没有合适的资源?快使用搜索试试~ 我知道了~
Modeling of the 3D spatio-temporal thermal profile of joule-clas...
0 下载量 26 浏览量
2021-02-22
04:12:25
上传
评论
收藏 2.31MB PDF 举报
温馨提示
Thermal profile modification of an active material in a laser amplifier via optical pumping results in a change in the material’s refractive index, and causes thermal expansion and stress, eventually leading to spatial phase aberrations, or even permanent material damage. For this purpose, knowledge of the 3D spatio-temporal thermal profile, which can currently only be retrieved via numerical simulations, is critical for joule-class laser amplifiers to reveal potentially dangerous thermal featur
资源推荐
资源详情
资源评论
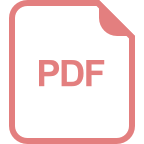
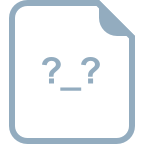
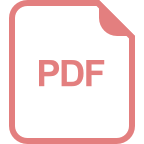
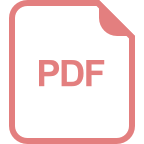
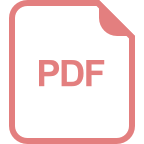
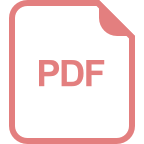
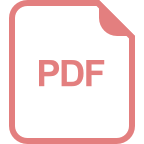
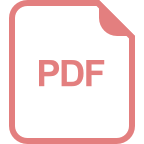
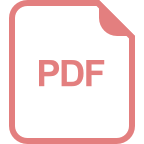
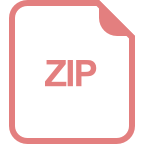
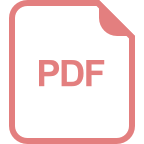
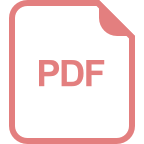
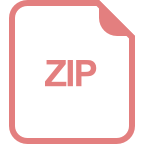
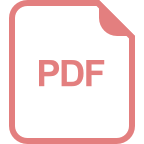
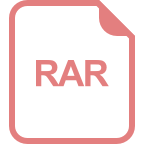
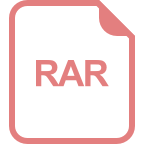
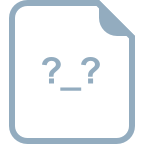
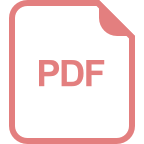
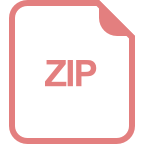
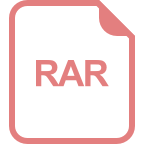
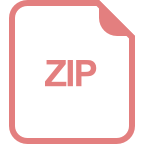
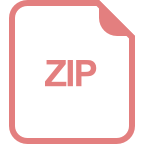
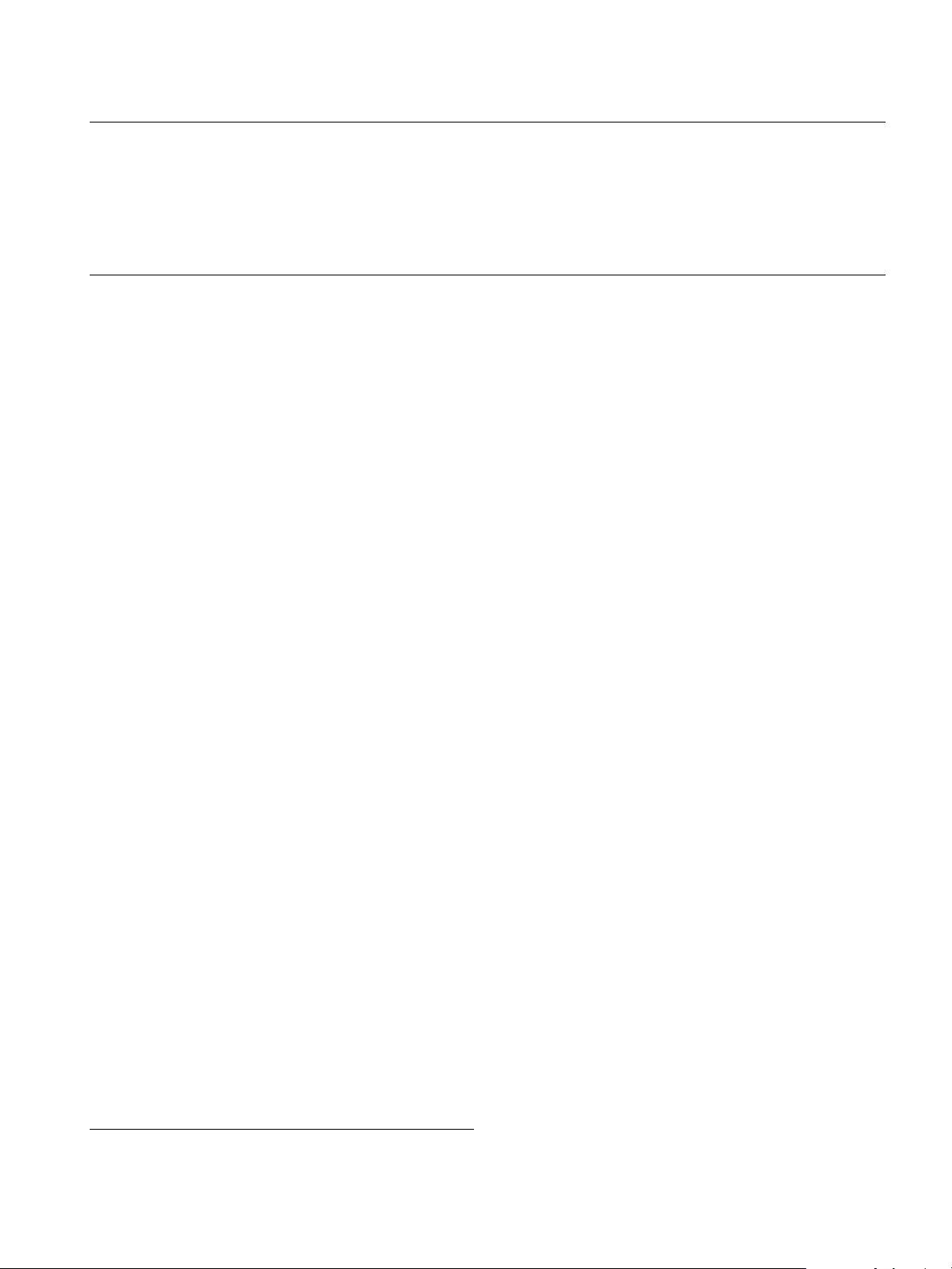
High Power Laser Science and Engineering, (2019), Vol. 7, e42, 7 pages.
