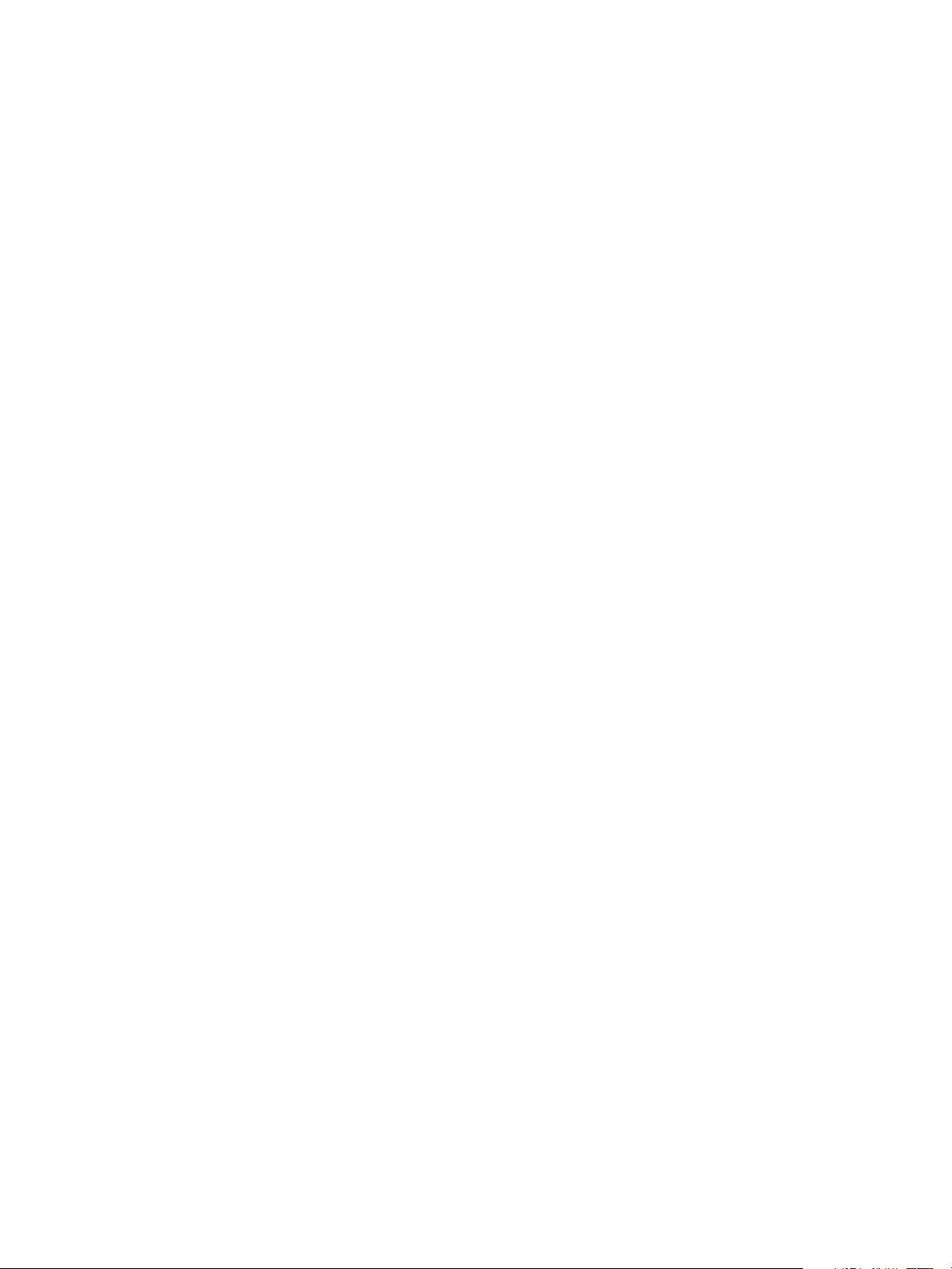
486 IEEE TRANSACTIONS ON INDUSTRIAL ELECTRONICS, VOL. 53, NO. 2, APRIL 2006
Design of a Maximum Power Tracking System for
Wind-Energy-Conversion Applications
Eftichios Koutroulis and Kostas Kalaitzakis
Abstract—A wind-generator (WG) maximum-power-point-
tracking (MPPT) system is presented, consisting of a high-
efficiency buck-type dc/dc converter and a microcontroller-based
control unit running the MPPT function. The advantages of the
proposed MPPT method are that no knowledge of the WG optimal
power characteristic or measurement of the wind speed is required
and the WG operates at a variable speed. Thus, the system features
higher reliability, lower complexity and cost, and less mechanical
stress of the WG.
