
xiaowu198809
- 粉丝: 13
- 资源: 17万+
最新资源
- BP神经网络回归拟合求各指标权重 建立输入输出的非线性拟合关系,利用神经网络连接权重计算输入指标对输出的权重值 可根据案例替为自己数据进行拟合求权重 Matlab代码备注清晰,适合新手使用
- KNN分类预测 可以选取80%的数据训练,20%测试(可自定义百分比) Matlab代码备注清晰,易于使用
- 电力负荷数据异常检测 窃电检测 MATLAB代码 适用人群:研究方向相近的本硕博学生,电力行业创新小组成员等
- Dwa方法实现局部路径规划,代码有注解,包含静态障碍物和动态障碍物
- FPGA纯verilog代码实现H.264 AVC视频解码,提供工程源码
- 基于FPGA的GMSK,2-FSK等调制算法仿真
- 自动驾驶控制器,车道偏离预警系统,基于Prescan设计场景和交通流,在Simulink中建立了相应的控制模型 进行LDW功能验证 整个模型自己建立,再次强调不是Prescan自带的那种很乱很模糊
- 伪谱法(伪谱最优控制方法) GPOPS II 以混合动力汽车能量管理控制为例,演示如何使用GPOPS II软件解决最优控制问题
- 基于输入整形的双惯量系统末端抖动低频机械谐振抑制仿真 1.模型简介 模型为基于输入整形的双惯量伺服系统低频机械谐振抑制(末端抖动抑制)仿真,采用Matlab R2018a Simulink搭建
- abaqus-012使用Python脚本提取积分点径向应力与位移
- 双机并联自适应阻抗下垂控制(droop)MATLAB仿真模型 下垂控制 电压电流双环控制 锁相环 有参考文献 模块完整,运行曲线完美,适合作为基础模型 MATLAB2018b及以上版本
- Comsol多场耦合仿真模型 温度场-水分场-应力场耦合,可实现冻融循环,高温,降水,渗流等场景的模拟 模型可自定义,适用于桩基路基,矿坝边坡等,附送教学视频
- Astar路径规划算法,画出障碍点 调用A*算法画出路径 Matlab代码
- simplorer与Maxwell电机联合仿真,包含搭建好的Simplorer电机场路耦合主电路与控制算法(矢量控制SVPWM),包含电路与算法搭建的详细教程视频 仿真文件可复制,可将教程中的电机模
- VSG预同步控制matlab仿真模型 MATLAB2019b 主要模块: 并网逆变器+VSG控制+预同步控制+电流电流双环控制 锁相环、三相准PR控制、PWM 0.65秒开始并网运行
- 基于分时电价条件下家庭能量管理策略研究MATLAB程序 参考文献: 《基于分时电价和蓄电池实时控制策略的家庭能量系统优化》参考部分模型 《计及舒适度的家庭能量管理系统优化控制策略》参考部分模型 主要内
资源上传下载、课程学习等过程中有任何疑问或建议,欢迎提出宝贵意见哦~我们会及时处理!
点击此处反馈


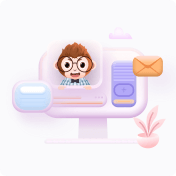