本文中所设计的系统利用工业控制计算机作调度、管理、完成了工业控制计算机与plc之间以及plc与plc之间的监视和控制参数的传递,提高了立体仓库的自动化管理水平。经过在现场的实际应用证明,这种管理和控制系统结构具有很高的可靠性和稳定性。 《基于PLC的立体仓库控制系统设计》 立体仓库控制系统是一种高度集成的信息、储存和管理的自动化设备,尤其在现代大规模生产环境中,它扮演着至关重要的角色。本文介绍的设计方案运用了工业控制计算机作为调度和管理核心,实现了与PLC之间的通信,确保了参数的实时监控和传递,从而提升了立体仓库的自动化管理水平。该系统在实际应用中表现出极高的稳定性和可靠性。 立体仓库的工艺流程是关键。以某企业为例,配料车间需要处理144种不同类型的粉体原料,每次取n种,每种重量不一。操作人员通过人机交互界面(触摸屏)设定目标料仓号和料位号,系统依据差值计算出最短路径,启动变频电机,并根据差值调整料仓的运行速度,防止摆动。目标料仓到达时,精确停机并亮起指示灯,便于操作。此外,系统还设有计量装置,当粉料重量达到预设值时,会发出提示,进入下一料仓和料位的操作。第二阶段的目标是实现自动称量,进一步提高效率。 在系统架构方面,立体仓库控制系统主要由PWS6A00型触摸屏、CJ1W-CPU22系列PLC、VLT5000型变频器、变频电动机、减速接近开关、到位接近开关以及其他电气元件构成。触摸屏通过专用电缆与PLC连接,进行操作和参数修改;PLC通过CS1W-CN114和CS1W-CN226连接编程器或PC进行离线编程和模拟。 系统控制主要包括以下几个方面: 1. 定位控制:PLC根据操作需求控制链条正反向运行,使用高速计数器和内置快速输入点实现精准定位。 2. 料仓计数:行程开关监测料仓的位置变化,PLC的可逆计数器进行加减计数。 3. 自动判断正反向运行:根据目标料仓号与当前料仓号的差值,系统自动选择最短路径,节省时间和能源。 4. 正反向点动运行:设置正反向点动按钮,提供手动控制,同时利用二进制比较指令实现安全保护。 