注射成型分析,课件
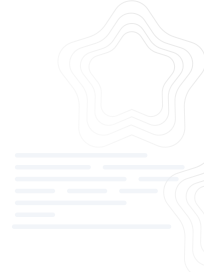

注射成型是一种广泛应用于塑料制品制造的技术,通过将熔融的塑料粒子注入模具中,冷却固化后形成所需的形状。这一过程涉及到多个关键知识点,包括材料选择、模具设计、工艺参数优化等。 1. 材料选择:注射成型所用的塑料原料通常为热塑性树脂或热固性树脂。热塑性树脂如聚乙烯(PE)、聚丙烯(PP)、聚苯乙烯(PS)等,它们在加热后可反复熔融成型;热固性树脂则在一次固化后不可逆,如酚醛树脂、环氧树脂等。选择材料时要考虑其机械性能、耐热性、耐化学性、成本等因素。 2. 模具设计:模具是注射成型的核心,它决定了产品的形状和尺寸精度。模具由动模和定模两部分组成,中间的分型面可以将产品从模具中取出。设计时需考虑流道系统(主流道、分流道、浇口),保证塑料熔体均匀流入每个型腔。此外,脱模机构、冷却系统和排气孔也是关键部分。 3. 工艺参数:注射成型过程中,注射速度、注射压力、熔融温度、保压时间和冷却时间等都是关键参数。注射速度过快可能导致飞边和内部应力集中,过慢则可能造成填充不足;注射压力需足够使熔体充满模具,但过大可能损坏模具;熔融温度影响塑料的流动性和粘度;保压时间确保塑料在模具内充分填充并减小收缩;冷却时间直接影响产品的尺寸和形状。 4. 流体力学与流动行为:理解塑料熔体在模具内的流动特性至关重要。流变学研究熔体在压力和剪切力下的流动行为,有助于优化注射速度和压力设定。剪切热是熔体流动过程中产生的热量,可能影响熔体温度和产品质量。 5. 冷却与结晶:塑料冷却过程中,分子会趋向于有序排列,形成结晶结构。冷却速率和模具温度对结晶度有直接影响,进而影响产品的物理性能,如硬度、强度和透明度。 6. 缺陷与解决:注射成型中可能出现的缺陷包括飞边、缩痕、气泡、翘曲等。通过调整工艺参数、改进模具设计或优化材料性能,可以减少或消除这些问题。 7. 机械与自动化:现代注射成型机具有高精度和自动化特性,包括闭环控制、伺服驱动和人机交互界面,以提高生产效率和制品质量。 注射成型分析涵盖了材料科学、模具设计、流变学、热力学等多个领域,通过对这些知识点的理解和应用,可以优化注射成型过程,提升塑料制品的质量和生产效率。这份课件提供了深入学习和实践注射成型技术的宝贵资源。
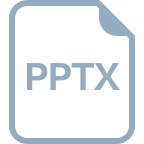
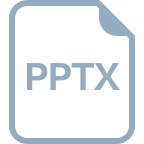
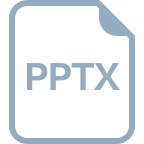
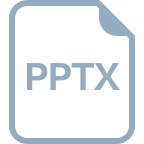
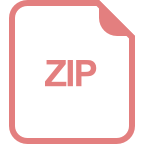
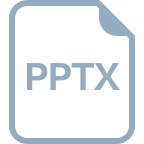
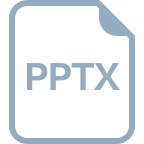
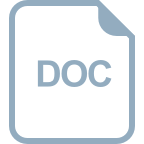
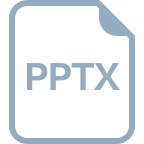
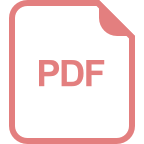
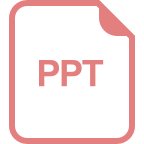
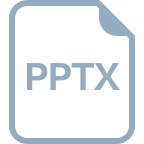
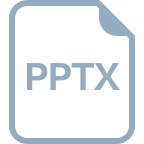
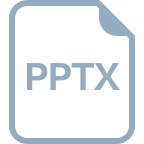
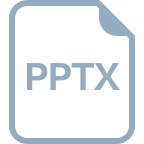
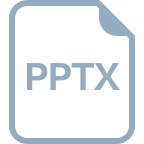


