没有合适的资源?快使用搜索试试~ 我知道了~
Disturbance and Friction Compensations in Hard Disk Drives Using...
0 下载量 140 浏览量
2021-02-21
05:30:27
上传
评论
收藏 730KB PDF 举报
温馨提示
In this paper, we show that by using two adaptive neural networks (NNs), each of which is tailored for a specific task, the tracking performance of the hard-disk-drive (HDD) actuator can be significantly improved. The first NN utilizes accelerometer signal to detect external vibrations and compensates for its effect on HDD position via feedforward action. The second NN is designed to compensate for pivot friction. The appealing advantage of the NN compensators is that the design does not involve
资源推荐
资源详情
资源评论
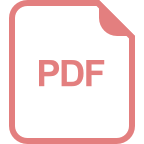
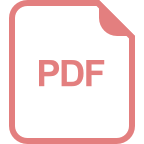
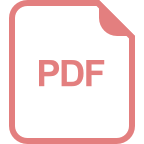
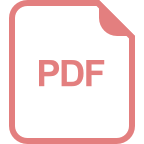
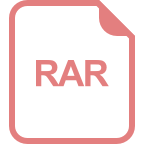
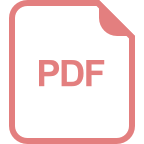
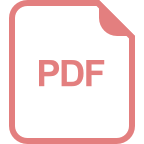
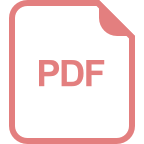
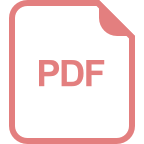
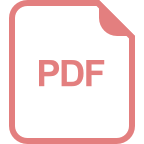
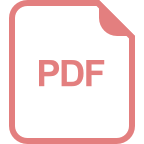
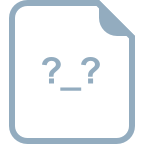
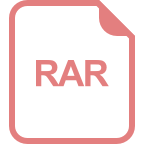
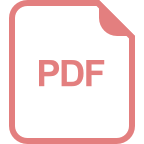
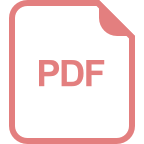
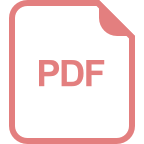
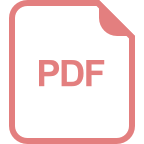
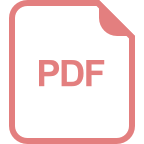
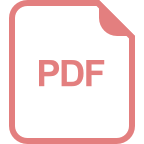
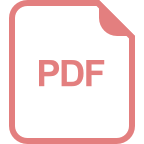
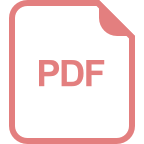
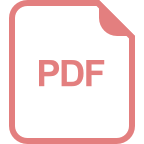
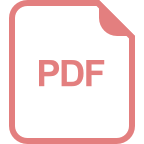
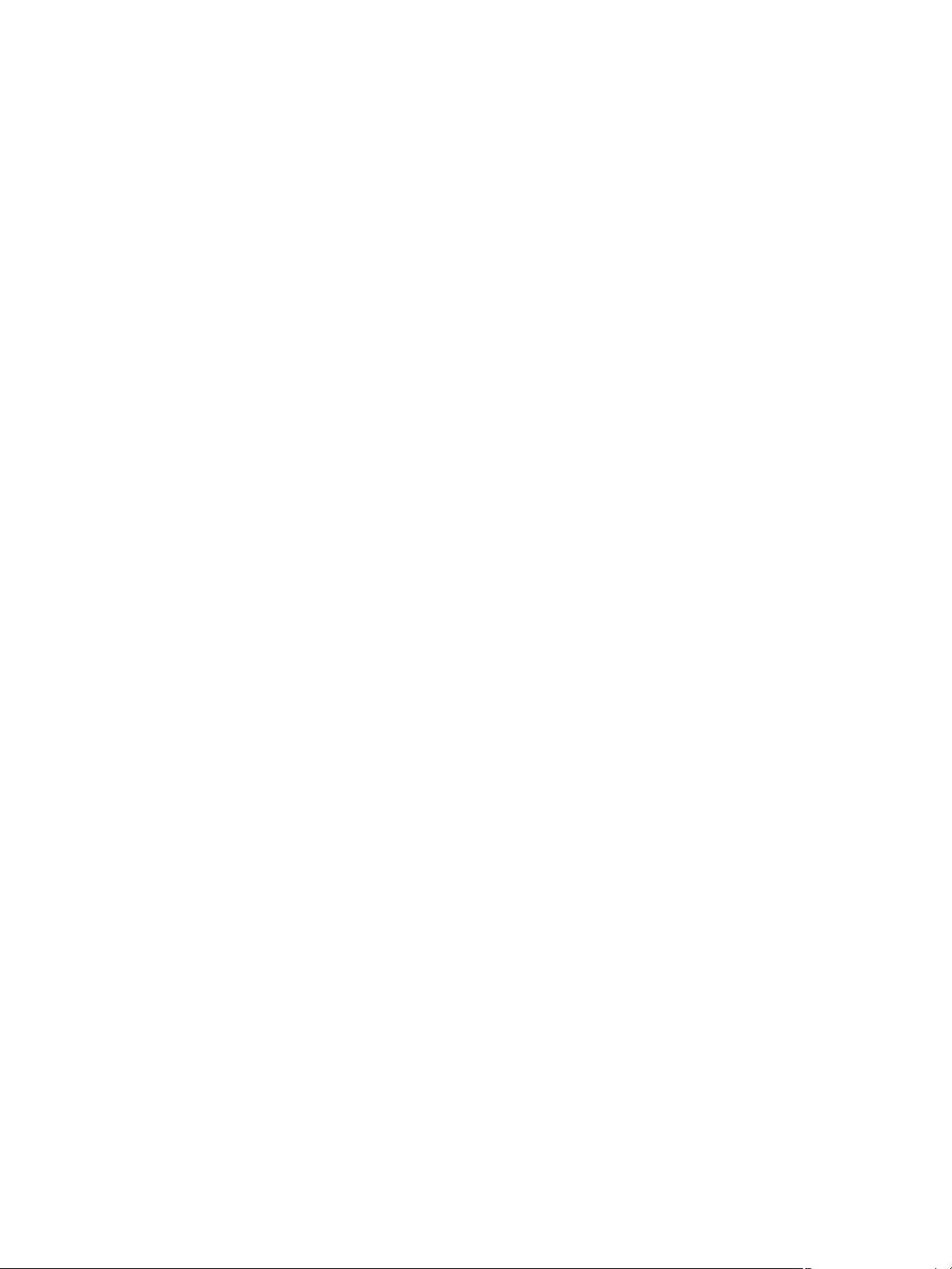
784 IEEE TRANSACTIONS ON INDUSTRIAL ELECTRONICS, VOL. 57, NO. 2, FEBRUARY 2010
Disturbance and Friction Compensations in Hard
Disk Drives Using Neural Networks
Chow Yin Lai, Student Member, IEEE, Frank L. Lewis, Fellow, IEEE, Venkatakrishnan Venkataramanan,
Xuemei Ren, Shuzhi Sam Ge, Fellow, IEEE, and Thomas Liew, Senior Member, IEEE
Abstract—In this paper, we show that by using two adaptive
neural networks (NNs), each of which is tailored for a specific task,
the tracking performance of the hard-disk-drive (HDD) actuator
can be significantly improved. The first NN utilizes accelerometer
signal to detect external vibrations and compensates for its effect
on HDD position via feedforward action. The second NN is de-
signed to compensate for pivot friction. The appealing advantage
of the NN compensators is that the design does not involve any in-
formation on the plant, sensor, disturbance dynamics, and friction
model. The stability of the proposed scheme is analyzed by the
Lyapunov criterion. Experimental results show that the tracking
performance of the HDDs can be improved significantly with the
use of the NN compensators as compared to the case without
compensation.
Index Terms—Disturbance feedforward, friction compensation,
hard disk drives (HDDs), neural networks (NNs).
I. INTRODUCTION
I
N CONFORMITY with the increase of the data density
