
拉拉庸
- 粉丝: 21
- 资源: 66万+
最新资源
- 一个简单的新年活动页面的HTML模板示例
- 工程翻斗车sw16全套技术资料100%好用.zip
- 锂电池极片贴正反面绝缘胶纸机sw17全套技术资料100%好用.zip
- 环链垂直连续升降提升机全套技术资料100%好用.zip
- 三级轴齿XYZ轴供料机械手sw17可编辑全套技术资料100%好用.zip
- 专业综合课程设计报告封面.docx
- OpenAI-Swarm
- C# 进度条源码,拷贝文件实例
- 基于SpringBoot的“在线BLOG网”的设计与实现(源码+数据库+文档+PPT).zip
- 用QT写的一个UDP数据发送测试小程序
- 最新知宇企业级发卡源码/新增几套模板/多商户入驻/API代销/自动发卡网站运营源码
- C# TCP客户端程序源码
- 互站价值800元的CSM会议室预约系统源码+企业免授权版+详细搭建教程
- 基于交变电流场测量技术的水下结构缺陷可视化与智能识别方法
- C# 生成excel图表I源码
- 光敏传感器实验熟练掌握光敏传感器的使用方法
资源上传下载、课程学习等过程中有任何疑问或建议,欢迎提出宝贵意见哦~我们会及时处理!
点击此处反馈


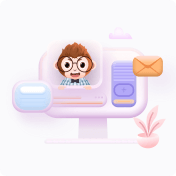