© The Author(s) 2019. This is an Open Access article, distributed under the terms of the Creative Commons Attribution licence (http://creativecommons.org/
licenses/by/4.0/), which permits unrestricted re-use, distribution, and reproduction in any medium, provided the original work is properly cited.
doi:10.1017/hpl.2019.32
Modeling of the 3D spatio-temporal thermal profile of
joule-class Yb
3+
-based laser amplifiers
Issa Tamer
1,2
, Sebastian Keppler
1,2
, J
¨
org K
¨
orner
2
, Marco Hornung
1,2
, Marco Hellwing
2
, Frank Schorcht
1
,
Joachim Hein
1,2
, and Malte C. Kaluza
1,2
1
Helmholtz-Institute Jena, Fr
¨
obelstieg 3, 07743 Jena, Germany
2
Friedrich-Schiller-University Jena, Max-Wien Platz 1, 07743 Jena, Germany
(Received 8 March 2019; revised 4 May 2019; accepted 4 June 2019)
Abstract
Thermal profile modification of an active material in a laser amplifier via optical pumping results in a change in the
material’s refractive index, and causes thermal expansion and stress, eventually leading to spatial phase aberrations, or
even permanent material damage. For this purpose, knowledge of the 3D spatio-temporal thermal profile, which can
currently only be retrieved via numerical simulations, is critical for joule-class laser amplifiers to reveal potentially
dangerous thermal features within the pumped active materials. In this investigation, a detailed, spatio-temporal
numerical simulation was constructed and tested for accuracy against surface thermal measurements of various end-
pumped Yb
3+
-doped laser-active materials. The measurements and simulations show an excellent agreement and the
model was successfully applied to a joule-class Yb
3+
-based amplifier currently operating in the POLARIS laser system
at the Friedrich-Schiller-University and Helmholtz-Institute Jena in Germany.
