没有合适的资源?快使用搜索试试~ 我知道了~
Understanding Automotive Electronics 8th - Chapter 5
需积分: 9 14 下载量 174 浏览量
2018-03-13
19:04:55
上传
评论
收藏 4.6MB PDF 举报
温馨提示
The previous chapter introduced two critically important components found in any electronic control system: sensors and actuators. This chapter explains the operation of the sensors and actuators used throughout a modern car. Special emphasis is placed on sensors and actuators used for power train (i.e., engine and transmission) applications since these systems often employ the largest number of such devices. However, this chapter will also discuss sensors found in other subsystems on modern cars.
资源推荐
资源详情
资源评论
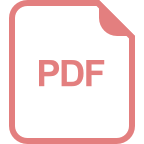
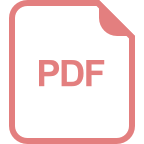
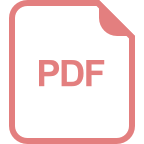
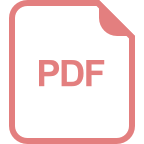
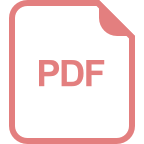
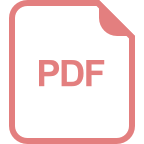
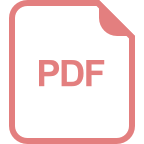
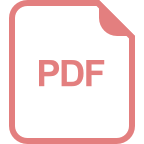
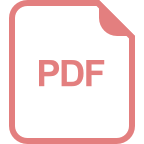
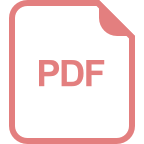
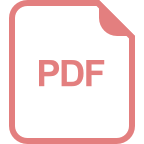
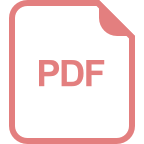
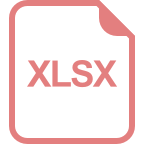
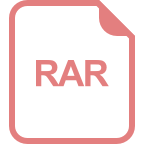
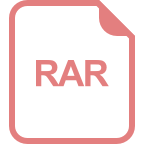
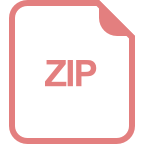
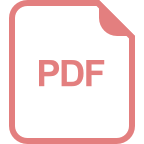
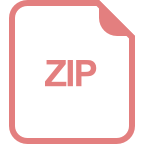
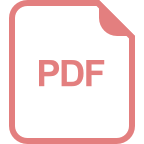
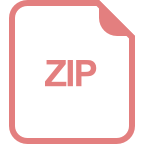
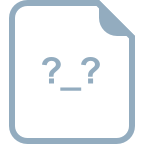
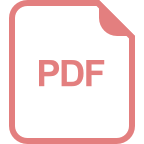
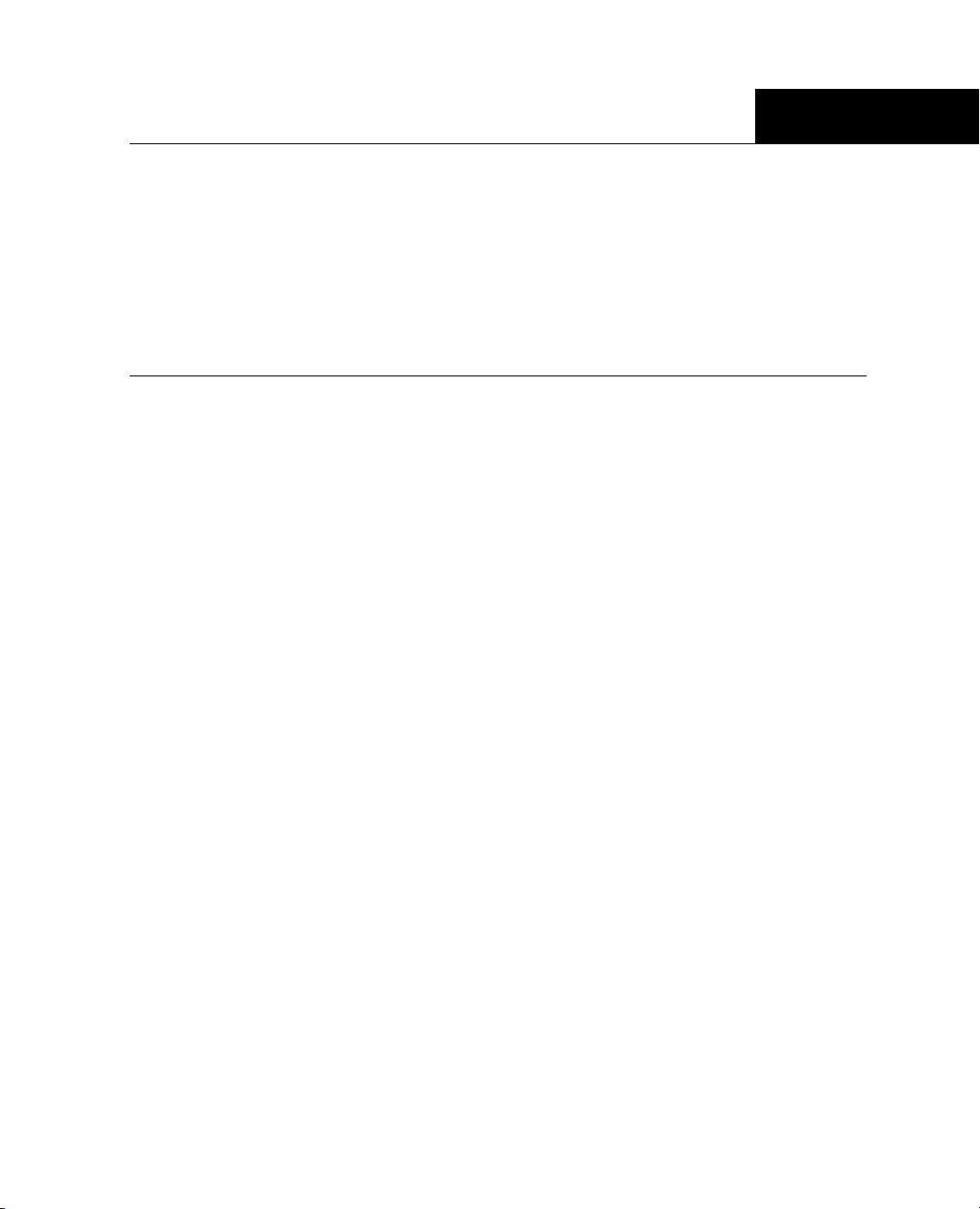
CHAPTER
SENSORS AND ACTUATORS
5
CHAPTER OUTLINE
Automotive Control System Applications of Sensors and Actuators ........................................................ 184
Variables to be Measured ..................................................................................................... 185
Airflow Rate Sensor ............................................................................................................. 186
Pressure Measurements ....................................................................................................... 191
Engine Crankshaft Angular Position Sensor ............................................................................ 194
Magnetic Reluctance Position Sensor .................................................................................... 195
Hall-Effect Position Sensor .................................................................................................. 205
Optical Crankshaft Position Sensor ....................................................................................... 208
Throttle Angle Sensor ......................................................................................................................... 211
Temperature Sensors ......................................................................................................................... 213
Typical Coolant Sensor ...................................................................................................................... 214
