltage at the cathode of D
2
cannot jump from ground to DC+ voltage instantly (this
causes a large current spike). Because of this issue, the designer cannot use an Si MOSFET in a
continuous-conduction mode (CCM) totem-pole PFC. Therefore SiC
1
and SiC
2
must be either SiC
MOSFET or gallium nitride (GaN) field-effect transistors (FETs), which have a low reverse recovery.
The biggest advantage of the totem-pole PFC is the reduced power losses in the conduction path. 表 1
shows the device comparison between a conventional PFC and a totem-pole PFC.
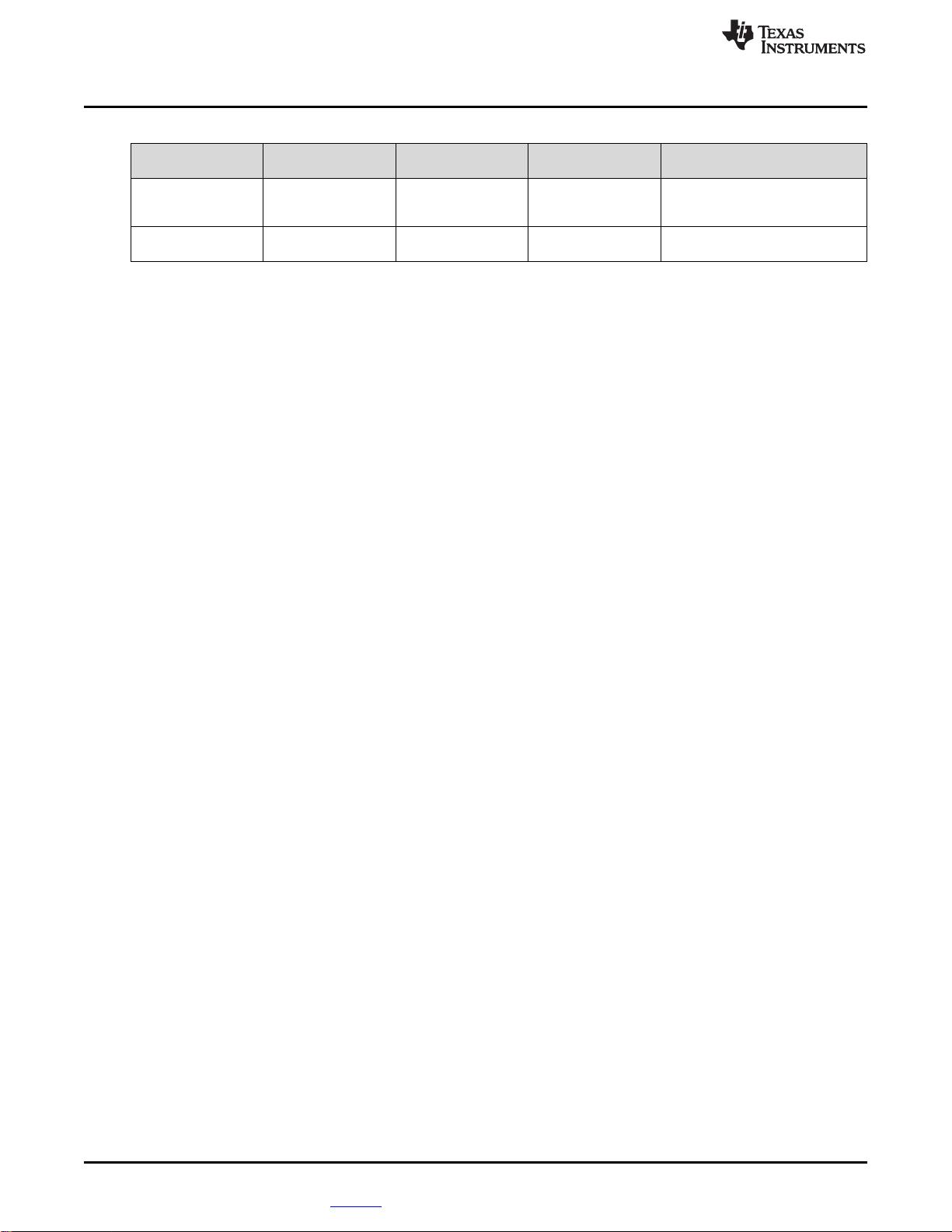
System Description
www.ti.com.cn
4
ZHCU459A–March 2018–Revised August 2018
TIDUE54 — http://www-s.ti.com/sc/techlit/TIDUE54
版权 © 2018, Texas Instruments Incorporated
效率为
98.6%
且适用于
HEV/EV
车载充电器的
6.6kW
图腾柱
PFC
参考设计
表表 1. Device Comparison of Conventional Bridged PFC and Totem-Pole Bridgeless PFC
PARAMETER
LOW-FREQUENCY
DIODES
HIGH-FREQUENCY
DIODES
HIGH-FREQUENCY
SWITCHES
CONDUCTION PATHS
Conventional bridged
PFC
Four One One
Two low-speed diodes + one
switch or (two low-speed diodes +
one high-speed diode)
Totem-pole bridgeless
PFC
Two Zero Two
One high-speed SiC switch + one
low-speed Si (or SiC) MOSFET
The following list summarizes the benefits of the totem-pole PFC:
• Although the conventional PFC boost converter is the most popular topology, its efficiency suffers from
the conduction losses of the front-end diode bridge rectifier and it is not bidirectional. A totem-pole PFC