Keywords: diode-pumped solid-state lasers; high intensity lasers; laser amplifiers; spatio-temporal thermal profile modeling; ytterbium
1. Introduction
Advances in relativistic laser plasma physics are reliant
on the optimization of state-of-the-art laser systems toward
higher peak and average powers. These laser pulses, when
focused to intensities in excess of 10
20
W/cm
2
, can acceler-
ate electrons
[1]
and ions
[2]
to relativistic velocities, as well
as generate X-rays
[3]
and high harmonics
[4]
. Attaining and
increasing such laser intensities requires the proper design,
characterization, and optimization of the final multi-pass
amplifier stages to amplify the seed laser pulse well into the
multi-joule regime while maintaining its spatial and temporal
fidelity.
Within these final multi-pass amplifier setups, large beam
diameters are necessary to reduce the fluence of the laser
pulse below the laser-induced damage threshold (LIDT) of
the active materials. Consequently, these large beam profiles
are particularly susceptible to effects leading to wavefront
aberrations, the ramifications of which are prominent due
to the long propagation distances typically found in non-
imaging joule-level multi-pass amplifiers. Such wavefront
aberrations occur in part due to the quantum defect, in which
a portion of the pump laser energy is transferred to the active
Correspondence to: I. Tamer, Helmholtz-Institute Jena, Fr
¨
obelstieg 3,
07743 Jena, Germany. Email: issa.tamer@uni-jena.de
material in the form of heat, resulting in a change in the
temperature profile that forms within the timescale of the
pump pulse. This pump-induced temperature change causes
a modification of the refractive index
[5]
, leads to thermal
expansion and stress, and alters the emission and absorption
spectra
[6]
of the laser material.
To mitigate the impact of these effects, narrowband diode-
pumped Yb
3+
-doped active materials can be employed,
which can provide a significantly lower quantum defect
of 9%
[6]
when compared to other dopants, such as Nd
3+
(24%
[7]
) or Ti
3+
(33%
[8]
). Present-day high-power Yb-
based laser systems have used this advantage to achieve
pulse energies higher than 50 J
[9]
and 100 J
[10]
within
pulse durations of 100 fs and 10 ns, respectively. De-
spite the reduced heat load within Yb
3+
-doped materials,
