
拉拉庸
- 粉丝: 21
- 资源: 66万+
最新资源
- Javase语言学习.zip
- CRC16-CCITT-FALSE
- 圣诞树html展示代码资料.zip
- ATA Command Set -5 (ACS-5).pdf
- wpf 控件库 参考 Demo
- MoonBit 编译器 MoonBit - 文档 - 概览 - 标准库
- CRC8 标准校验CAN报文
- promtail linux 安装包
- 基于微信小程序的中国各地美食推荐平台的设计与实现springboot.zip
- 微信小程序基于BS模式的学生实习与就业管理系统设计与实现springboot.zip
- 微信小程序自助点餐系统springboot.zip
- 【大模型必备】office 转 markdown 的服务实现,基于微软markitdown
- 答题小程序ssm.zip
- 基于微信小程序的水果销售系统的设计与实现springboot.zip
- 基于微信小程序的学生签到系统设计与实现ssm.zip
- “校园资料分享微信小程序”的设计与实现springboot.zip
资源上传下载、课程学习等过程中有任何疑问或建议,欢迎提出宝贵意见哦~我们会及时处理!
点击此处反馈


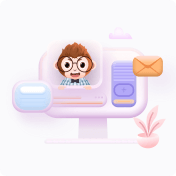