Experimental results of the proposed system indicate near-
optimal WG output power, increased by 11%–50% compared
to a WG directly connected via a rectifier to the battery bank.
Thus, better exploitation of the available wind energy is achieved,
especially under low wind speeds.
Index Terms—Buck converter, maximum power point tracking
(MPPT), microcontroller, variable speed, wind generator (WG).
I. INTRODUCTION
W
IND GENERATORS (WGs) have been widely used
both in autonomous systems for power supplying re-
mote loads and in grid-connected applications. Although WGs
have a lower installation cost compared to photovoltaics, the
overall system cost can be further reduced using high-efficiency
power converters, controlled such that the optimal power is
acquired according to the current atmospheric conditions.
The WG power production can be mechanically controlled
by changing the blade pitch angle [1]. However, WGs of special
construction are required, which is not the usual case, especially
in small-size stand-alone WG systems.
A commonly used WG control system [2]–[4] is shown in
Fig. 1(a). This topology is based on the WG optimal power ver-
sus the rotating-speed characteristic, which is usually stored in a
microcontroller memory. The WG rotating speed is measured;
then, the optimal output power is calculated and compared to
the actual WG output power. The resulting error is used to
control a power interface. In a similar version found in [5],
the WG output power is measured and the target rotor speed
for optimal power generation is derived from the WG optimal
power versus rotor-speed characteristic. The target rotor speed
is compared to the actual speed, and the error is used to
control a dc/dc power converter. The control algorithm has been
implemented in LabVIEW running on a PC.
Manuscript received February 26, 2003; revised May 30, 2004. Abstract
published on the Internet January 25, 2006.
The authors are with the Department of Electronic and Computer Engineer-
ing, Technical University of Crete, Chania GR-73100, Greece (e-mail: koskal@
electronics.tuc.gr).
Digital Object Identifier 10.1109/TIE.2006.870658
In permanent-magnet (PM) WG systems, the output current
and voltage are proportional to the electromagnetic torque
and rotor speed, respectively. In [6] and [7], the rotor speed
is calculated according to the measured WG output voltage,
while the optimal output current is calculated using an ap-
proximation of the current versus the rotational-speed optimal
characteristic. The error resulting from the comparison of the
calculated and the actual current is used to control a dc/dc
converter.
The disadvantage of all above methods is that they are
based on the knowledge of the WG optimal power charac-
teristic, which is usually not available with a high degree
of accuracy and also changes with rotor aging. Another ap-
proach using a two-layer neural network [8] updates online
the preprogrammed WG power characteristic by perturbation
of the control signals around the values provided by the
power characteristic. However, under real operating conditions
where the wind speed changes rapidly, the continuous neural-
network training required results in accuracy and control-speed
reduction.
A control system based on wind-speed measurements [2]
is shown in Fig. 1(b). The wind speed is measured, and the
required rotor speed for maximum power generation is com-
puted. The rotor speed is also measured and compared to the
calculated optimal rotor speed, while the resulting error is used
to control a power interface.
Implementations of fuzzy-logic-based control systems trans-
ferring the maximum power from a wind-energy-conversion
system to the utility grid or to a stand-alone system have been
presented in [9] and [10], respectively. The controllers are based
on a polynomial approximation of the optimal power versus the
wind-speed characteristic of the WG.
Apart from the accuracy reduction due to the approximation
of the WG characteristics, an accurate anemometer is required
for the implementation of the aforementioned methods, which
increases the system cost. Furthermore, due to wind gusts of
low-energy profile, extra processing of wind-speed measure-
ment must be incorporated in the control system for a reliable
computation of the available wind energy, which increases the
control system complexity.
In this paper, an alternative approach for WG maximum-
power-point-tracking (MPPT) control is described. The block
diagram of the proposed system is illustrated in Fig. 2. The
MPPT process is based on monitoring the WG output power
using measurements of the WG output voltage and current
and directly adjusting the dc/dc converter duty cycle according
to the result of comparison between successive WG-output-
power values. Thus, neither knowledge of the WG power
0278-0046/$20.00 © 2006 IEEE