Sensors for Feedback Control ............................................................................................................. 215
Exhaust Gas Oxygen Sensor .................................................................................................. 215
Oxygen Sensor Improvements ............................................................................................... 220
Knock Sensors ................................................................................................................................... 221
Angular Rate Sensor .......................................................................................................................... 223
LIDAR ................................................................................................................................................ 227
Digital Video Camera ......................................................................................................................... 229
Flex-Fuel Sensor ................................................................................................................................ 235
Oscillator Methods of Measuring Capacitance ........................................................................ 239
Acceleration Sensor ............................................................................................................. 244
Automotive Engine Control Actuators ................................................................................................... 247
Fuel Injection ...................................................................................................................... 251
Exhaust Gas Recirculation Actuator ...................................................................................... 253
Variable Valve Timing ........................................................................................................................ 254
VVP Mechanism Model ........................................................................................................ 257
Electric Motor Actuators ..................................................................................................................... 258
Two-Phase Induction Motor .................................................................................................. 263
Brushless DC Motors ............................................................................................................ 266
Stepper Motors .................................................................................................................................. 268
Ignition System .................................................................................................................................. 268
Ignition Coil Operations ....................................................................................................... 269
Understanding Automotive Electronics. http://dx.doi.org/10.1016/B978-0-12-810434-7.00005-3
Copyright # 2017 Elsevier Inc. All rights reserved.
