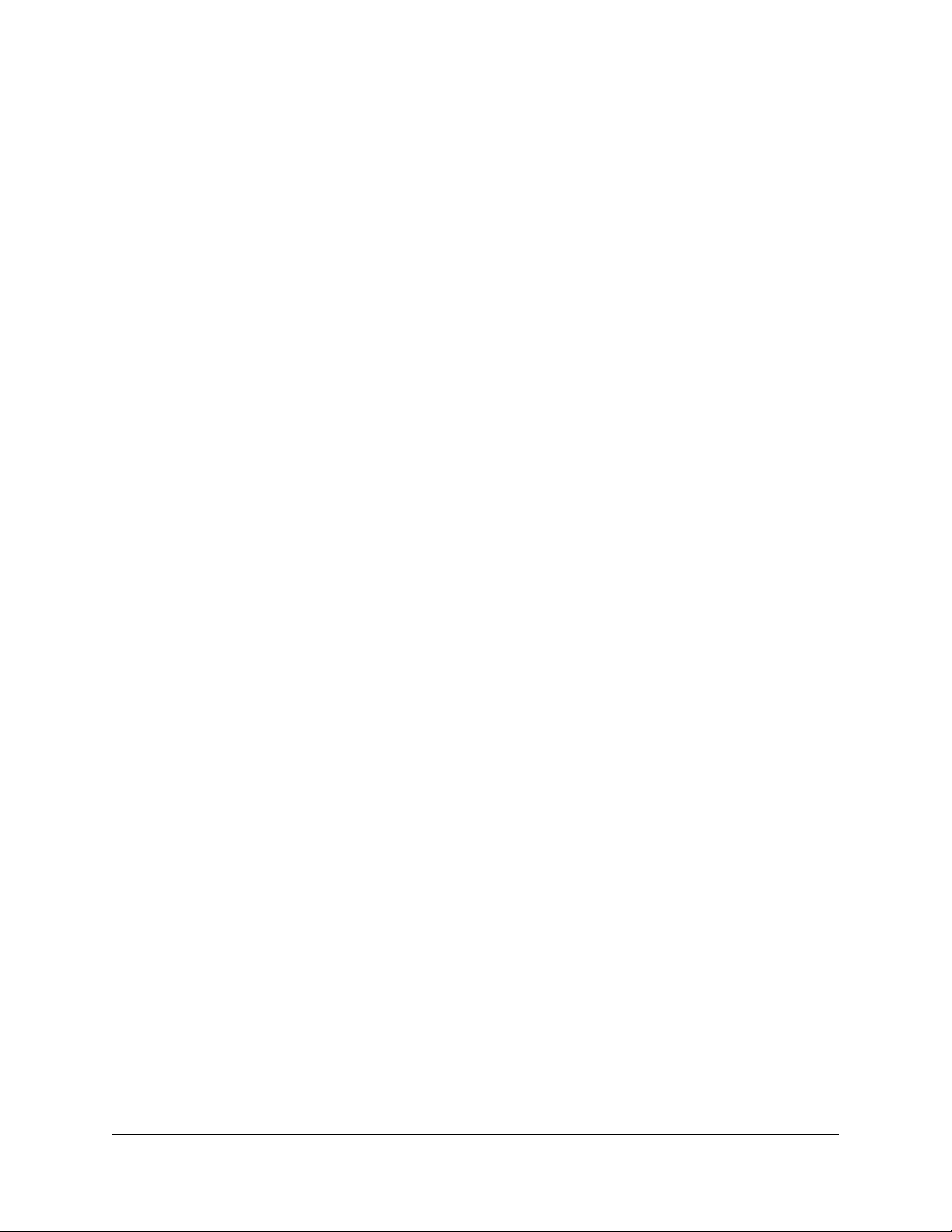
THERMAL OPTION 1-1
1 THERMAL OPTION
1.1 Introduction
The thermal option of PFC
3D
allows simulation of transient heat conduction and storage in materials
consisting of PFC
3D
particles, and development of thermally-induced displacements and forces.
The thermal material is represented as a network of heat reservoirs (associated with each particle)
and thermal pipes (associated with the contacts). Heat flow occurs via conduction in the active
pipes that connect the reservoirs. Radiative and convective heat transfer are not included in the
present formulation. Thermally-induced strains are produced in the PFC
3D
material by modifying
the particle radii and the force carried in each parallel bond to account for heating of both particles
and bonding material.
A thermal pipe is associated with each contact, but only some of these pipes are active. By default, a
pipeisactiveifthe twoparticles atthe contactare overlappingorif abond ispresent. (The criteriafor
apipe tobe activecan be altered bythe THERMAL pipe command.) Once the thermal microproperties
are specified, subsequent loading or damage (in the form of bond breakages) will modify the number
of active pipes, and thereby change the ability of the material to conduct heat. For example, as
a bonded material is compressed and new pipes form, the macroscopic thermal conductivity will
be increased, but as bonds break and associated pipes become inactive, the macroscopic thermal
conductivity will be reduced.
PFC
3D
Version 3.0
评论8
最新资源