
wsbhm62
- 粉丝: 7
- 资源: 21万+
最新资源
- Java毕业设计-基于springboot+Vue的校园组团平台2(附源码,部署教程).zip
- 基于java+ssm+mysql的车辆出租管理系统 源码+数据库+论文(高分毕设项目).zip
- 基于java+ssm+mysql的儿童教育网站 源码+数据库+论文(高分毕设项目).zip
- 基于java+ssm+mysql的电影购票系统 源码+数据库+论文(高分毕设项目).zip
- 本项目在脱敏的情况下整理出常见的报告模板、红蓝对抗技巧、渗透测试方法大全、大型会议PPT
- 基于源荷双重不确定性的虚拟电厂日前鲁棒优化经济调度策略,MATLAB代码:计及源-荷双重不确定性的电厂日前鲁棒优化调度 关键词:电厂 微网调度 鲁棒调度 源荷不确定性 日前经济调度 参考文档
- Java毕业设计-基于SpringBoot+Vue的校园二手书交易平台的设计与实现2(附源码,部署教程).zip
- Java毕业设计-基于SpringBoot+Vue的的信息技术知识赛系统的设计与实现(附源码,部署教程).zip
- Java毕业设计-基于SpringBoot+Vue的的信息技术知识竞赛系统的设计与实现(附源码,部署教程).zip
- Java毕业设计-基于SpringBoot+Vue的的信息技术知识竞赛系统的设计与实现2(附源码,部署教程).zip
- Java毕业设计-基于springboot+Vue的校园疫情防控系统(附源码,部署教程).zip
- Java毕业设计-基于springboot+Vue的校园外卖服务系统设计与实现(附源码,部署教程).zip
- 基于java+ssm+mysql的高校学生课堂考勤系统 源码+数据库+论文(高分毕设项目).zip
- 基于java+ssm+mysql的公司宣传网站 源码+数据库+论文(高分毕设项目).zip
- 基于java+ssm+mysql的高校大学生党建系统 源码+数据库+论文(高分毕设项目).zip
- 基于源荷双重不确定性的虚拟电厂日前鲁棒优化经济调度策略,MATLAB代码:计及源-荷双重不确定性的电厂日前鲁棒优化调度 关键词:电厂 微网调度 鲁棒调度 源荷不确定性 日前经济调度 参考文档
资源上传下载、课程学习等过程中有任何疑问或建议,欢迎提出宝贵意见哦~我们会及时处理!
点击此处反馈


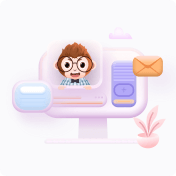