183
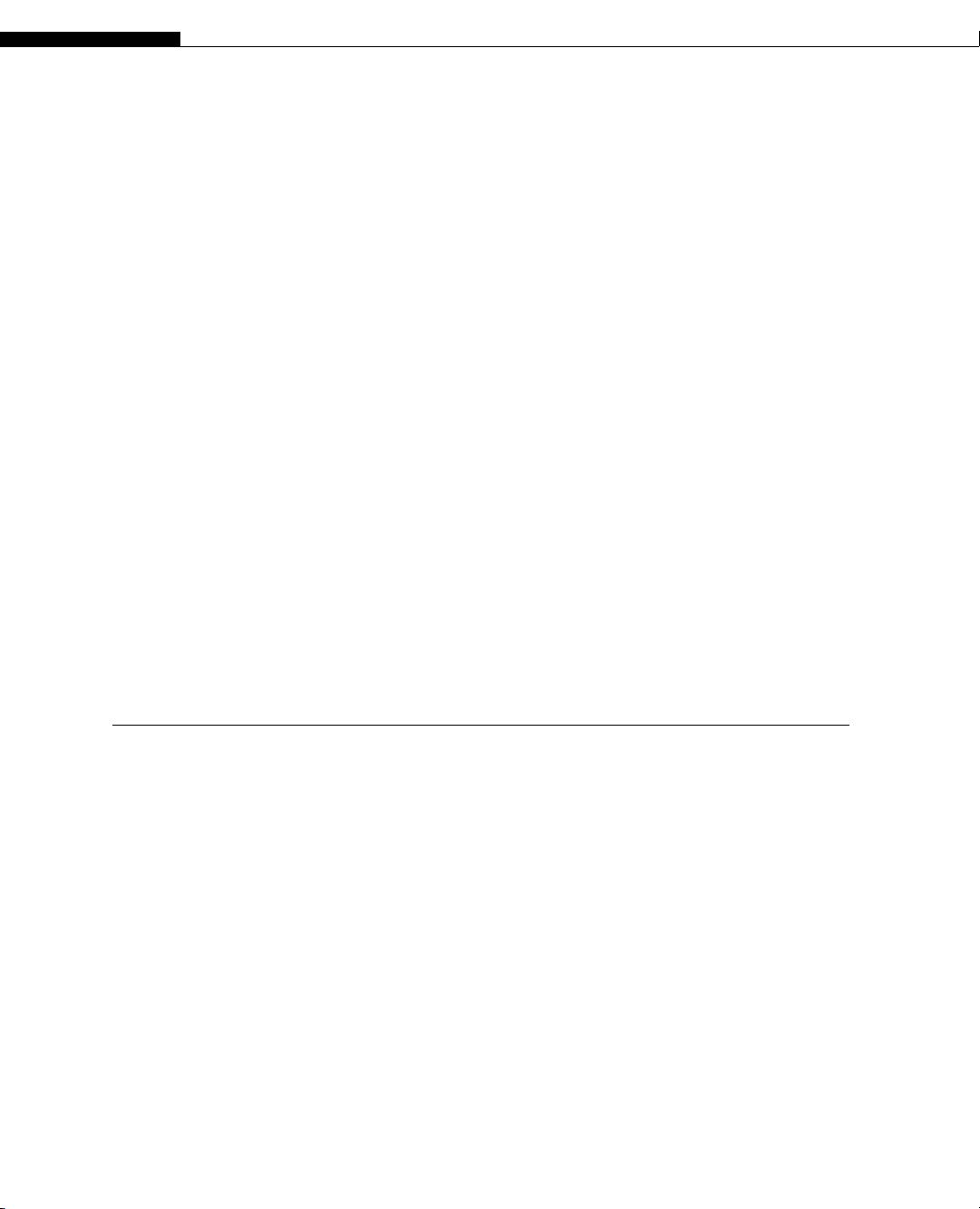
The previous chapter introduced two critically important components found in any electronic control
system: sensors and actuators. This chapter explains the operation of the sensors and actuators used
throughout a modern car. Special emphasis is placed on sensors and actuators used for power train
(i.e., engine and transmission) applications since these systems often employ the largest number of such
devices. However, this chapter will also discuss sensors found in other subsystems on modern cars.
In any control syst em, sensors provide measurements of important plant variables in a format suit-
able for the digital control system (often called an ECU). Similarly, actuators are electrically operated
devices that regulate inputs to the plant that directly controls its output. For examp le, as we shall see,
fuel injectors are electrically driven actuators that regulate the flow of fuel into an engine for engine
control applications.
In Appendix A, it is explained that fundamentally an electronic control system uses measurements
of the plant variable being regulated in the closed-loop mode of operation. The measured variable is
compared with a desired value (set point) for the variable to produce an error signal. In the closed-loop
mode, the electronic controller generat es output electrical signals that regulate inputs to the plant in
such a way as to reduce the error to zero. In the open-loop mode, it uses measurements of the key input
variable to calculate the desired control variable. Automotive instrumentation (as described in
Appendix A) also require s measurement of some variable. For either control or instrumentation appli-
cations, such measurements are made using one or more sensors. However, since control applications
of sensors demand more accurate sensor performance models, the following discussion of sensors will
focus on control applications. The reader should be aware, however, that many of the sensors discussed
below also can be used in instrumentation systems.
As will be shown throughout the remainder of this book, automotive electronics has man y examples
of electronic control in virtually every subsystem. Modern automotive electronic control systems use
microcontrollers based on microprocessors (as explained in Chapter 4) to implement almost all control
functions. Each of these subsystems requires one or more sensors and actuators in order to operate.
