没有合适的资源?快使用搜索试试~ 我知道了~
温馨提示
非常全的用户手册,全英文原版PFC3D用户手册。想学好还是要有毅力的。 部分目录: USER’S GUIDE Frontispiece Terms and Conditions Precis Table of Contents Section 1 : Introduction Section 2 : Getting Started Section 3 : Problem Solving with PFC3D Section 4 : FISH Beginner’s Guide Section 5 : Miscellaneous Section 6 : Bibliography COMMAND REFERENCE Frontispiece Table of Contents Section 1 : Command Reference
资源推荐
资源详情
资源评论
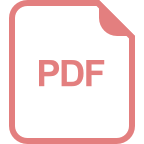
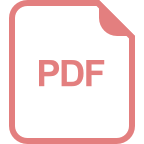
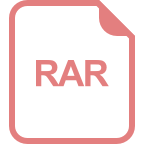
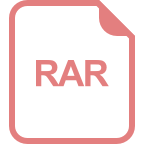
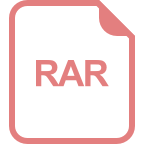
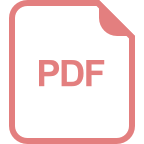
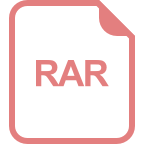
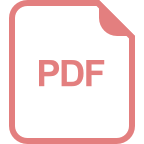
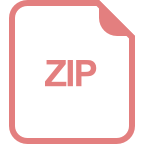
