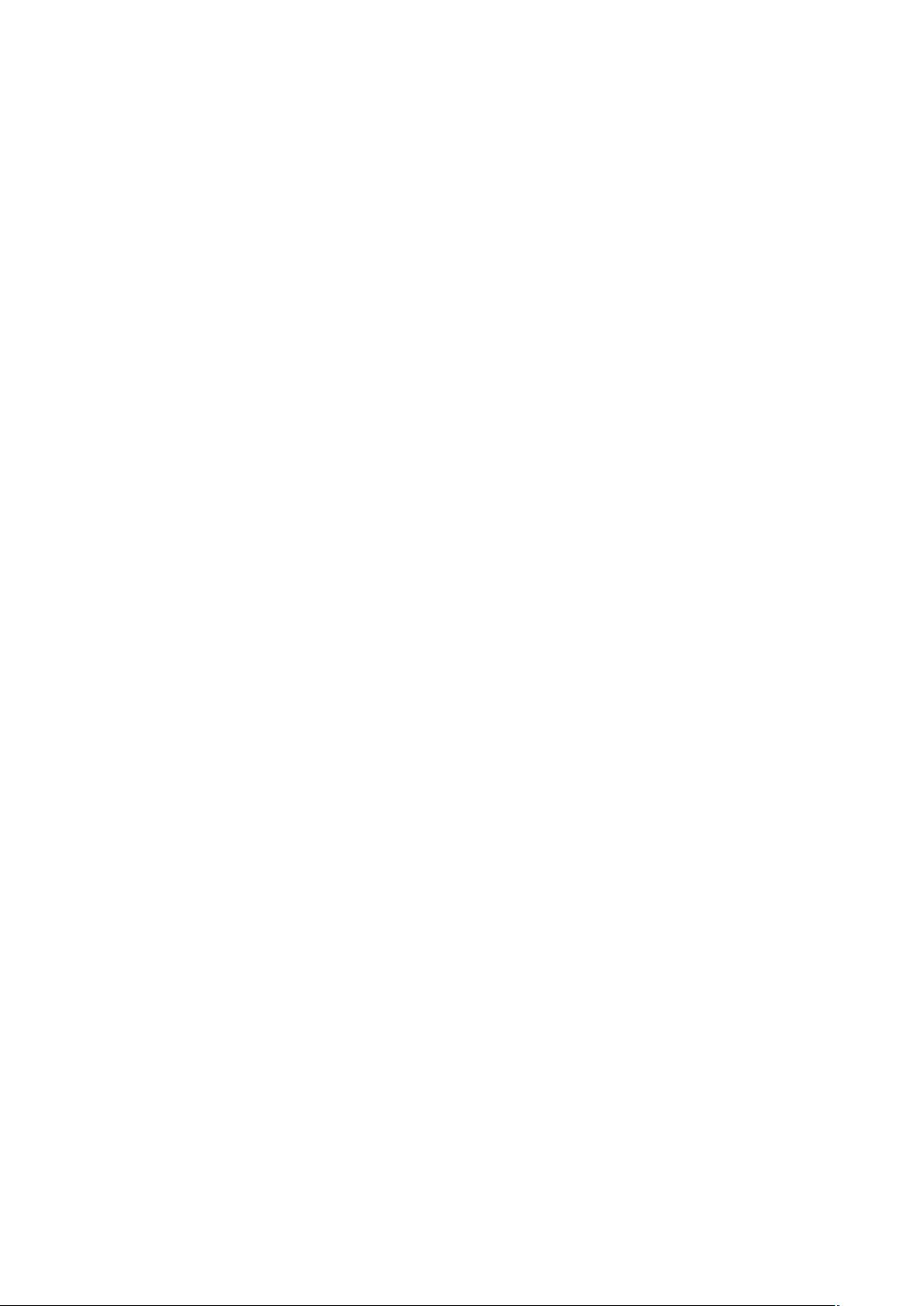
0.019208,误判率降低了 96.04%,从而使模型得到优化。
关键词:自动化车床管理 效益函数 正态分布 误判率
1.问题重述
一道工序用自动化车床连续加工某种零件,由于刀具损坏等原因该工序会出现故障,
其中刀具损坏故障占 95%, 其它故障仅占 5%。工序出现故障是完全随机的, 假定在生产
任一零件时出现故障的机会均相同。工作人员通过检查零件来确定工序是否出现故障。
现积累有 100 次刀具故障记录,故障出现时该刀具完成的零件数如附表。现计划在刀具
加工一定件数后定期更换新刀具。
已知生产工序的费用参数如下:
故障时产出的零件损失费用 f=200 元/件;
进行检查的费用 t=10 元/次;
发现故障进行调节使恢复正常的平均费用 d=3000 元/次(包括刀具费);
未发现故障时更换一把新刀具的费用 k=1000 元/次。
要求解的问题:
1)假定工序故障时产出的零件均为不合格品,正常时产出的零件均为合格品, 试对
该工序设计效益最好的检查间隔(生产多少零件检查一次)和刀具更换策略。
2)如果该工序正常时产出的零件不全是合格品,有 2%为不合格品;而工序故障时
产出的零件有 40%为合格品,60%为不合格品。工序正常而误认有故障停机产生
的损失费用为 1500 元/次。对该工序设计效益最好的检查间隔和刀具更换策略。
3)在 2)的情况, 可否改进检查方式获得更高的效益。
评论0
最新资源