significant detrimental effects can still occur due to the
pump-induced thermal profile. The influence of strong ther-
mally induced
[5]
wavefront aberrations – in conjunction
with electronic contributions
[11]
– may heavily distort
[12]
the
amplified beam profile upon propagation. Additionally, the
spatially varying depolarization of the amplified seed beam
due to thermal stress
[5]
induced by the thermal gradient in
a multi-hundred-joule pumped active material can directly
lead to energy loss and possible spatial profile deformations
1
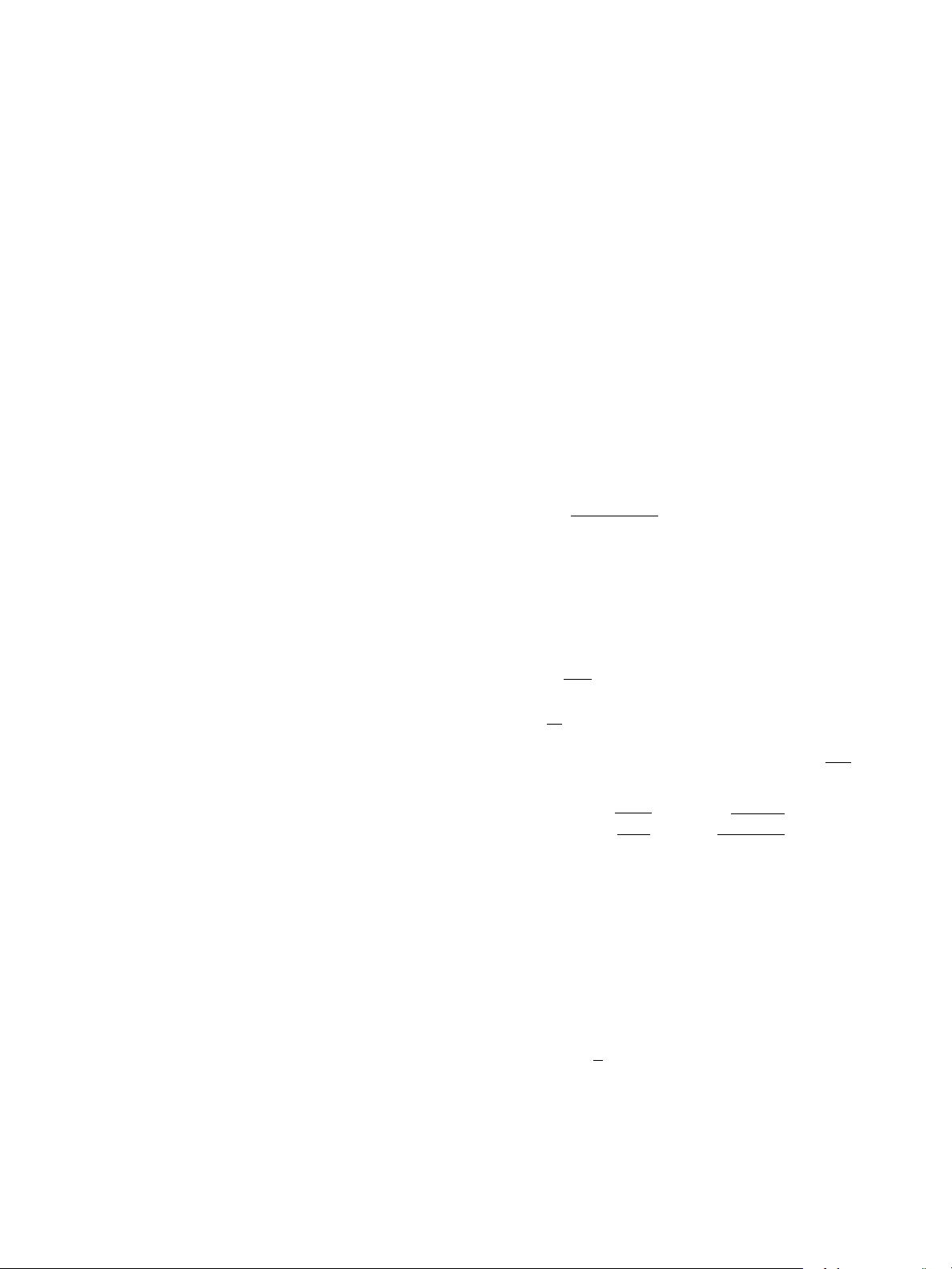
2 I. Tamer et al.
after interacting with polarization-sensitive optical compo-
nents within the laser system. If not properly characterized
and controlled, the thermal profile within a strongly pumped
active material can not only limit the maximum achievable
energy and final focusability of the laser pulse, but ulti-
mately, in cases of high thermal stress, result in permanent
damage to the active material.
A measurement technique that is capable of resolving
the complete spatio-temporal thermal profile of the pumped
active materials is challenging, due to the high emissiv-
ity of these materials. Measurements
[5]
utilizing thermal
infrared imaging cameras, for example, are only able to
access the surface temperature profiles with limited tem-
poral resolution, due to the camera’s long integration time
compared to the typical pump pulse durations utilized with
Yb
3+
-doped active materials
[6]
. Interferometric temperature
measurements or measurements of temperature-dependent
absorption
[13]
, on the other hand, only provide informa-
tion about the temperature averaged over the thickness of
the material. Recently, a novel scanning method
[14]
that
is capable of measuring the temperature inside the active
material has been reported. The applicability of this method
to joule-class laser amplifiers is currently limited, however,
due to the large active material radius in conjunction with
the typically low amplifier repetition rates, as well as the
vast material dataset required to calibrate the fitting function.
Therefore, a characterization of the temporally resolved 3D
thermal profiles of active materials under complex pumping
configurations, such as with the 3D multi-spot pump setup of
the POLARIS
[9]
laser system, cannot be adequately realized
with these methods alone.