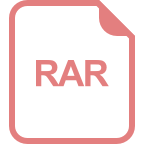
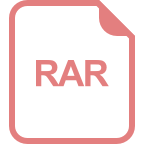
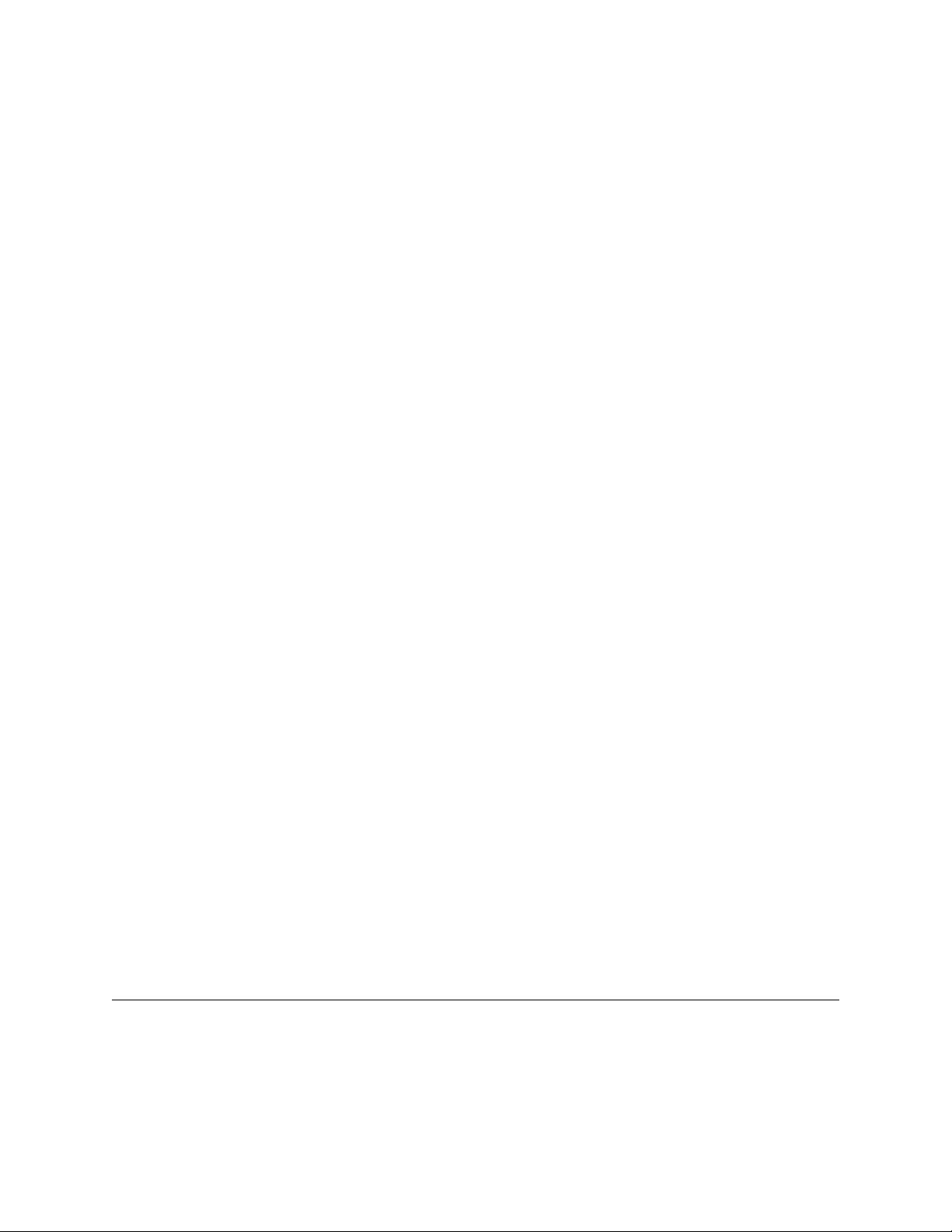
Online Contents - 1
PFC3D
Particle Flow Code
in 3Dimensions
Online Manual Table of Contents
USER’S GUIDE
Frontispiece
Terms and Conditions
Precis
Table of Contents
Section 1 : Introduction
Section 2 : Getting Started
Section 3 : Problem Solving with PFC
3D
Section 4 : FISH Beginner’s Guide
Section 5 : Miscellaneous
Section 6 : Bibliography
COMMAND REFERENCE
Frontispiece
Table of Contents
Section 1 : Command Reference
PFC
3D
Version 3.0
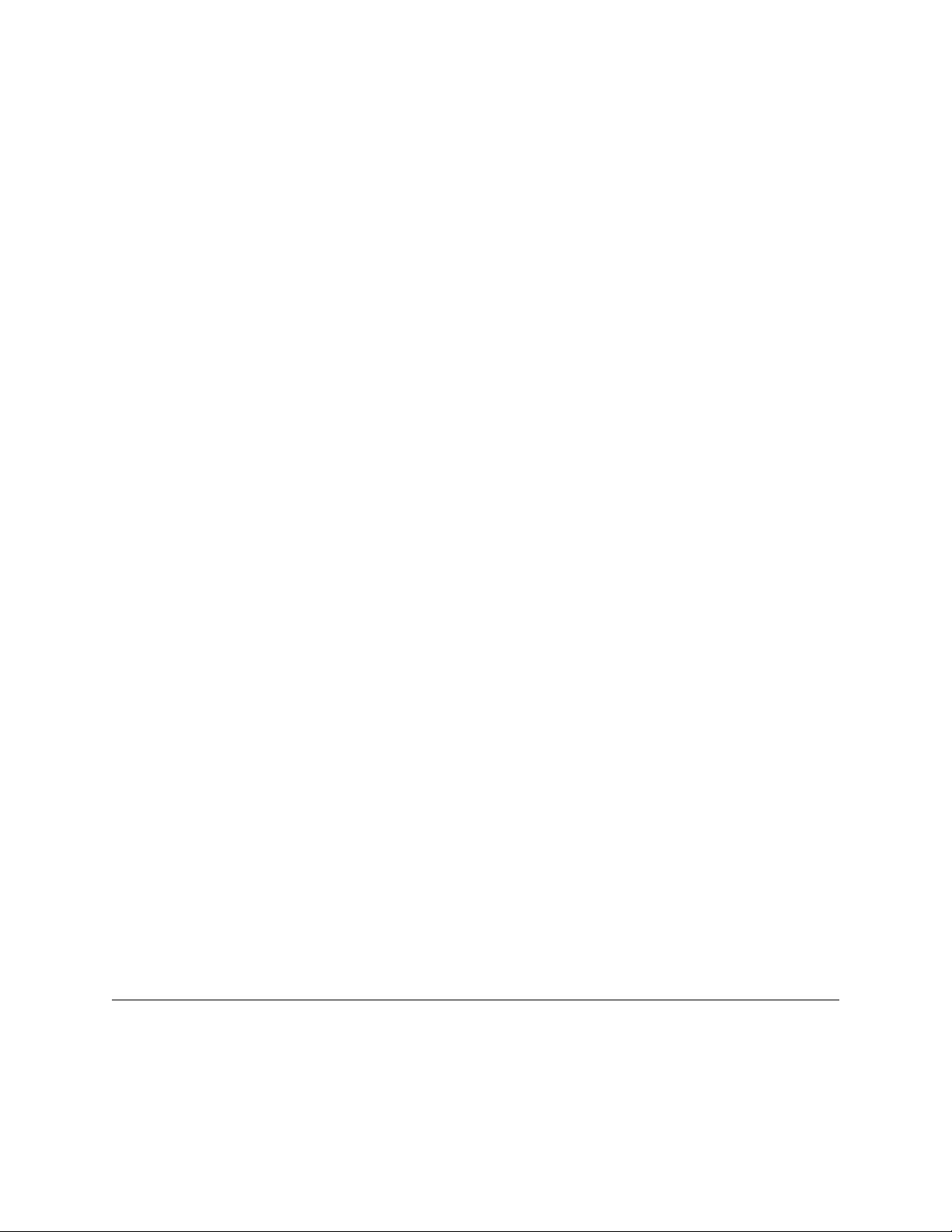
Online Contents - 2
FISH IN PFC
3D
Frontispiece
Precis
Table of Contents
Section 1 : FISH Beginner’s Guide
Section 2 : FISH Reference
Section 3 : Augmented FishTank
THEORY AND BACKGROUND