5. 目标料仓号及料位号设置:24个料仓和每个料仓的料位号在触摸屏上直观显示,通过PLC的内部保持继电器进行数据传输。 基于PLC的立体仓库控制系统通过高效的信息处理和精确的物料管理,极大地提升了立体仓库的自动化水平和运营效率,降低了人工操作的复杂性,增强了系统的稳定性和安全性。这一设计思路和实现方法为类似自动化项目的开发提供了宝贵的参考。
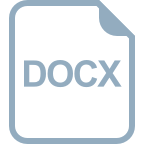
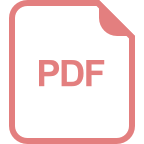
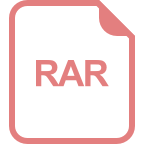
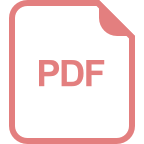
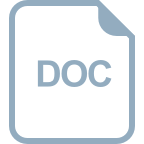
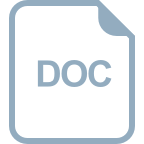
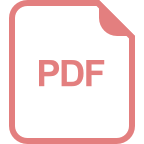
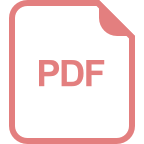
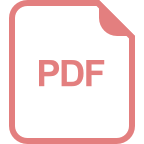
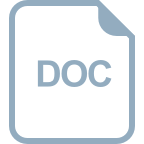
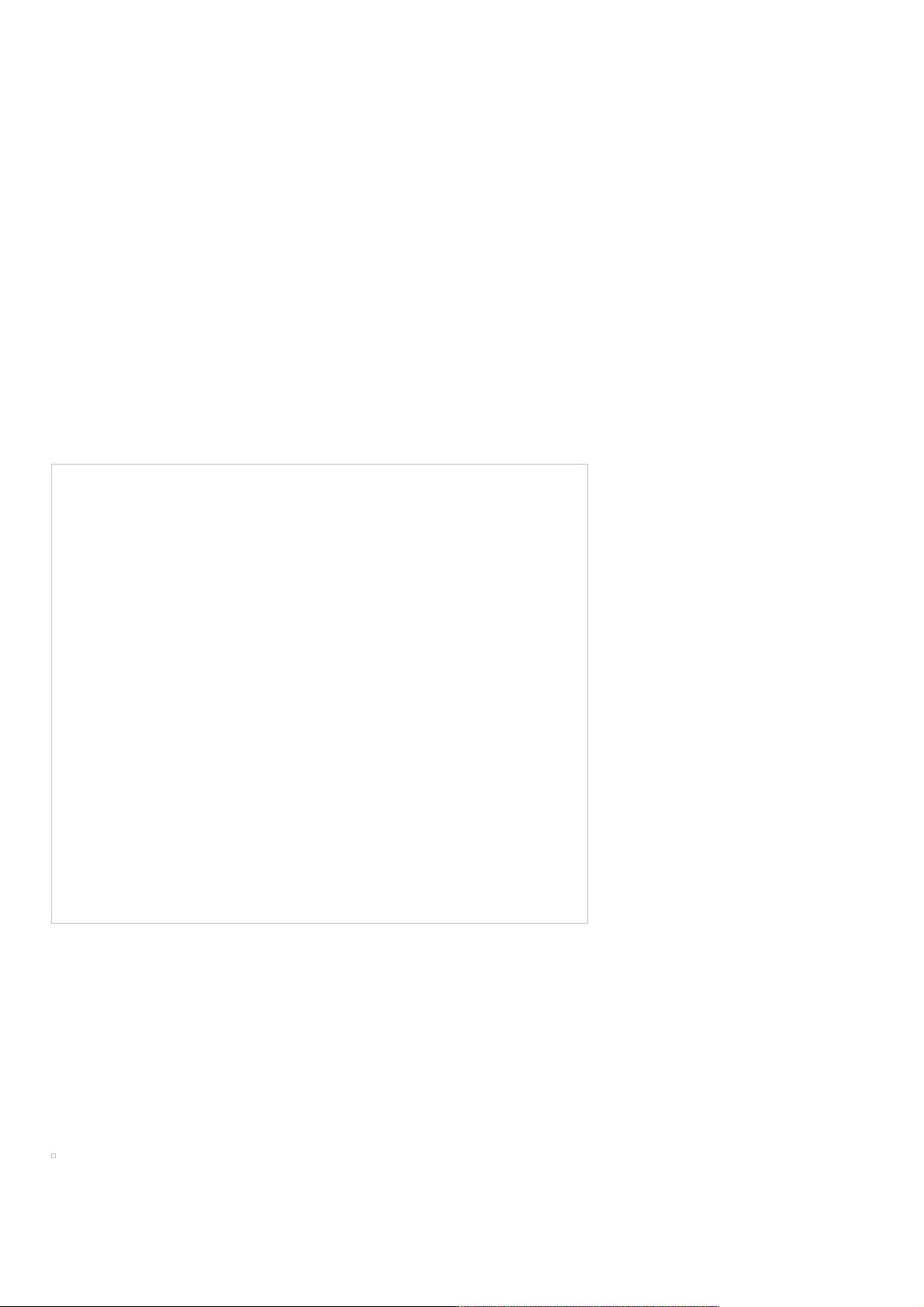
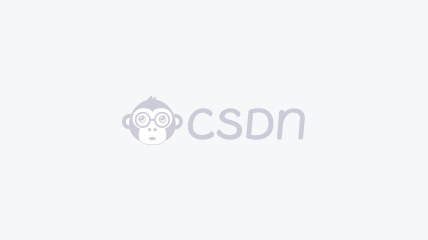
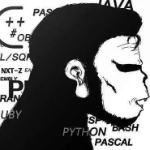
- 粉丝: 275
- 资源: 866
我的内容管理 展开
我的资源 快来上传第一个资源
我的收益
登录查看自己的收益我的积分 登录查看自己的积分
我的C币 登录后查看C币余额
我的收藏
我的下载
下载帮助

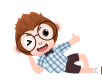
