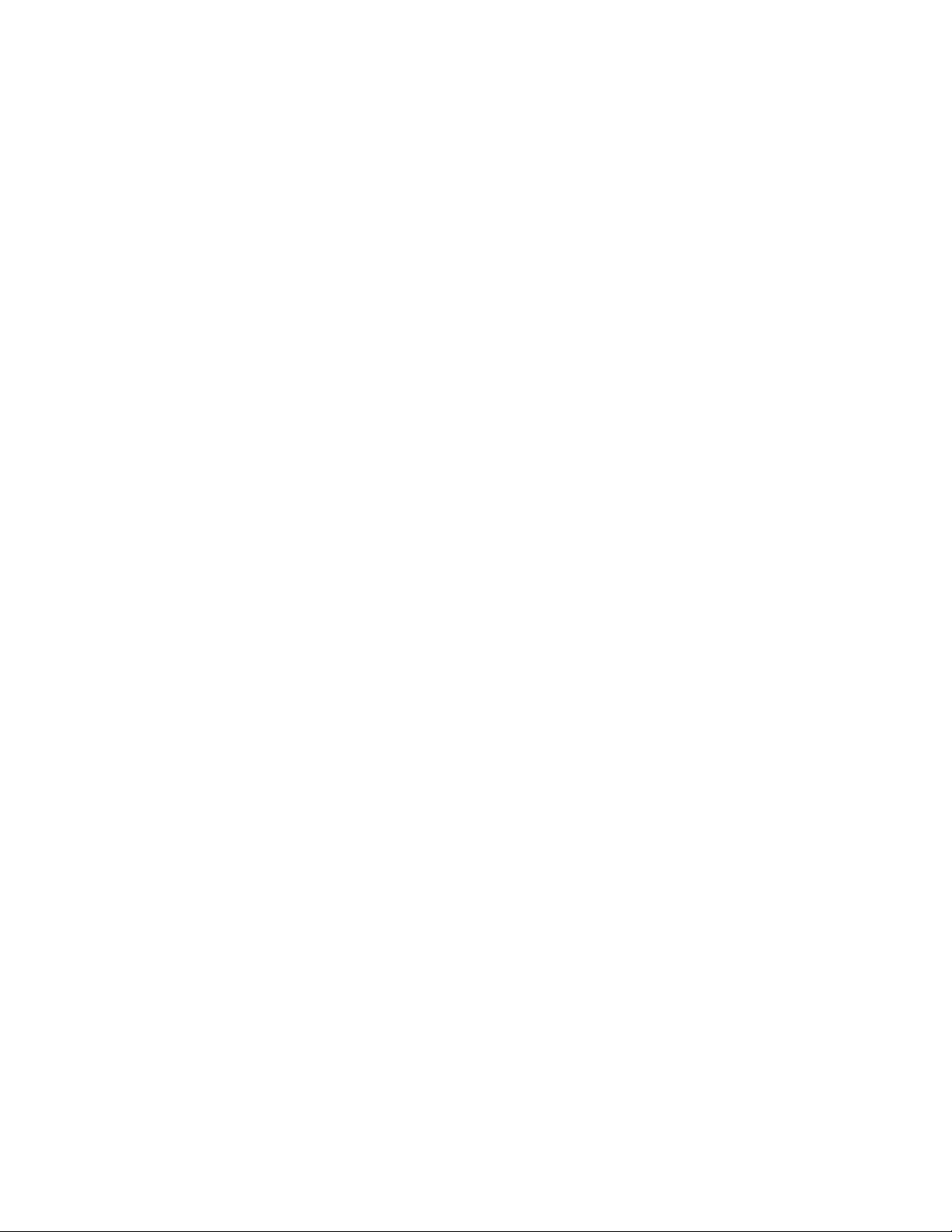
5
carrier of the SKU, in pallet picks, case picks and broken case (unit) picks. Many different order- picking
system types can be found in warehouses. Often multiple order-picking systems are employed within one
warehouse, for example in each of the three zones of Figure 1. Figure 2 distinguishes order-picking systems
according to whether humans or automated machines are used. The majority of warehouses employ humans
for order picking. Among these, the picker-to-parts systems, where the order picker walks or drives along the
aisles to pick items, are most common (De Koster 2004). We can distinguish two types of picker-to-parts
systems: low-level picking and high-level picking. In low-level order-picking systems, the order picker picks
requested items from storage racks or bins (bin-shelving storage), while travelling along the storage aisles.
Other order-picking systems employ high storage racks; order pickers travel to the pick locations on board of
a lifting order-pick truck or crane. The crane automatically stops in front of the appropriate pick location and
waits for the order picker to perform the pick. This type of system is called a high-level or a man-aboard
order-picking system.
Parts-to-picker systems include automated storage and retrieval systems (AS/RS), using mostly aisle-bound
cranes that retrieve one or more unit loads (pallets or bins; in the latter case the system is often called a mini-
load) and bring them to a pick position (i.e. a depot). At this position the order picker takes the required
number of pieces, after which the remaining load is stored again. This type of system is also called a unit-load
or end-of-aisle order-picking system. The automated crane (also: storage and retrieval (S/R) machine) can
work under different operating modes: single, dual and multiple command cycles. The single-command cycle
means that either a load is moved from the depot to a rack location or from a rack location to the depot. In the
dual-command mode, first a load is moved from the depot to the rack location and next another load is
retrieved from the rack. In multiple command cycles, the S/R machines have more than one shuttle and can
pick up and drop off several loads in one cycle. For example, in a four-command cycle (described in Sarker
and Babu 1995), the S/R machine leaves the depot with two storage loads, stores them and returns with two
retrieved loads. Other systems use modular vertical lift modules (VLM), or carousels that also offer unit loads
to the order picker, who is responsible for taking the right quantity.
Put systems, or order distribution systems (see Figure 2) consist of a retrieval and distribution process. First,
items have to be retrieved, which can be done in a parts-to-picker or picker-to-parts manner. Second, the
carrier (usually a bin) with these pre-picked units is offered to an order picker who distributes them over
customer orders (‘puts’ them in customer cartons). Put systems are particularly popular in case a large number
of customer order lines have to be picked in a short time window (for example at the Amazon Germany
warehouse, or flower auctions) and can result in about 500 picks on average per order picker hour (for small
items) in well-managed systems (De Koster 2004). Newly developed systems indicate that up to 1000 put
handlings per picker hour are feasible.
Figure 2 also shows several organisational variants of picker-to-parts systems. The basic variants include
picking by article (
batch picking) or pick by order (discrete picking). In the case of picking by article, multiple
customer orders (the batch) are picked simultaneously by an order picker. Many in-between variants exist,
such as picking multiple orders followed by immediate sorting (on the pick cart) by the order picker (sort-
while-pick), or the sorting takes place after the pick process has finished (pick-and-sort). Another basic variant
is zoning, which means that a logical storage area (this might be a pallet storage area, but also the entire
warehouse) is split in multiple parts, each with different order pickers. Depending on the picking strategy,
zoning may be further classified into two types: progressive zoning and synchronised zoning, depending on
whether orders picked in a zone are passed to other zones for completion or picked in parallel. The term wave
picking is used if orders for a common destination (for example, departure at a fixed time with a certain
carrier) are released simultaneously for picking in multiple warehouse areas. Usually (but not necessarily) it is
combined with batch picking. The batch size is determined based on the required time to pick the whole batch