Frontispiece
Precis
Table of Contents
Section 1 : General Formulation
Section 2 : Contact Constitutive Models
Section 3 : Implementation Issues
Section 4 : Clump Logic
Section 5 : General Wall Logic
OPTIONAL FEATURES
Frontispiece
Precis
Table of Contents
Section 1 : Thermal Option
Section 2 : Writing New Contact Models
Section 3 : User-Written C++ Code
Section 4 : Parallel Processing
PFC
3D
Version 3.0
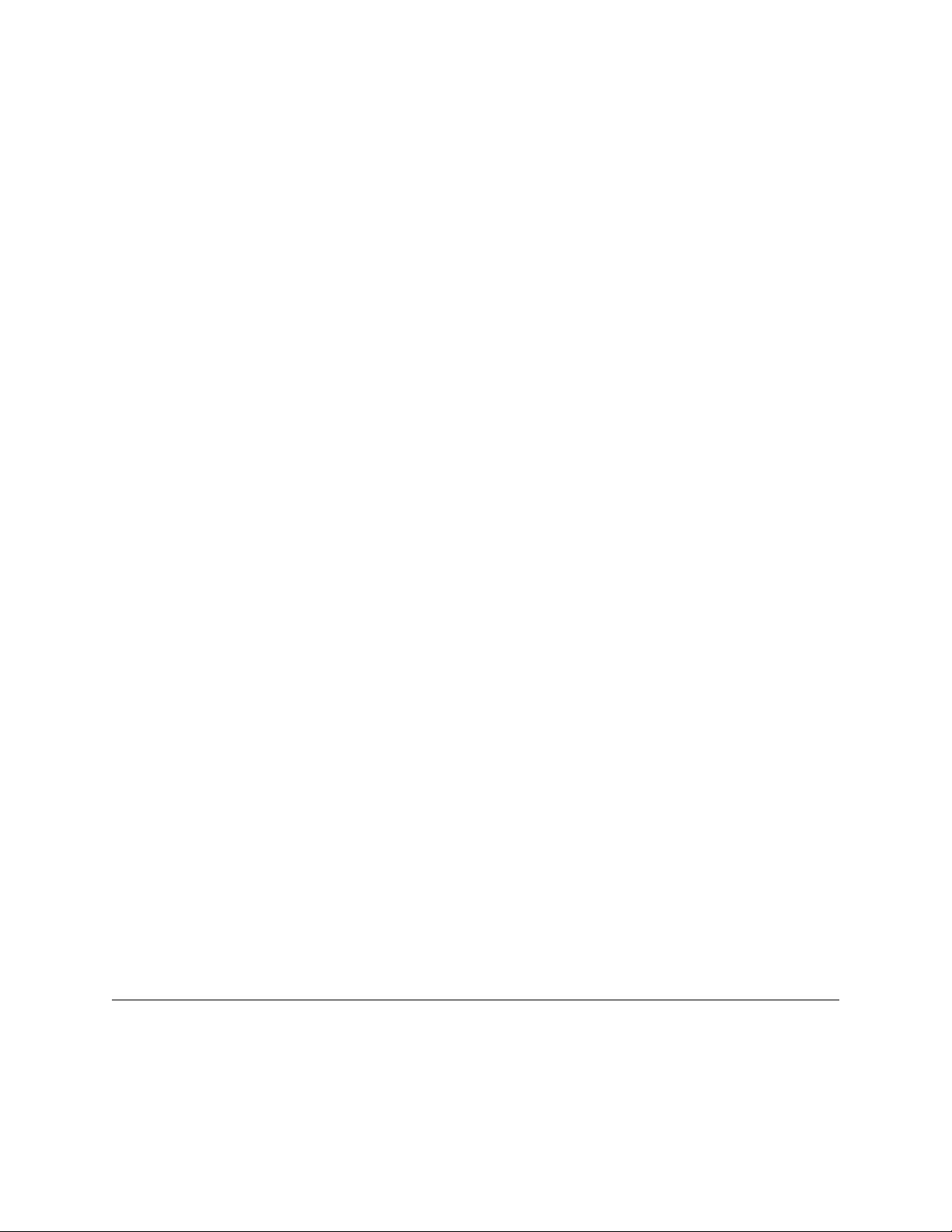
Online Contents - 3
VERIFICATION PROBLEMS AND EXAMPLE APPLICATIONS
Frontispiece
Precis
Table of Contents
Tip-Loaded Cantilever Beam
Energy Computations
Collisions with a Particle Assembly
Porosity Computations
Strength of a Face-Centered Cubic Array of Uniform Rigid Spheres
Triaxial and Brazilian Tests
Angle-of-Repose Test
Granular Flow from a Hopper