AUTOMOTIVE CONTROL SYSTEM APPLICATIONS OF SENSORS
AND ACTUATORS
In any control system application, sensors and actuators are, in many cases, the critical components for
determining system performance. This is especially true for vehicular control system applications. The
availability of appropriate sensors and actuators dictates the design of the control system and the type of
function it can perform.
The sensors and actuators that are available to a control system designer are not always what the
designer wants, because the idea l device may not be commercially available at acceptable costs. For
this reason, special signal proce ssors or interface circuits often are designed to adapt an available sensor
or actuator, or the control system is designed in a specific way to fit available sensors or actuators.
However, because of the large potential production run for automotive control systems, it is often
worthwhile to develop a sensor for a particular application, even though it may take a long and expen-
sive research project to do so.
Although there are many subsystems on automobiles that operate with sensors and act uators, we
begin our discussion with a survey of the devices for power train control. To motivate the discussion
of engine control sensors and actuators, it is helpful to review the variables measured (sensors) and the
184 CHAPTER 5 SENSORS AND ACTUATORS
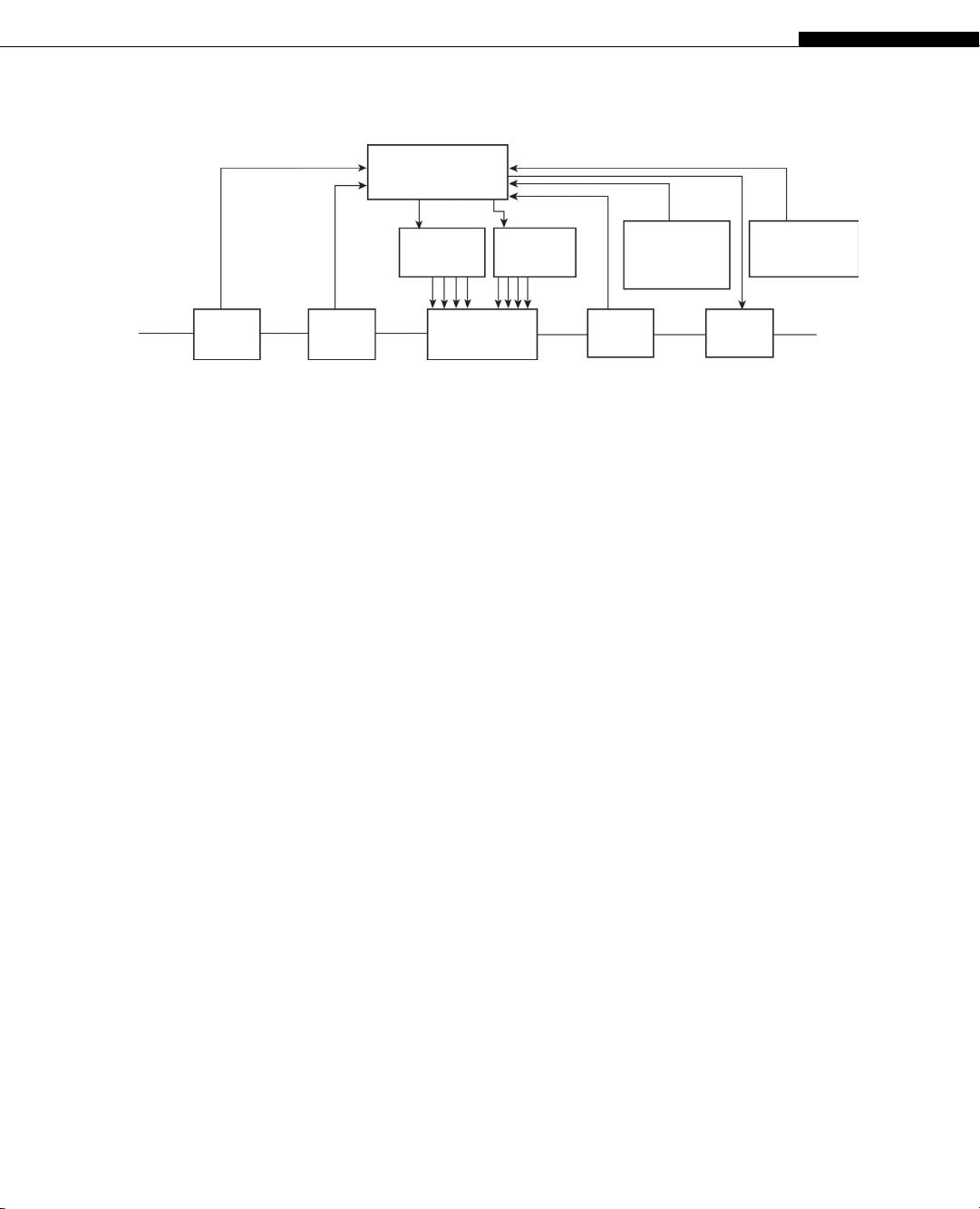
controlled variables (actuators). Fig. 5.1 is a simplified block diagram of a representative electronic
engine control system illustrating most of the relevant sensors used for engine control.