is inherently capable of bidirectional operation.
• Bridgeless PFC boost converters greatly reduce the number of diodes, increase the power density, and
increase the efficiency.
• This PFC is superior in terms of: high efficiency, small common mode noise, small AC current ripple,
small reverse recovery current, and fewer components.
• The low reverse recovery charge of the SiC body diode and the low turnon resistance of the SiC
MOSFET make the converter an efficient and cost-effective solution for bidirectional onboard chargers.
1.2 Totem-Pole Bridgeless PFC Operation
The totem-pole PFC operates in the positive and negative cycles of the AC mains input, respectively, and
determines the current flow depending on how the high frequency SiC MOSFETs are switched (see 图 2
and 图 3, respectively).
The high-frequency SiC MOSFETs together with the inductor create a synchronous mode boost converter.
During the positive half cycle, S
2
is the boost switch which is driven with duty cycle D and S
1
is driven with
a complementary pulse-width modulation (PWM) signal (1-D). 图 2 (A) shows the direction in which the
current flows. Similarly, during the period when S
2
is switched with 1-D, S
1
is switched with D; 图 2 (B)
shows the direction in which the current flows. Note that, during this cycle, S
D2
conducts continuously.
During the negative half cycle, the operation is similar except that the role of the high-side- and low-side,
high-frequency switches are swapped. 图 3 shows the direction in which the current flows. Note that,