Mine Block-Caving Process
Rockfall
Dynamics of a Beam-Column Structure
Wave Propagation in Particle Assemblies
Triaxial Test on a Face-Centered Cubic Array of Rigid Particles
Experiments in Geometry with FISH
Incorporation of Fluid Coupling in PFC
3D
COMMAND AND FISH REFERENCE SUMMARY
Frontispiece
Precis
Table of Contents
Command Summary
FISH Statement Summary
PFC
3D
Version 3.0
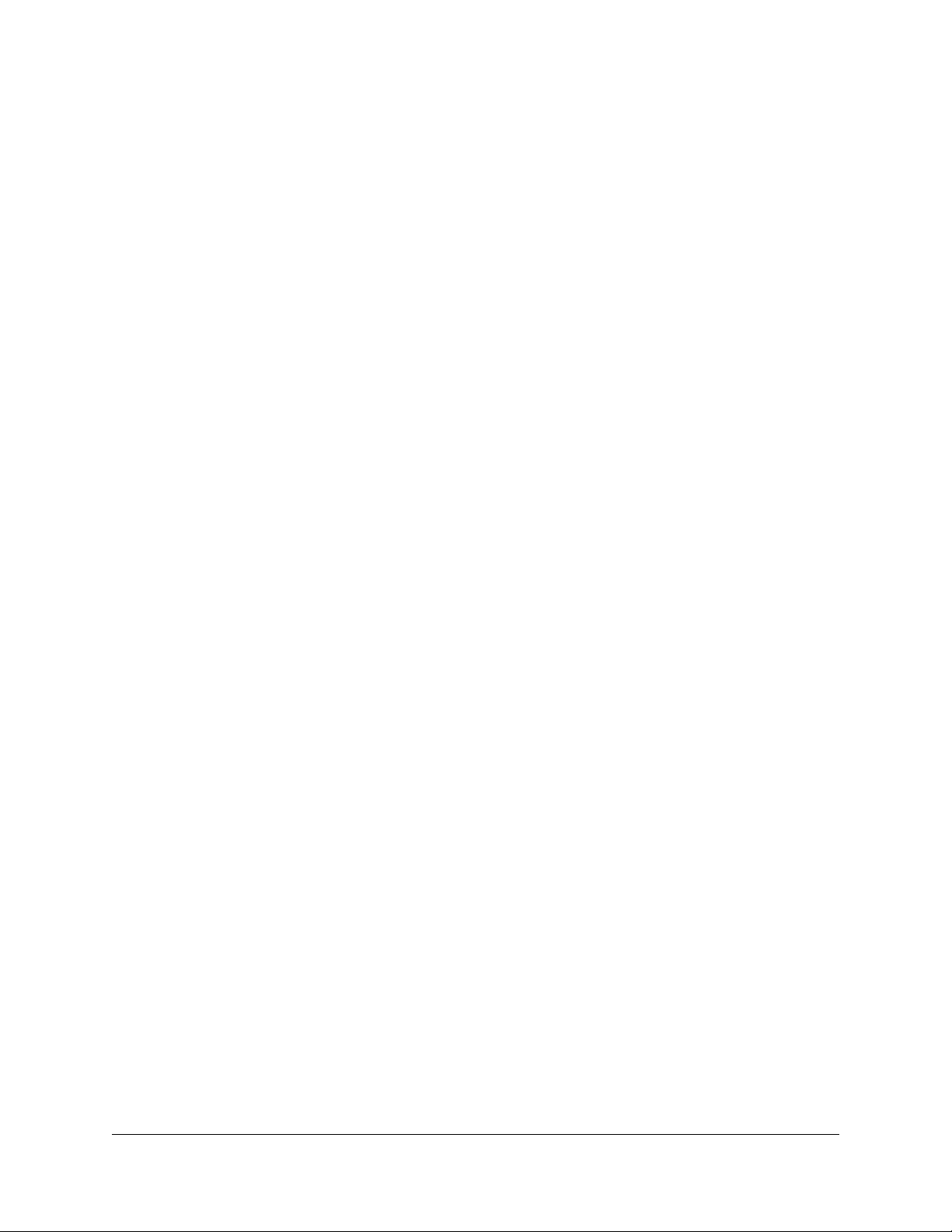
INTRODUCTION 1-1
1 INTRODUCTION
1.1 Background and Overview
PFC
3D
models the movement and interaction of spherical particles by the distinct element method
(DEM), as described by Cundall and Strack (1979). The original application of this method was as a
tool to perform research into the behavior of granular material; representative elements containing
several hundred particles were tested numerically. The particle model was used to understand
element behavior (in which conditions are “uniform”), and a continuum method was used to solve
real problems that involve complicated deformation patterns (with the element behavior derived
from the particle-model tests). Two factors have brought about a change in this approach. First, the
task of deriving general constitutive laws from test results on particle assemblies is very difficult.
Second, with the spectacular increase in powerofsmall computers, it is now possible to model entire
problems with particles; the constitutive behavior is built into the model automatically. PFC
3D
is
designed to be an efficient tool to model complicated problems in solid mechanics and granular
flow.
