
我虽横行却不霸道
- 粉丝: 95
- 资源: 1万+
最新资源
- 【python】Google出品的机器学习入门视频的中文字幕翻译与示例代码.zip
- 【python】Python3工具集合库——中国农历-中文数字-设计模式-树形结构.zip
- 西安电子科技大学在线评测系统(xdoj)题库结构及运维流程解析
- JavaEE实践项目详解-从校内课程到校企合作的应用开发
- 2025新春好友送祝福微信小程序源码.zip
- 【python】钉钉群自定义机器人webhook协议的Python封装.zip
- 【python】Python爬虫爬取公众号所有文章信息,包括标题、url、md链接.zip
- 【python】python爬虫破解滑动验证码使用.zip
- 【python】基于python的qq群机器人.zip
- 【python】机器学习NB算法实现基于文本的WebShell检测工具.zip
- 【python】南京大学实验室安全教育与考试系统考试脚本用于生成答案.zip
- 【python】使用python爬虫爬取域名的whois信息并存入mysql数据库.zip
- 【python】人工智能与机器学习.zip
- 【python设计模式】大话设计模式python实现.zip
- 【python爬虫】Python写的微博定向抓取图片的爬虫.zip
- 【react】使用React编写的在线考试系统.zip
资源上传下载、课程学习等过程中有任何疑问或建议,欢迎提出宝贵意见哦~我们会及时处理!
点击此处反馈


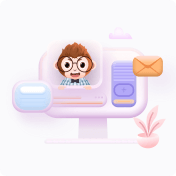