during this cycle, S
D1
conducts continuously.
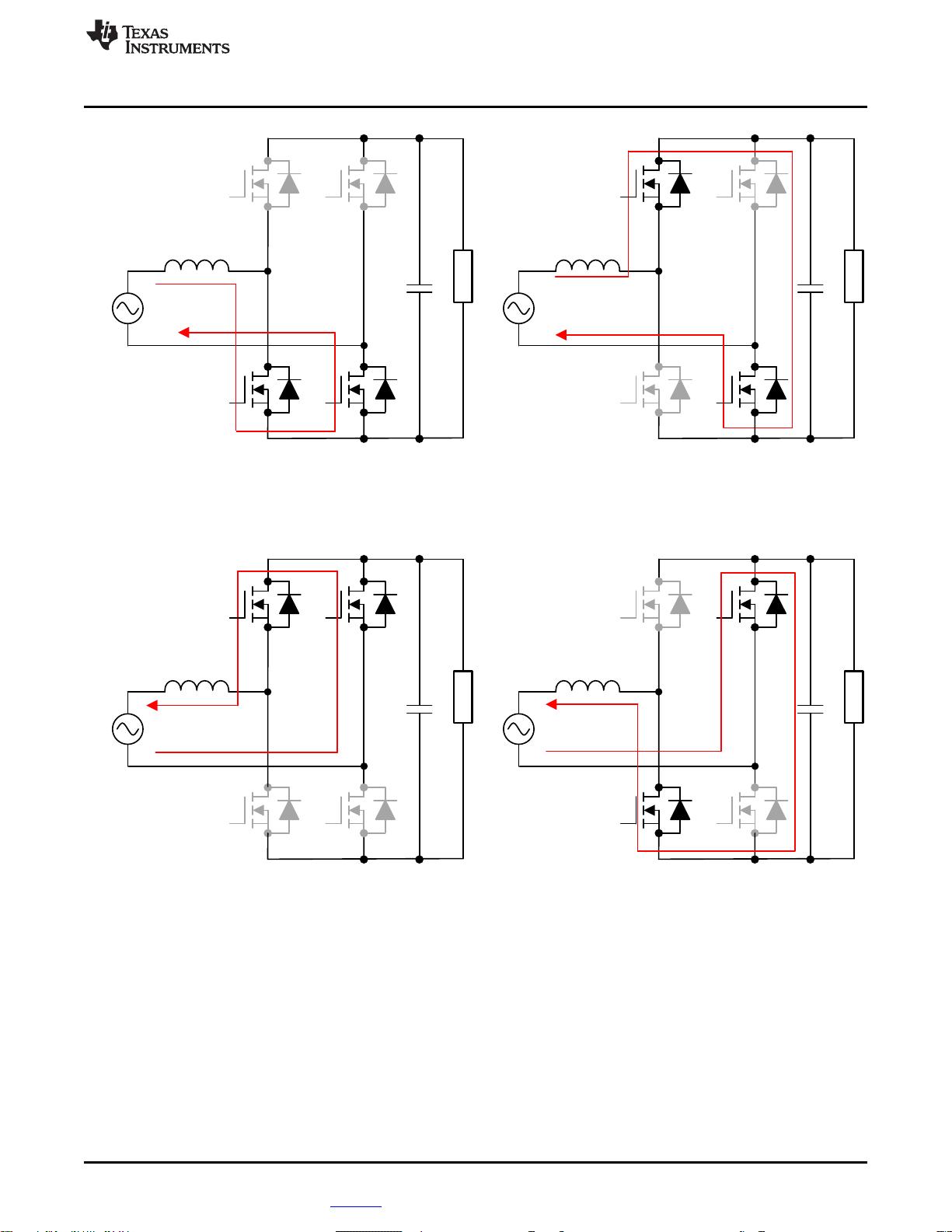
Power Grid
V
AC
Load
S
1
S
2
S
D1
S
D2
L
(b)
+
-
Power Grid
V
AC
Load
S
1
S
2
S
D1
S
D2
L
(a)
+
-
Power Grid
V
AC
Load
S
1
S
2
S
D1
S
D2
L
(b)
+
-
Power Grid
V
AC
Load
S
1
S
2
S
D1
S
D2
L
(a)
+
-
www.ti.com.cn
System Description
5
ZHCU459A–March 2018–Revised August 2018
TIDUE54 — http://www-s.ti.com/sc/techlit/TIDUE54
版权 © 2018, Texas Instruments Incorporated
效率为
98.6%
且适用于
HEV/EV
车载充电器的
6.6kW
图腾柱
PFC
参考设计
图图 2. Totem-Pole Bridgeless PFC Operation During Positive Half Cycle:
(A) While S
2
is Switched ON (B) While S
2
is Switched OFF
图图 3. Totem-Pole Bridgeless PFC Operation During Negative Half Cycle:
(A) While S
1
is Switched ON (B) While S
1
is Switched OFF
This reference design uses an SiC MOSFET (C3M0065100K from Wolfspeed) and TI’s C2000™
Piccolo™ (TMS320F280049) high-performance MCU. The high-frequency SiC MOSFETs operate at a
100-kHz switching frequency and the pair of Si MOSFETs operate at the line frequency (approximately
45 Hz to 60 Hz). Thus the conduction path includes one SiC switch and one low-frequency Si switch with
significantly-reduced conduction losses. Use three-channel interleaving to reduce conduction loss and
input current ripple. Test results demonstrate a high efficiency above 98.86% and confirm that the
advanced features of the controller function, such as phase shedding and adaptive dead-time control.
