在探讨非固态金属材料压力体积成形中的不等体积原理之前,首先需要了解固态金属体积成形中的等体积原理。传统上,在固态金属体积成形过程中,由于金属材料在塑性变形时体积保持不变,所以成形前的坯料体积与成形后的工件体积是相等的,这被称为等体积原理。这一原理是固态金属塑性成形的基本原理之一。 然而,在非固态金属材料的成形过程中,尤其是在液态或半固态条件下,材料会经历一系列复杂的物理变化,这些变化包括材料自身的冷却、凝固过程,以及在成形过程中由于模具和型芯在高温和高压作用下的变形和压头挤压等。这些因素导致成形前后的型腔体积和材料自身体积发生显著变化,形成不等体积现象。在非固态成形工艺中,为了获取致密的产品,要求成形后的材料体积必须小于成形前浇入模腔的材料体积,其差值被称为材料成形过程的可压缩体积。或者要求型腔的初始容积必须大于成形后金属占据的体积,其差值是挤入式型芯的挤入体积与压头的挤压运动体积之和。这就是非固态体积成形的不等体积原理。 现代材料成形技术已经覆盖从室温到合金液相线以上的全部温度范围,根据成形温度范围的不同,可以区分为液态成形、半固态成形和固态成形三大类。液态成形过程离不开非重力作用,往往需要施加压力以获得必要的塑性流动性和补缩效果。半固态成形技术从一开始也依赖于非重力作用,如压力,来完成充型和凝固过程。在这些非固态成形过程中,高强度的模具或铸型、提供非重力(多数为压力)的设备、以及合格的金属熔体是三个基本条件。此外,借助材料在非重力作用下的流变特性完成充型、凝固和补缩是至关重要的。 非固态体积成形的基本过程包括浇注、充型、冷却、凝固、变形、取件等六个基本环节,每个环节都会出现体积效应。这些体积效应与温度、压力关系密切,伴随每个环节结束时都会有相应的温度、压力和体积变化。为了方便分析,可以将浇注完毕时材料的温度和体积定义为初始温度T0和初始体积V0,工件取出模腔时的温度和体积定义为出模温度Tf和出模体积Vf。非固态金属体积成形过程中各环节的温度、固相分数和体积变化如图所示。 在浇注与充型环节中,金属熔体自身的体积效应不容忽视。对于纯液态成形而言,体积变化主要由温度降低引起,而对半固态熔体,体积变化还会受到固相分数变化的影响。金属熔体的液态体收缩系数αl以及凝固体收缩系数αs是描述这些体积变化的重要参数。在实际操作中,为了保证产品质量,需要精确控制成形过程中的温度和压力参数,以确保材料得到适当的凝固和补缩,避免缩孔和缩松等缺陷。 非固态金属材料压力体积成形中的不等体积原理是研究非固态材料成形过程的核心内容之一。这一原理揭示了非固态成形与固态成形过程的显著区别,并在成形工艺设计、质量控制及模具设计等方面提供了理论基础。通过对不等体积原理的理解和应用,可以更有效地控制成形工艺,提升产品品质。
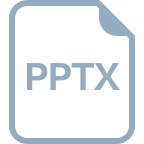
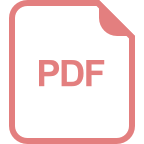
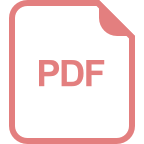
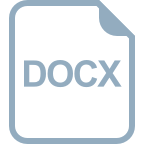
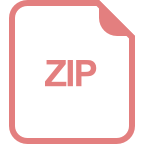
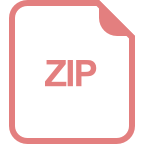
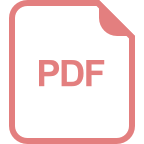
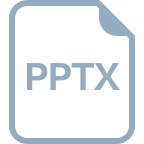
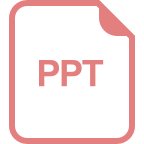
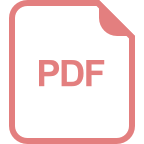
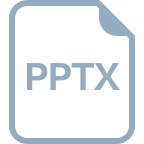
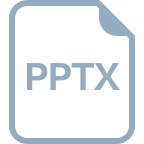
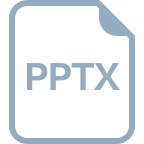
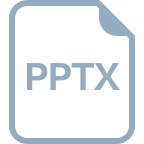
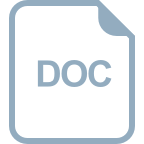
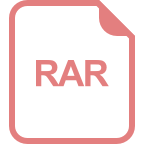
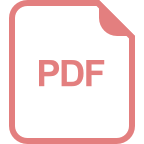
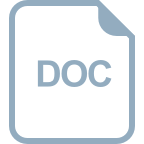
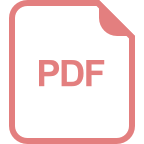
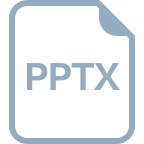
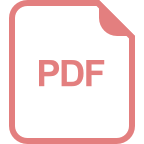
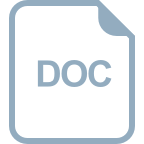
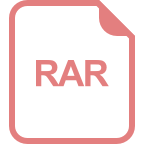
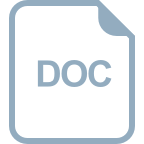
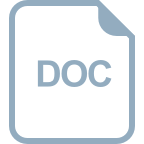
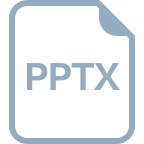
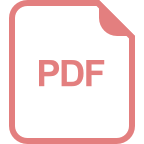
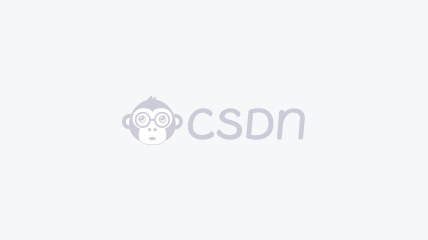

- 粉丝: 4
- 资源: 908
我的内容管理 展开
我的资源 快来上传第一个资源
我的收益
登录查看自己的收益我的积分 登录查看自己的积分
我的C币 登录后查看C币余额
我的收藏
我的下载
下载帮助

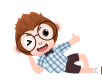
最新资源

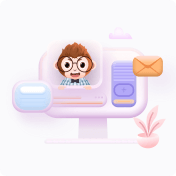