However, with extensive knowledge of the material pa-
rameters, including the doping-dependent thermal properties
of the materials and the inversion-dependent absorption of
the pump pulse, a highly accurate numerical model can be
constructed and verified to provide access to the complete
spatio-temporal thermal profiles. Such thermal simulations
are a necessary tool to access the temperature profile within
the materials, which may strongly differ from the surface
temperatures. A pump profile that is optimized solely ac-
cording to the surface temperature distribution may produce
high thermal gradients elsewhere in the active material,
leading to significant wavefront aberrations and permanent
material damage from the thermally induced stress.
In this paper we describe the temporally and spatially
resolved temperature study of Yb:YAG, Yb:CaF
2
and
Yb:fluorophosphate glass
[15]
(Yb:FP15), which are com-
monly used in diode-pumped high-power laser systems such
as the POLARIS laser system at the Friedrich-Schiller-
University and Helmholtz-Institute Jena in Germany. A
simple pump geometry with a homogeneous, square-shaped
pump pulse together with a thermal camera was used as a
measurement setup to benchmark the detailed temperature
simulations, which showed excellent agreement with the
measurements. The calibrated measurement method was
then applied to the 3D pumping configuration of a joule-
class Yb:FP15-based amplifier operating in the POLARIS
laser system. The individually measured surface temperature
profiles of each pump pulse on the front and back sides of the
active material could be combined via a complex simulation
to enable access to the 3D spatio-temporal thermal profiles.
2. Thermal profile simulation
2.1. Heat transfer and active material parameters
Numerical simulations of the spatio-temporal behavior and
magnitude of the temperature profile throughout the pumped
material can be accomplished through the use of finite
element analysis software. Here, COMSOL (Version 5.2,
Sweden) was employed to construct a 3D model of the
pumped active material and solve the time-dependent heat
transfer equation
ρC
p
∂T (x, y, z, t)
∂t
− K
th
∇
2
T (x, y, z, t)
= η
h
α I (x, y, t)A(z, t), (1)
which predicts the flow of heat through a material via
conduction
[5]
, based on the given pump conditions.
The individual components of Equation (1) grant an under-
standing into how the material parameters contribute to the
thermal profile T (x, y, z, t) of the material. The specific heat
capacity C
p
[
J
kg · K
], which can be calculated using the Debye
model
[16]
for a given doping concentration, along with the
density ρ [
kg
m
3
] affects the temperature variation in the pulsed
regime. The magnitude of the temperature gradient in the
material scales with the thermal conductivity K
th
[
W
m · K
],
which can be determined from Gaum
´
e’s model as
[17]
K
th
= B ·
r
K
th,0
d
· arctan
p
K
th,0
· d
B
!
, (2)
where d is the doping concentration, K
th,0
is the undoped
thermal conductivity, and B is an empirically determined
[17]
fit parameter.
The term on the right-hand side of Equation (1) represents
the absorbed power density of the heat source within the
material. Here, the heat source is the pump laser with
intensity I (x, y, t), which exhibits a homogeneous spatial
profile and a square-like periodic temporal profile. The
strength of the absorbed power density is also determined by
the absorption α [
1
m
] of the material, which is dependent on
the dopant concentration, and the percentage η
h
of energy
transferred to heat through the quantum defect and other
nonradiative transitions due to material impurities. The form
of the pump laser depletion along the material’s length is
given by the parameter A(z, t ). The material parameters
剩余6页未读,继续阅读
资源评论
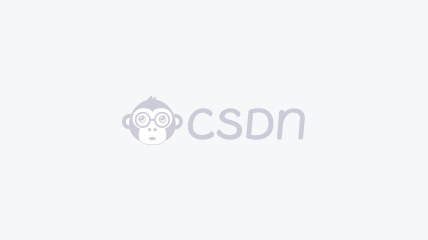

weixin_38732519
- 粉丝: 2
- 资源: 951
上传资源 快速赚钱
我的内容管理 展开
我的资源 快来上传第一个资源
我的收益
登录查看自己的收益我的积分 登录查看自己的积分
我的C币 登录后查看C币余额
我的收藏
我的下载
下载帮助

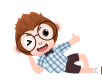
最新资源
资源上传下载、课程学习等过程中有任何疑问或建议,欢迎提出宝贵意见哦~我们会及时处理!
点击此处反馈


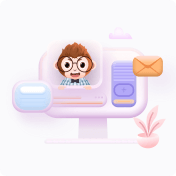
安全验证
文档复制为VIP权益,开通VIP直接复制