剩余76页未读,继续阅读
资源评论
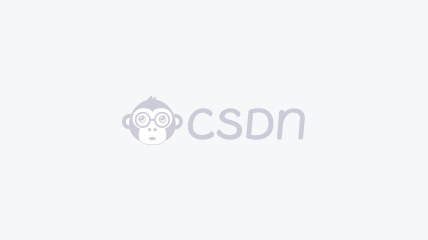
- #完美解决问题
- #运行顺畅
- #内容详尽
- #全网独家
- #注释完整
- 吉利吉利2023-07-24对于初学者来说,这份指南易于理解,语言简洁明了,能够帮助他们快速入门车载充电器设计领域。
- 月小烟2023-07-24这份指南提供了详实而实用的信息,对于设计车载充电器的人来说是一份不可多得的参考。
- 精准小天使2023-07-24该文件全面介绍了TI 6.6kw车载充电器的设计方案,让人能够深入了解其中的技术细节。
- 王元祺2023-07-24指南中的案例分析和示意图非常实用,能够帮助读者更好地理解和应用相关知识。
- 永远的122023-07-24这份文件对于解决实际问题提供了有价值的建议和指导,减少了设计者在实践中遇到的困惑和错误。

起名真TM的难
- 粉丝: 0
- 资源: 4
上传资源 快速赚钱
我的内容管理 展开
我的资源 快来上传第一个资源
我的收益
登录查看自己的收益我的积分 登录查看自己的积分
我的C币 登录后查看C币余额
我的收藏
我的下载
下载帮助

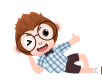
最新资源
- 重磅推荐-2024全新Langchain大模型AI应用与多智能体实战开发(视频教程+源码+课件).zip
- 线性时变模型预测控制LTV-MPC在Matlab+Simulink环境下的应用与仿真研究(2020b版),基于Matlab/Simulink的线性时变模型预测控制(LTV-MPC)仿真研究(2020
- "《基于Matlab+YALMIP+Gurobi的配电网两阶段鲁棒故障恢复策略复现与实践》-中科院一区期刊IEEE Transactions on Power Systems中的顶刊成果详解与实现"
- 代码项目文档:早报信息生成与推送系统
- "低速永磁同步电机转子偏心对运行特性及振动噪声影响的研究","转子偏心对低速永磁同步电机性能影响的研究:从齿槽转矩到振动噪声的全面分析",转子偏心对低速永磁同步电机运行特性影响的研究 低速直驱永磁同步
- RTCA DO-311A-2017可充电锂电池和电池系统的最低运行性能标准
- 华为项目管理10大模板(可直接套用)
- 基于大蔗鼠优化策略:改进的大蔗鼠优化算法IGCRA与自然觅食行为结合的元启发式算法研究,改进的IGCRA:三大策略驱动的大蔗鼠优化算法(Greater Cane Rat Algorithm with
- Java期末作业基于javafx实现的任务管理软件源代码+数据库
- 1_base.apk.1
- 界面 多语言动态 切换显示;使用Language.ini进行语言配置; 建立Language-CN.ini,Language-EN.ini对照表,切换内容包括:菜单及控件,文中提示信息等
- 华为ICT大赛2023-2024全国总决赛网络赛道实验试题
- 基于MATLAB的变压器剩磁计算程序:计算输出磁通波形与剩磁值,MATLAB程序在计算变压器剩磁时的输出波形及其计算结果的应用分析,MATLAB程序 变压器剩磁计算 输出磁通波形 计算剩磁值 ,MAT
- CNN-LSSVM卷积神经网络最小二乘支持向量机多变量多步预测,光伏功率预测(Matlab完整源码和数据)
- C语言开发-销售预测项目案例分享
- 微信小程序餐厅扫码点餐项目源码
资源上传下载、课程学习等过程中有任何疑问或建议,欢迎提出宝贵意见哦~我们会及时处理!
点击此处反馈


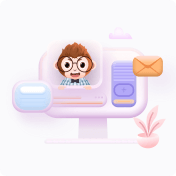
安全验证
文档复制为VIP权益,开通VIP直接复制