A physical problem that is concerned with the movement and interaction of spherical particles may
be modeled directly by PFC
3D
. It is also possible to create particles of arbitrary shape by attaching
two or more particles together, such that each group of particles acts as an autonomous object
(using the clump logic described in Section 4 in Theory and Background). PFC
3D
is also able
to model a brittle solid, by bonding every particle to its neighbor; the resulting assembly can be
regarded as a “solid” that has elastic properties and is capable of “fracturing” when bonds break in a
progressive manner. PFC
3D
contains extensive logic to facilitate the modeling of solids as closely-
packed assemblies of bonded particles (much of this logic has been implemented in the Augmented
FishTank — a set of functions written in FISH, the PFC
3D
embedded language); the solid may
be homogeneous, or it may be divided into a number of discrete regions or blocks. This type of
physical system may also be modeled by the distinct element programs UDEC (Itasca 2000) and
3DEC (Itasca 2003), which deal with angular blocks. However, PFC
3D
has three advantages. First,
it is potentially more efficient, since contact detection between circular objects is much simpler than
contact detection between angular objects; second, there is essentially no limit to the magnitude of
displacement that can be modeled; and third, it is possible for the blocks to break (since they are
composed of bonded particles), unlike blocks modeled with UDEC or 3DEC which cannot break.
The drawback to modeling a blocky system with PFC
3D
is that block boundaries are not planar; in
exchange for the advantages offered by PFC
3D
, the user must accept “bumpy” boundaries.
The specification of the geometry, properties and solution conditions is not so straightforward in
PFC
3D
as in programs such as FLAC (Itasca 2002) and UDEC. For example, with a continuum
program, a grid is created, initial stresses installed, and boundaries set as fixed or free. In a
particle code such as PFC
3D
, a compacted state cannot be pre-specified in general, since there
is no unique way to pack a number of particles within a given volume. A process analogous to
physical compaction must be followed until the required porosity is obtained. The initial stress
state cannot be specified independently of the initial packing since contact forces arise from the
relative positions of particles. Finally, the setting of boundary conditions is more complicated
than for a continuum program because the boundary does not consist of planar surfaces. These