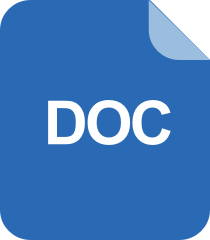
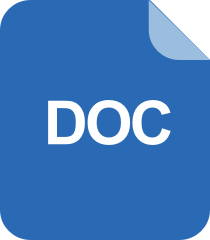
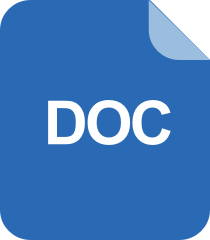
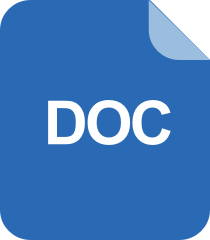
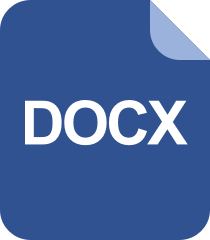
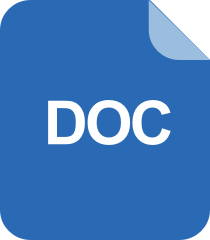
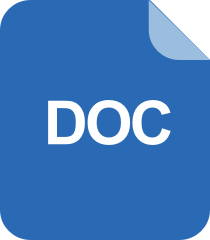
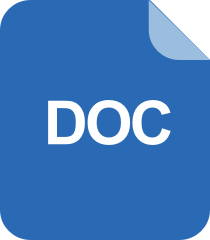
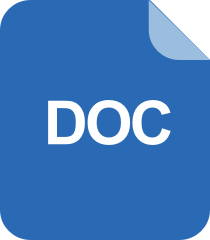
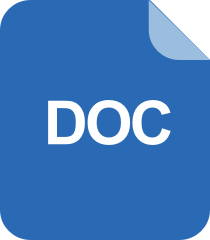
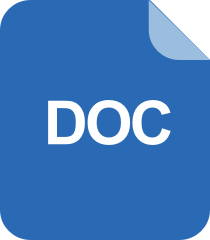
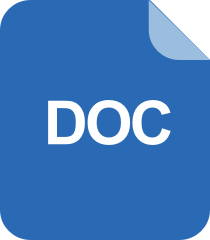
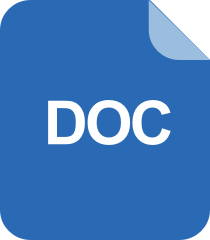
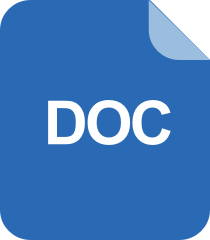
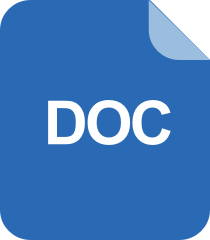
- 1
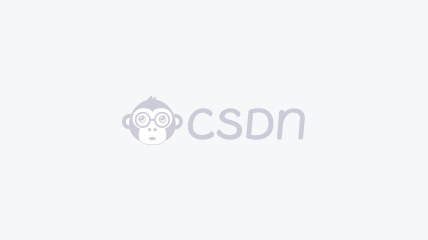

- 粉丝: 0
- 资源: 5
我的内容管理 展开
我的资源 快来上传第一个资源
我的收益
登录查看自己的收益我的积分 登录查看自己的积分
我的C币 登录后查看C币余额
我的收藏
我的下载
下载帮助

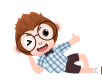
最新资源
- mmexport1732452246811.png
- Python毕业设计基于物品的协同过滤算法实现图书推荐系统项目源码(高分项目)
- 软考(中级-软件设计师)知识点汇总与解析
- Desktop (2).zip
- 考研冲刺模拟试题50道及解析
- 11月美宝莲专卖店店内海报 店内海报完稿310mmX360mm-op.ai
- Python 中实现十大排序算法
- 基于 Java 实现的24点卡牌游戏课程设计
- 基于ssm台球俱乐部管理系统 框架html + css + jquery + jsp + java + ssm + MySQL 用户类型 管理员 admin 123456 普通用户 002 0
- 纸中世界-跳跃游戏.sb3

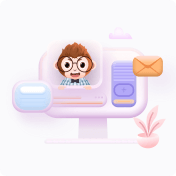
