
拉拉庸
- 粉丝: 21
- 资源: 66万+
最新资源
- "基于电阻抗层析成像(EIT/ECT)技术的正逆问题联合仿真教学研究:使用Comsol与Matlab联合求解正问题,Matlab求解逆问题,针对不同模型建模与求解方法探讨,电极数量灵活可变(8、16、
- bgp设计与实现(英文版)
- COMSOL模拟多裂纹水力压裂扩展:拉伸与压缩破坏的实时可视化研究,comsol多裂纹水力压裂扩展,可以实现拉伸和压缩下的破坏 ,comsol多裂纹; 水力压裂扩展; 拉伸破坏; 压缩破坏,"CO
- 基于Comsol模拟的高斯热源激光打孔蚀除过程仿真研究:运用变形几何与固体传热技术实现单脉冲通孔数值模拟分析,基于Comsol激光打孔,利用高斯热源脉冲激光对材料进行蚀除过程仿真,其中运用了变形几何和
- 验证正确性并已全面考虑高斯热源及熔覆模型研究-模型框架在科研中直接可用的激光熔覆仿真系统,圆形光斑激光熔覆comsol仿真模型,模型已通过实验验证了正确性,确保模型一定正确可用于科研 高斯热源,马
- 基于Comsol激光超声技术的铝板表面波检测:热效应驱动的瞬态声场与位移信号分析,comsol激光超声表面波检测 如图,通过激光的热效应,在铝板中产生超声波,瞬态声场如图1 图2为含裂纹和不含时在(
- Comsol锂枝晶加流动耦合模型:探究电势场浓度生长过程中的流场改变对枝晶形貌的影响机制 ,comsol 锂枝晶加流动耦合电势场模型,浓度场生长过程中添加流场,改变枝晶形貌 ,关键词:COMSOL
- bgp设计与实现(中文版)
- 基于comsol的三维电化学-热-应力耦合锂离子电池模型:全尺度计算三场耦合效应,输出电信号、温度及应力分布与电池瞬态位移情况,comsol三维电化学-热-应力耦合锂离子电池模型 全尺度计算三场耦合
- 《Comsol 3D拓扑光子晶体能带计算方法及案例研究-基于超材料体系的体系特性分析》,comsol 3D三维拓扑光子晶体能带计算,体系为超材料,文件包含带隙打开时的能带(原文FIG.1E)mph
- Comsol油浸式变压器多物理场耦合仿真研究:探索内部热点温度与油流速度分布的详细模型与学习资料,Comsol油浸式变压器电磁﹣温度﹣流体多物理场耦合仿真;可以得到变压器稳定运行时内部热点温度及油流速
- "COMSOL模拟下的三维平面相控阵聚焦超声技术:声程差法驱动的高分辨率成像研究",COMSOL 平面相控阵聚焦超声仿真 三维平面相控阵聚焦超声技术结合了相控阵和聚焦原理,通过多个超声发射和接收元件的
- "基于Comsol的完全耦合水力压裂模型:应力-渗流-损伤一体化模拟与MATLAB随机参数生成技术",comsol水力压裂应力-渗流-损伤 本模型用Comsol模拟注水过程中的岩石损伤,考虑完全耦合模
- "COMSOL混凝土碳化模型:基于PDE模块的物理场景复现与偏微分方程变量模型研究",COMSOL混凝土碳化模型,使用PDE建模 PDE模块(系数偏微分方程) 物理场景,研究荷载作用下混凝土碳化情况
- 基于磁流体方程的Comsol电弧放电模型:多物理场耦合模拟电磁热流体动态行为,comsol电弧放电模型,采用磁流体方程模拟电弧放电现象,耦合电磁热流体以及电路多个物理场 一共四个模型 ,comsol电
- "Kagome晶格角态几何建模的随机位移及其在Comsol App开发器中的高效编辑-无需Matlab依赖的简化文件方案",kagome晶格角态随机位移几何建模,在comsol中app开发器中编辑
资源上传下载、课程学习等过程中有任何疑问或建议,欢迎提出宝贵意见哦~我们会及时处理!
点击此处反馈


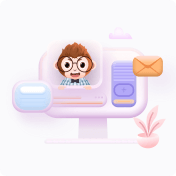