issues are all addressed in this manual, and practical procedures are suggested for making realistic
PFC
3D
Version 3.0
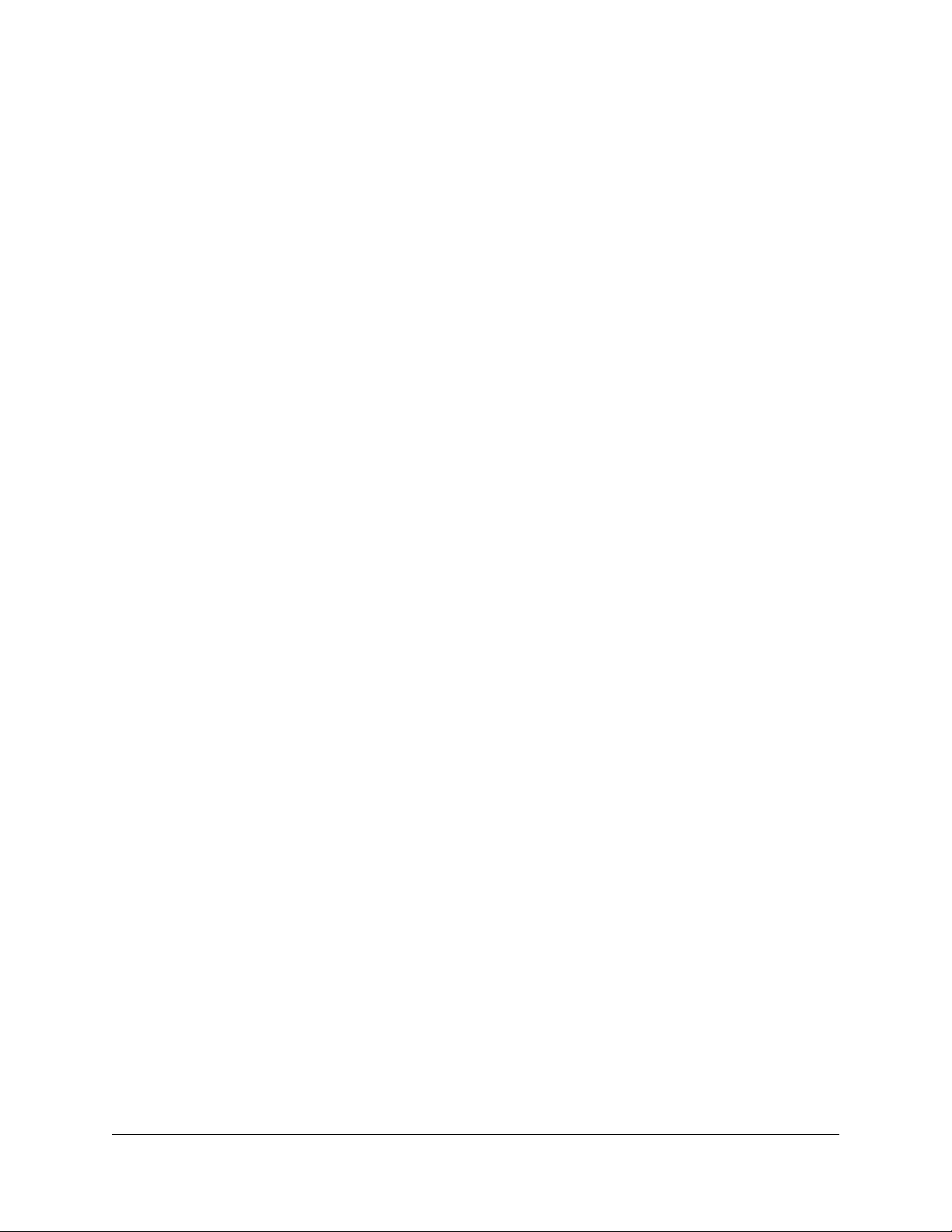
1-2 User’s Guide
models. A further difficulty arises when it is required to match the behavior of a simulated solid
(comprised of bonded particles) with a real solid tested in the laboratory. To some extent, this is a
trial-and-error process, because there is no complete theory that can predict macroscopic behavior
from microscopic properties and geometry. However, guidelines are given that should help in the
matching process(e.g., which factorsinfluencesomeaspectof behavior and which do not). It should
be realized that such modeling is difficult because it is exercising the limits of current knowledge.
However, by performing tests with PFC
3D
, we stand to gain some fundamental understanding in
solid mechanics (particularly in fracture mechanics and damage mechanics).
The calculation method (DEM) is a timestepping, explicit scheme, which is described in more detail
inSection 1.3 in Theory andBackground. Thereare severaladvantagesto sucha scheme. Systems
that exhibit physical instability may be modeled without numerical difficulty. Large populations of
particles require only modest sizes of computer memory, since matrices are never stored. PFC
3D
may be used to model static or dynamic problems, but the full dynamic equations of motion are
solved even when static solutions are required. This is done in order to follow such phenomena as
failure and “flow” of material in a realistic manner; it is not necessary to invoke some nonphysical
algorithm, as done in some implicit methods. Modeling with PFC
3D
involves the execution of
many thousands of timesteps. At each step, Newton’s second law (force = mass × acceleration)
is integrated twice for each particle to provide updated velocities and new positions, given a set
of contact forces acting on the particle. Based on these new particle positions, contact forces are
derived from the relative displacements of pairs of particles; a linear or nonlinear force/displacement
law at contacts may be used.
The current version of PFC
3D
operates on any IBM-compatible computers running Windows95 or
later operating systems. With 160 MB of RAM, approximately 100,000 particles may be modeled,
assuming a reasonable packing density. A parallel-processing option is available, whereby a simu-
lation may be split between several processors, connected by a network. For details, see Section 4
in Optional Features.