As explained in Chapter 6, the position of the throttle plate, sensed by the throttle position sensor
(TPS), directly regulates the airflow into the engine, thereby controlling output power. A set of fuel
injectors (one for each cylinder) delivers the correct amount of fuel to a corresponding cylinder during
the intake stroke under the control of the electronic engine controller to maintain the fuel/air mixture at
stoichiometry within a narrow tolerance band. A fuel injector is, as will presently be shown, one of the
important actuators used in automotive electronic application. The ignition control system fires each
spark plug at the appropriate time under control of the electronic engine controller. The exhaust gas
recirculation (EGR) is controlled by yet another output from the engine controller. All critical engine
control functions are based on measurements made by various sensors connected to the engine in an
appropriate way. Computations made within the engine controller based on these inputs yield output
signals to the actuators. We consider inputs (sensors) to the control system first, and then, we will dis-
cuss the outputs (actuators).
VARIABLES TO BE MEASURED
The set of variables sensed for any given power train is specific to the associated engine control con-
figuration. Space limitations for this book preclude a complete survey of all power train control systems
and relevant sensor and actuator selections for all car models. Nevertheless, it is possible to review a set
of possible sensors, which is done in this chapter, and to present representative examples of practical
digital control configurations, which is done in the next chapter.
The set of variables sensed in engine control includes the following:
1. Mass airflow (MAF) rate
2. Exhaust gas oxygen concentration
3. Throttle plate angular position
4. Crankshaft angular position/RPM
5. Camshaft angular position
6. Coolant temperature
Inlet
air
TPS
Engine
control
Fuel
injectors
Ignition
system
Crankshaft/
camshaft
position
sensor
Coolant
temperature
sensor
MAF Engine EGO EGR
FIG. 5.1 Representative electronic engine control system.
