
weixin_38743481
- 粉丝: 698
- 资源: 4万+
最新资源
- 基于蒙特卡洛模拟与半不变量法的电力系统概率潮流计算程序:考虑光伏不确定性,分析IEEE34节点系统电压与潮流概率特性 ,电力系统随机潮流计算MATLAB程序包含蒙特卡洛模拟法与半不变量法,在光伏不确定
- mysql-installer-community-8.0.18.0.msi
- 深度学习驱动的电动车头盔佩戴检测系统:完整源码与数据集的集成解决方案,深度学习驱动的电动车头盔佩戴检测系统:完整源码与数据集的集成解决方案,基于深度学习YOLOv8+Pyqt5的电动车头盔佩戴检测系统
- IMDb 韩国电视剧及用户评论数据集.zip
- 无功补偿仿真实例: 使用Simulink与MATLAB仿真无功补偿SVG,附有详细文档,基于Simulink与Matlab的无功补偿SVG仿真研究-完整仿真过程与说明文档,无功补偿仿真,simuli
- C++实现扩展卡尔曼滤波器估计移动物体的位置和速度源码+使用教程(自动驾驶汽车项目).zip
- 軟體比對參考腳本,輸出電腦中的軟件和系統信息
- 基于DH参数的UR5机械臂PID轨迹跟踪控制及Simscape物理仿真:角度、速度、加速度与力矩分析,误差曲线展示,UR5机械臂PID轨迹跟踪控制技术:六自由度Simscape物理仿真与DH参数分析的
- 基于卡尔曼滤波跟踪自由落体的速度matlab源码实现-高度曲线(课程作业).zip
- 最佳阿尔茨海默氏症MRI数据集(99%准确率).zip
- E000704金融股权投资类企业网站模板+PHP+Mysql+易优+CMS+建站模板
- 将 Linux 系统配置成为一台 IPv4 路由器 具备 RIP、OSPF(单区域)和路由重分配功能
- 中国地图GeoJSON
- 自动生成爱心,让你的三八节表达爱意有乐趣
- 1737773274623_ NOUV1WnbhDPACrd11NUVOb14GN4+AF+wJggYPBDWg.jpg
- 让你的三八节表达爱意有乐趣,自动生成会动的爱心
资源上传下载、课程学习等过程中有任何疑问或建议,欢迎提出宝贵意见哦~我们会及时处理!
点击此处反馈


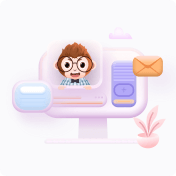