
weixin_38744153
- 粉丝: 348
- 资源: 2万+
最新资源
- 西门子S7-1200流水线贴膜机项目程序,有KTP700触摸屏组态操作界面 程序包含.上下气缸控制,夹紧气缸控制,输送带电机控制,贴膜伺服控制旋转电机控制等类容 适合简单控制工艺及运动控制初学
- comsol电力变压器电磁场计算模型,通过简化高低压绕组,铁心,结构件和绝缘油的几何模型,得到变压器内部电磁场分布
- 西门子PLC1500大型程序 西门子PLC1500大型程序fanuc机器人焊装 包括1台西门子1500PLC程序,2台触摸屏TP1500程序 9个智能远程终端ET200SP Profinet连接 15
- Task-113-出租车计价
- HttpUrlConnectionUtilDemo-大炮打蚊子
- fishing-game-大炮打蚊子
- 有限信息,多智能体系统,鲁棒无碰撞编队控制,有文献参考 符合要求请放心联系,MATLAB,保证能够运行 simulink,复现
- MATLAB全桥或者半桥LLC谐振DC DC变器的设计与仿真 内含开环仿真、电压闭环仿真两个仿真文件 并含有电路参数仿真计算过程 支持最高版本2018b
- 基于模型参考自适应的永磁同步电机无感FOC 1.采用模型参考自适应MRAS来估计转速和转子位置,实现中高速下PMSM的无感运行,估计精度较高; 2.提供算法对应的参考文献和仿真模型,支持技术解答;拿后
- hustoj-重庆大学python题库答案
- 基于阻抗的微电网功率分配策略研究(文章复现),关键词:下垂控制,并联逆变器,阻抗
- Util-大炮打蚊子c++
- 一种微电网分布式电源的下垂控制策略(文章复现),关键词:下垂控制,并联逆变器,对等控制
- 汽车手动变速器sw18可编辑全套设计资料100%好用.zip
- 基于PreScan与Carsim的车道保持联合仿真 其中车道线识别算法通过采集单目摄像头数据,Ransac算法提取车道线;采用MPC控制器实现车道保持与循迹控制 内附
- 西门子1200博图程序冷却油泵PID控制系统,和多台油泵及水泵G120西门子变频器Modbud RTU通讯,画面采用西门子KTP700触摸屏,内有变频器参数 Modbus通讯报文详细讲解,PID带手动
资源上传下载、课程学习等过程中有任何疑问或建议,欢迎提出宝贵意见哦~我们会及时处理!
点击此处反馈


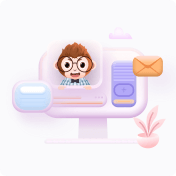