185AUTOMOTIVE CONTROL SENSORS AND ACTUATORS
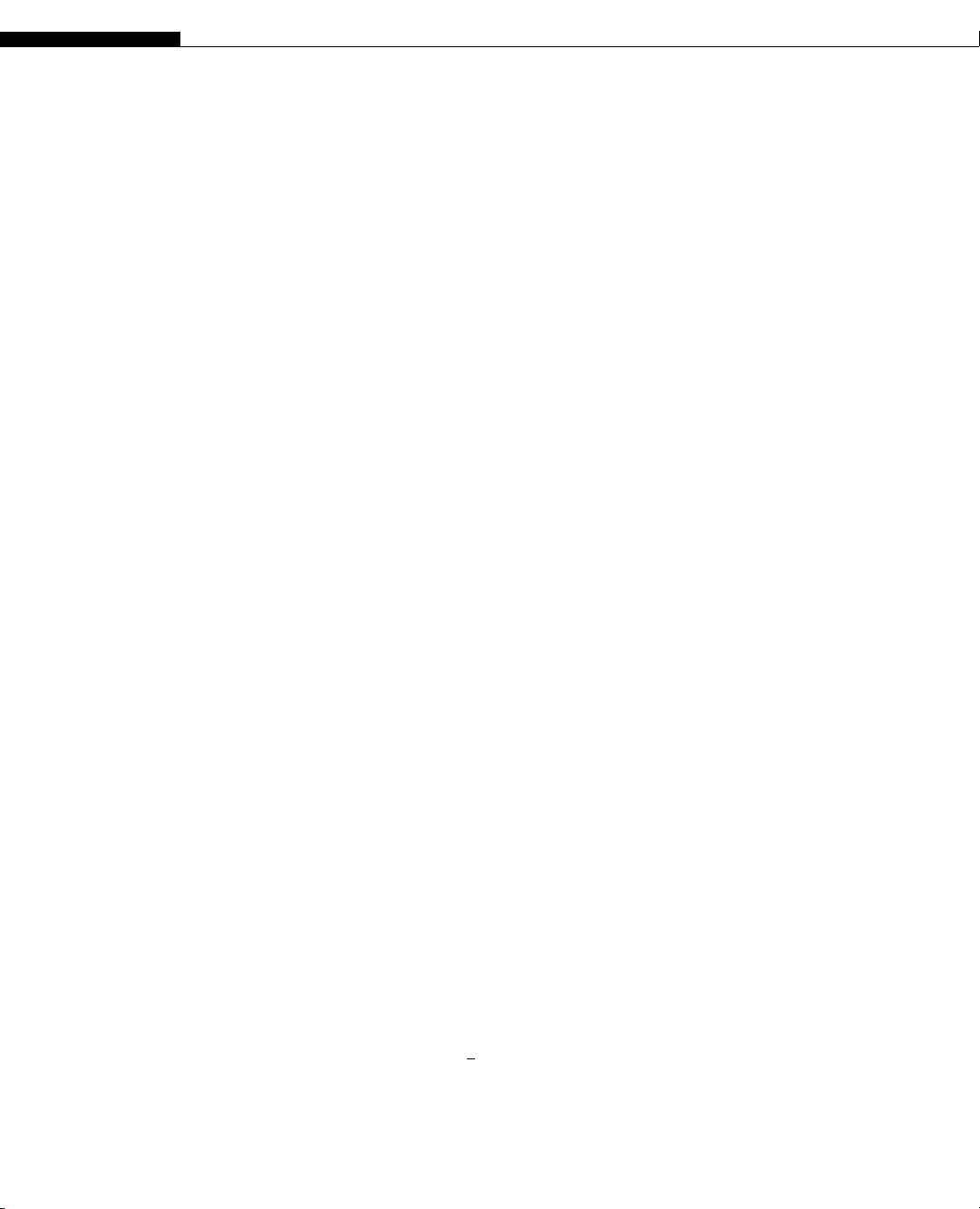
7. Intake air temperature
8. Ambient air pressure
9. Ambient air temperature
10. Manifold absolute pressure (MAP)
11. Differential exhaust gas pressure (relative to ambient)
12. Vehicle speed
13. Transmission gear selector position
14. Actual transmission gear in use
15. Various pressures
In addition to measurements of the above variables, engine control is also based on the status of the
vehicle as monitored by a set of switches. These switches include the following:
1. Air conditioner clutch engaged
2. Brake on/off
3. Wide open throttle
4. Closed throttle
5. Transmission gear selection
AIRFLOW RATE SENSOR
In Chapter 4, we showed that the correct operation of an electronically controlled engine operating with
government-regulated exhaust emissions requires a measurement of the mass flow rate of air
_
M
a
into
the engine. Throughout this book, the over dot in this notation implies time rate of change. The majority
of cars produced since the early 1990s use a relatively simple and inexpensive mass airflow rate (MAF)
sensor. This is normally mounted as part of the intake air assembly, where it measures airflow into the
intake manifold. It is a ruggedly packaged, single-unit sensor that includes solid-state electronic signal
processing. In operation, the MAF sensor generates a continuous signal that varies as a function of true
mass airflow
_
M
a
.
Before explaining the operation of the MAF, it is, perhaps, helpful to review the characteristics of
the inlet airflow into an engine. It has been shown in Chapter 4 that a four-stroke reciprocating engine
functions as an air pump with air pumped sequentially into each cylinder every two crankshaft revo-
lutions. The dynamics of this pumping process are such that the airflow consists of a fluctuating com-
ponent (at half the crankshaft rot ation frequency times the number of cylinders) superposed on a
quasisteady component. This latter component is a constant only for constant engine operation (i.e.,
