
拉拉庸
- 粉丝: 21
- 资源: 66万+
最新资源
- 基于小程序的小区服务系统源码(小程序毕业设计完整源码).zip
- TCU变速箱控制器仿真模型-含(设计文档) 乘用车AMTTCU变速箱控制器仿真模型算法模块,含TCU应用层软件,驱动制动数学模型,电机传动数学模型,车辆数学模型等,在产品已量产 含有的功能模块包括但
- 基于小程序的学生宿舍管理系统源码(小程序毕业设计完整源码).zip
- 双三相永磁同步电机模型预测控制仿真,采用matlab离散化仿真,通过使能模块,真实模拟DSP中断触发方式 图一为参考文献,真实复现TOP文献 图二为突加负载和转速突变波形 图三为电流波形 图四为预
- 毕设-java-swing-仓库商品管理系统(文档+视频+源码)
- 基于小程序的宿舍管理小程序源码(小程序毕业设计完整源码).zip
- 工具变量-上市公司股吧舆论数据(2008-2023年).txt
- 超级多种多目标优化算法(动物园算法) 能够打印运行时间对比图 有注释,适合入门
- 基于小程序的微信小程序的点餐系统源码(小程序毕业设计完整源码).zip
- 基于小程序的短视频系统源码(小程序毕业设计完整源码).zip
- 【电动汽车优化调度】考虑温度对电动汽车的影响 温度可影响电动汽车的电池容量问题
- 基于小程序的付费自习室系统源码(小程序毕业设计完整源码).zip
- 采用pfc2d6.0构建松散可破碎土石混合体的地基强夯模型 块石由可破碎颗粒cluster建立,土体由ball建立,赋予不同的接触属性 可监测动应力、位移、孔隙比等参数变化 可根据需求修改级配、
- 基于小程序的高校课堂教学管理系统源码(小程序毕业设计完整源码+LW).zip
- 毕设-java-swing-电影票购票管理系统(视频+源码)
- 基于小程序的食堂窗口自助点餐系统源码(小程序毕业设计完整源码).zip
资源上传下载、课程学习等过程中有任何疑问或建议,欢迎提出宝贵意见哦~我们会及时处理!
点击此处反馈


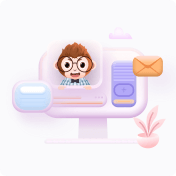