
拉拉庸
- 粉丝: 21
- 资源: 66万+
最新资源
- 基于微信小程序的校园商铺系统--论文-微信小程序毕业项目,适合计算机毕-设、实训项目、大作业学习.zip
- 家政项目小程序+ssm-微信小程序毕业项目,适合计算机毕-设、实训项目、大作业学习.rar
- 基于微信小程序的校园综合服务平台ssm-微信小程序毕业项目,适合计算机毕-设、实训项目、大作业学习.rar
- 驾校管理系统+ssm-微信小程序毕业项目,适合计算机毕-设、实训项目、大作业学习.rar
- 健身房私教预约微信小程序+ssm-微信小程序毕业项目,适合计算机毕-设、实训项目、大作业学习.rar
- 基于微信小程序的新生报到系统--论文-微信小程序毕业项目,适合计算机毕-设、实训项目、大作业学习.zip
- 基于微信小程序的新生自助报到系统--论文-微信小程序毕业项目,适合计算机毕-设、实训项目、大作业学习.zip
- win32汇编环境,对话框程序中模态对话框与非模态对话框的区别
- 基于微信小程序的新生报到系统的设计与实现ssm-微信小程序毕业项目,适合计算机毕-设、实训项目、大作业学习.rar
- 警务辅助人员管理系统+ssm-微信小程序毕业项目,适合计算机毕-设、实训项目、大作业学习.rar
- 酒店管理系统+ssm-微信小程序毕业项目,适合计算机毕-设、实训项目、大作业学习.rar
- 健身房私教预约系统+ssm-微信小程序毕业项目,适合计算机毕-设、实训项目、大作业学习.rar
- 基于微信小程序的药店管理系统-微信小程序毕业项目,适合计算机毕-设、实训项目、大作业学习.zip
- 基于微信小程序的学习资料销售平台--论文-微信小程序毕业项目,适合计算机毕-设、实训项目、大作业学习.zip
- 基于微信小程序的学生签到系统设计与实现ssm-微信小程序毕业项目,适合计算机毕-设、实训项目、大作业学习.rar
- 客家菜餐馆点菜系统+ssm-微信小程序毕业项目,适合计算机毕-设、实训项目、大作业学习.rar
资源上传下载、课程学习等过程中有任何疑问或建议,欢迎提出宝贵意见哦~我们会及时处理!
点击此处反馈


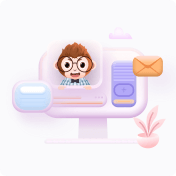