steady power at constant RPM such as might be achieved at a constant vehicle speed on a level road).
However, automotive engines rarely operate at absolutely constant power and RPM. The quasisteady
component of airflow changes with load and speed. It is this quasisteady component of
_
M
a
tðÞthat is
measured by the MAF for engine control purposes. One way of characterizing this quasisteady-state
component is as a short-term time average over a time interval τ (which we denote
_
M
aτ
tðÞ) where
_
M
aτ
tðÞ¼
1
τ
ð
t
tτ
_
M
a
t
0
ðÞdt
0
(5.1)
186 CHAPTER 5 SENSORS AND ACTUATORS
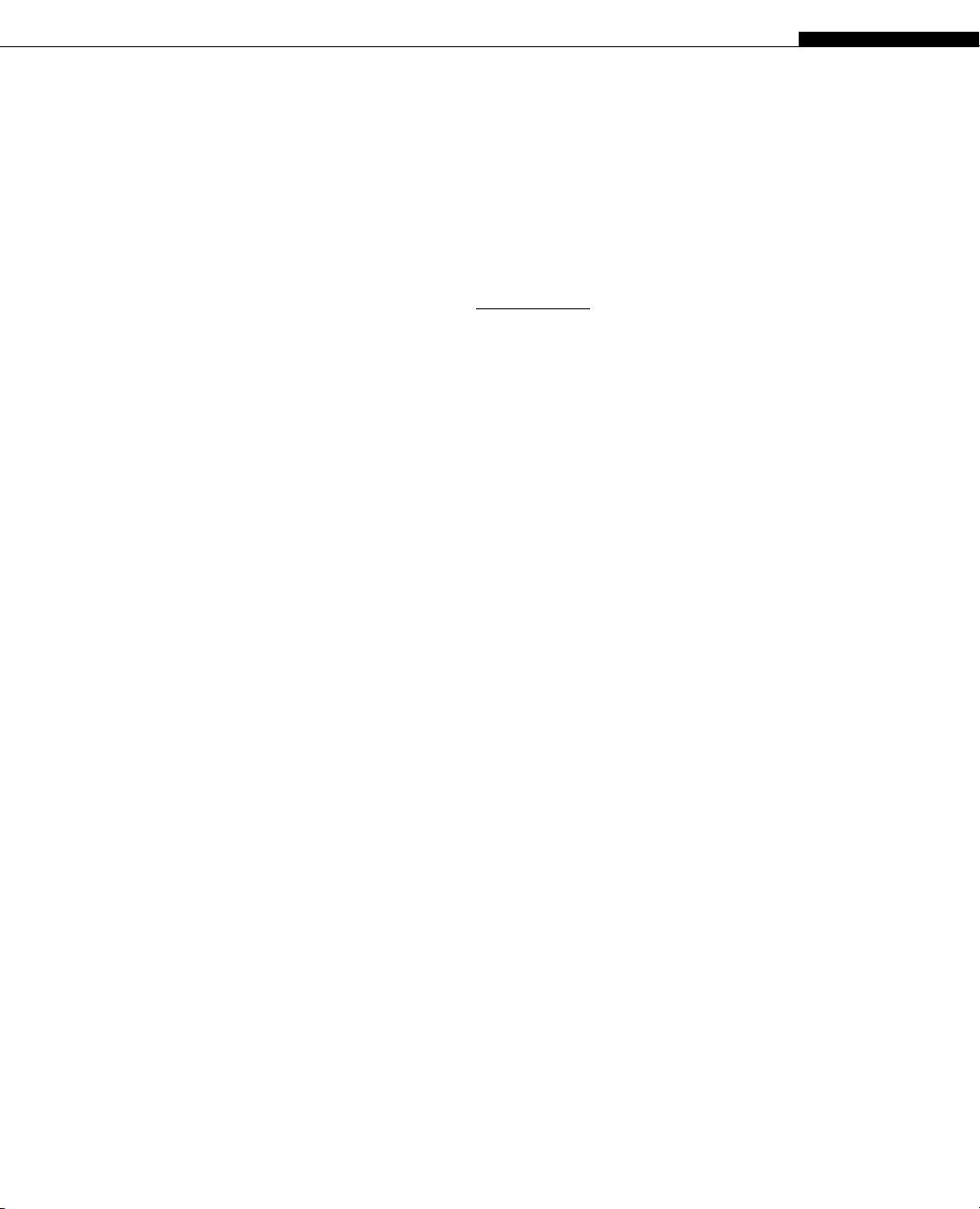
The integration interval (τ) must be long enough to suppress the time-varying component at the lowest
cylinder pumping frequency (e.g., idle RPM) yet short enough to preserve the transient characterist ics
of airflow associated with relatively rapid throttle position changes.
Alternatively, the quasisteady component of mass airflow can be represented by a low-pass-filtered
version of the instantaneous flow rate. Appendix A explains that a low-pass filter (LPF) can be char-
acterized (in continuous time) by an operational transfer function (H
LPF
(s)) of the form
H
LPF
sðÞ¼
b
o
+ b
1
s + ⋯ b
m
s
m
a
o
+ a
1
s + ⋯ a
n
s
n
(5.2)
where the coefficients determine the response characteristics of the filter. The filter bandwidth effec-
tively selects the equivalent time interval over which mass airflow measurements are averaged. Of
course, in practice with a digital power train control system, mass airflow measuremen ts are sampled
at discrete times, and the filtering is implemented as a discrete time transformation of the sampled data
(see Appendix B).
A typical MAF senso r is a variation of a classic airflow sensor that was known as a hot-wire an-
emometer and was used, for example, to measure wind velocity for weather forecasting and for various
scientific studies. In the typical MAF, the sensing element is a conductor or semiconductor thin-film
structure mounted on a substrate. On the air inlet side, a honeycomb flow straightener is mounted that
“smoothes” the airflow (causing nominally laminar airflow over the film element).
