
Dambulla
- 粉丝: 7
- 资源: 3万+
最新资源
- 【年度培训】培训效果评估报告(修改版)行政人事CLUB.doc
- 【年度培训】培训计划表行政人事CLUB.doc
- 【年度培训】公司员工培训总结报告行政人事CLUB.doc
- 【年度培训】年度培训计划及预算方案行政人事CLUB.doc
- 【年度培训】年度培训总结模板(内附表格,拿来即用)行政人事CLUB.doc
- 【年度培训】2023年度公司培训计划方案行政人事CLUB.doc
- 【年度培训】公司年度培训工作计划(完整版)行政人事CLUB.doc
- 【年度培训】【企业培训师】年度培训工作总结报告行政人事CLUB.doc
- 【年度培训】培训需求调查行政人事CLUB.pptx
- 【年度培训】DP152企业培训体系建设需求分析PPT行政人事CLUB.pptx
- 【年度培训】人力资源员工培训管理系统(完美版)行政人事CLUB.xlsx
- 【年度培训】2023年全年培训计划的副本行政人事CLUB.pptx
- 探索大规模语言模型在上下文学习中的决策边界机制
- 【年度培训】培训需求分析及评估行政人事CLUB.ppt
- 【年度培训】培训效果评估问卷行政人事CLUB.xlsx
- 【年度培训】培训员工跟踪表行政人事CLUB.xlsx
资源上传下载、课程学习等过程中有任何疑问或建议,欢迎提出宝贵意见哦~我们会及时处理!
点击此处反馈


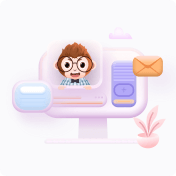