PFC
3D
operates, by default, in a command-driven mode; a graphical, menu-driven mode also exists
forfile-handling, plottingand print redirection. Ineither mode, there are graphics facilitiesin PFC
3D
that allowhigh-resolution, color-renderedplots to be generated rapidly. The graphics displays allow
the user to view the model during creation or at any stage during a run. The model can be translated,
rotated and magnified on the screen for optimum viewing. Perspective plots may be made of the
particles, walls, contacts, forces, displacements, velocities and other quantities. All plotted output
can be directed to a black-and-white or color output device, to the Windows clipboard, or to a file
(in PostScript and various bitmap formats).
PFC
3D
Version 3.0
剩余1312页未读,继续阅读
资源评论
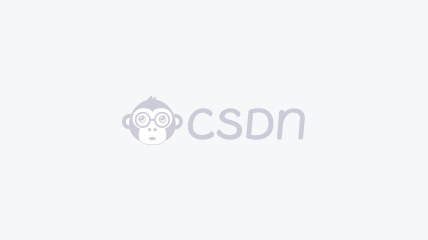

xuefeng1990
- 粉丝: 4
- 资源: 5
上传资源 快速赚钱
我的内容管理 展开
我的资源 快来上传第一个资源
我的收益
登录查看自己的收益我的积分 登录查看自己的积分
我的C币 登录后查看C币余额
我的收藏
我的下载
下载帮助

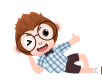
最新资源
- mCloud_11.3.5_24113518_1282.apk
- 三相PWM整流器闭环仿真,电压电流双闭环控制,输出直流电压做外环 模型中包含主电路,坐标变,电压电流双环PI控制器,SVPWM控制,PWM发生器 matlab simulink模型 功率因数1,低TH
- 算法题解与优化基础教程
- 数据结构与算法基础教程
- GA-PID,采用遗传算法优化PID参数,或者叫PID参数整定 matlab代码 PID和被控对象部分采用simulink搭建的
- 计算机考试习题基础教程:从入门到精通
- 数据集构建与分析基础教程
- 基于无权重系数占空比模型预测转矩永磁同步电机控制,主体采用matlab function模块编程,与c语言接近,便于实物移植 【提供参考lunwen】 相比于传统模型预测转矩控制性能提高很多 可赠
- 欧拉法仿真铺粉元素偏移, 里面包含高斯移动热源,温度梯度设置,以及元素偏析模拟和四种元素的铺粉定向能量沉积模型以及全视频讲解,包含完整的仿真模型以及自定义编程代码和讲解视频(反冲与元素基本模型三维)
- 10位100M,SAR ADC完整电路,包括仿真测试代码,建模代码,电路文件,奈奎斯特频有效位数9.8
- 电阻炉温度仿真, 模糊PID控制电阻炉温度仿真, 其中包括量化因子,比例因子的设定, 以及全篇介绍文档 拿来就可以用
- 分布式电源风机与光伏的并网Matlab Simulink仿真,包含两种风机与光伏类型,附带参考文献 直驱:机侧最佳叶尖速比控制,网侧双闭环控制,额定功率300kW,并网等级690V 双馈:机侧转速
- e2studio开发RA0E1(10)-TAU配置One-Shot模式生成固定数量PWM
- MATLAB 代码:考虑阶梯式碳机制与电制氢的综合能源系统热电优化 关键词:碳 电制氢 阶梯式碳 综合能源系统 热电优化 参考文档:《考虑阶梯式碳机制与电制氢的综合能源系统热电优化》基本复现 仿
- 简单质量添加单层以及多层 里面包含简单的三维质量源项以及移动高斯热源,并且可以进行多层熔覆模拟,包含完整的仿真模型以及自定义编程代码和讲解视频
- 大厂量产的PCS储能源代码
资源上传下载、课程学习等过程中有任何疑问或建议,欢迎提出宝贵意见哦~我们会及时处理!
点击此处反馈


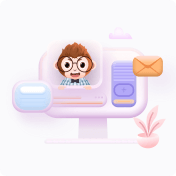
安全验证
文档复制为VIP权益,开通VIP直接复制