The concept of such an airflow sensor is based upon the variation in resistance of the two-terminal
sensing element with temperature. A current is passed through the sensing element supplying power to
it, thereby raising its temperature and changing its resistance. When this heated sensing element is
placed in a moving airstream (or other flowing gas), heat is removed from the sensing element as a
function of the mass flow rate of the air passing the element and the temperature difference betwee n
the moving air and the sensing element. For a constant supply current (i.e., heating rate), the temper-
ature at the element changes in proportion to the heat removed by the moving airstream, thereby pro-
ducing a change in its resistance. A convenient model for the sensing element resistance (R
SE
)at
temperature (T) is given by Eq. (5.3)
R
SE
TðÞ¼R
o
+ k
T
T T
ref
ðÞ (5.3)
where R
o
is the resistance at some reference temperature T
ref
(e.g., 0°C) and k
T
is the resistance/
temperature coefficient. The current i
2
flowing through R
SE
causes its temperature to rise above
ambient temper ature such that T ¼T
a
+ ΔT. The relationship between ΔT and
_
M
a
is explained later
in this section of the chapter for a conducting sensing element, k
T
>0, and for a semiconducting
sensing element, k
T
<0.
The mass flow rate of the moving airstream is measured via a measurement of the change in resis-
tance. There are many potential methods for measuring mass airflow via the influence of mass airflow
on the sensing element resistance. One such scheme involves connecting the element into a so-called
bridge circuit as depicted in Fig. 5.2.
In the bridge circuit, three resistors (R
1
, R
2
, and R
3
) are connected as depicted in Fig. 5.2 along with
a resistive sensing element denoted R
SE
(T). This sensing element consists of a thin film of conducting
(e.g., Ni) or semiconducting material that is deposited on an insulating substrate. The voltages V
1
and
V
2
(depicted in Fig. 5.2) are connected to the inputs of a relatively high-gain differential amplifier.
187AUTOMOTIVE CONTROL SENSORS AND ACTUATORS
剩余87页未读,继续阅读
资源评论
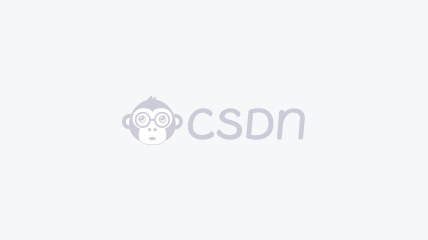

frank_technologies
- 粉丝: 13
- 资源: 91
上传资源 快速赚钱
我的内容管理 展开
我的资源 快来上传第一个资源
我的收益
登录查看自己的收益我的积分 登录查看自己的积分
我的C币 登录后查看C币余额
我的收藏
我的下载
下载帮助

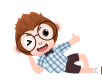
最新资源
- 基于微信小程序的网上商城+ssm-微信小程序毕业项目,适合计算机毕-设、实训项目、大作业学习.rar
- 教学辅助微信小程序设计+ssm-微信小程序毕业项目,适合计算机毕-设、实训项目、大作业学习.rar
- 基于微信小程序的童装商城的设计与实现+ssm-微信小程序毕业项目,适合计算机毕-设、实训项目、大作业学习.rar
- Python 实现GARCH分位数时间序列预测的设计项目实例(含完整的程序,GUI设计和代码详解)
- 家庭记账本的设计与实现+ssm-微信小程序毕业项目,适合计算机毕-设、实训项目、大作业学习.rar
- 基于微信小程序的校园二手交易平台系统设计与开发ssm-微信小程序毕业项目,适合计算机毕-设、实训项目、大作业学习.rar
- 基于微信小程序的小区疫情防控ssm-微信小程序毕业项目,适合计算机毕-设、实训项目、大作业学习.rar
- 流浪动物救助小程序--论文pf-微信小程序毕业项目,适合计算机毕-设、实训项目、大作业学习.zip
- 开放实验室预约管理系统pf-微信小程序毕业项目,适合计算机毕-设、实训项目、大作业学习.zip
- 美食推荐系统的微信小程序--论文pf-微信小程序毕业项目,适合计算机毕-设、实训项目、大作业学习.zip
- 基于小程序的社区超市管理系统springboot-微信小程序毕业项目,适合计算机毕-设、实训项目、大作业学习.rar
- 基于微信小程序的在线选课系统springboot-微信小程序毕业项目,适合计算机毕-设、实训项目、大作业学习.rar
- 生活小助手微信小程序_k1s0l-微信小程序毕业项目,适合计算机毕-设、实训项目、大作业学习.zip
- 农场管理系统(小程序)--论文pf-微信小程序毕业项目,适合计算机毕-设、实训项目、大作业学习.zip
- 基于微信小程序的学生公寓电费信息管理系统+ssm-微信小程序毕业项目,适合计算机毕-设、实训项目、大作业学习.rar
- 农业电商服务系统_30249--论文-微信小程序毕业项目,适合计算机毕-设、实训项目、大作业学习.zip
资源上传下载、课程学习等过程中有任何疑问或建议,欢迎提出宝贵意见哦~我们会及时处理!
点击此处反馈


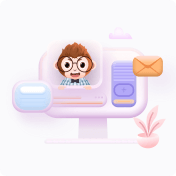
安全验证
文档复制为VIP权益,开通VIP直接复制
