
weixin_38743737
- 粉丝: 376
- 资源: 2万+
最新资源
- 微信小程序养老院系统--论文pf-微信小程序毕业项目,适合计算机毕-设、实训项目、大作业学习.zip
- 健身小程序+ssm-微信小程序毕业项目,适合计算机毕-设、实训项目、大作业学习.rar
- 微信阅读小程序-微信小程序毕业项目,适合计算机毕-设、实训项目、大作业学习.zip
- 鲜花销售微信小程序--论文-微信小程序毕业项目,适合计算机毕-设、实训项目、大作业学习.zip
- 戏曲文化苑小程序bootpf-微信小程序毕业项目,适合计算机毕-设、实训项目、大作业学习.zip
- 懒人美食帮+springboot-微信小程序毕业项目,适合计算机毕-设、实训项目、大作业学习.rar
- 居住证申报系统+ssm-微信小程序毕业项目,适合计算机毕-设、实训项目、大作业学习.rar
- 小演员招募小程序的设计与开发_33d98-微信小程序毕业项目,适合计算机毕-设、实训项目、大作业学习.zip
- 课程答疑微信小程序+ssm-微信小程序毕业项目,适合计算机毕-设、实训项目、大作业学习.rar
- 乡村研学旅行平台 (小程序--论文pf-微信小程序毕业项目,适合计算机毕-设、实训项目、大作业学习.zip
- 汽车保养系统+ssm-微信小程序毕业项目,适合计算机毕-设、实训项目、大作业学习.rar
- 培训机构客户管理系统的设计+ssm-微信小程序毕业项目,适合计算机毕-设、实训项目、大作业学习.rar
- 奶茶点餐小程序ssm-微信小程序毕业项目,适合计算机毕-设、实训项目、大作业学习.rar
- 校园订餐小程序--论文-微信小程序毕业项目,适合计算机毕-设、实训项目、大作业学习.zip
- 校园二手交易平台小程序--论文-微信小程序毕业项目,适合计算机毕-设、实训项目、大作业学习.zip
- 社区二手物品交易小程序ssm-微信小程序毕业项目,适合计算机毕-设、实训项目、大作业学习.rar
资源上传下载、课程学习等过程中有任何疑问或建议,欢迎提出宝贵意见哦~我们会及时处理!
点击此处反馈


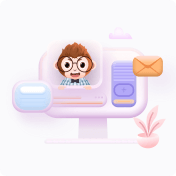