on magnetic disk drives in recent years, the data track
width has reduced significantly. This means that the tracking
accuracy of the voice-coil-motor (VCM) actuator must be
improved. However, two major trends of the hard-disk-drive
(HDD) development are posing challenges to the quest for
better tracking performance of the VCM actuator. First, the
HDDs are increasingly used in mobile devices and thus are
subject to more external vibrations and shocks. Second, with
the current trend toward smaller form factors and smaller VCM
torque, the nonlinear pivot friction becomes more pronounced.
Thus, the effect of external disturbances and friction should be
explicitly taken into account during the design of HDDs servo
Manuscript received April 14, 2008; revised July 1, 2009. First published
July 24, 2009; current version published January 13, 2010. This work was
supported in part by the National Science Foundation (NSF) under Grant
ECCS-0801330, in part by the Army Research Office under Grant W91NF-
05-1-0314, in part by the Science and Engineering Research Council, Agency
for Science, Technology and Research (A*STAR) under Grant 052 101 0097,
and in part by the National Natural Science Foundation of China under
Grant 60974046.
C. Y. Lai is with the NUS Graduate School for Integrative Sciences and
Engineering, National University of Singapore, Singapore 117456 (e-mail:
g0601819@nus.edu.sg).
F. L. Lewis is with the Automation and Robotics Research Institute,
The University of Texas at Arlington, Fort Worth, TX 76118 USA (e-mail:
lewis@uta.edu).
V. Venkataramanan and T. Liew are with the Data Storage In-
stitute, A
∗
STAR, Singapore 117608 (e-mail: Venka_V@dsi.a-star.edu.sg;
LIEW_Yun_Fook@dsi.a-star.edu.sg).
X. Ren is with the Department of Automatic Control, Beijing Institute of
Technology, Beijing 100081, China (e-mail: xmren@bit.edu.cn).
S. S. Ge is with the Department of Electrical and Computer Engineering, Na-
tional University of Singapore, Singapore 117576 (e-mail: samge@nus.edu.sg).
Digital Object Identifier 10.1109/TIE.2009.2027257
system, so that the desired positioning accuracy can be achieved
even under the presence of external disturbances and friction.
To reduce the effect of the disturbances on the HDDs, a num-
ber of authors have proposed using accelerometers to measure
external disturbances and injecting the accelerometer signal to a
feedforward controller, which then outputs a feedforward signal
into the system [1]–[8]. Bando et al. [3] identified the transfer
function from external vibration to plant input via recursive
least square algorithm using the acceleration signal and the dis-
turbance signal which is estimated from disturbance observer.
Du et al. [4] applied the H
∞
method in state space to design
the feedforward controller to compensate for external vibration
impact on the positioning accuracy of the VCM actuator. The
identification of both the plant and the disturbance model is
considered by Pannu and Horowitz in [5], where they designed
an adaptive f eedforward controller acting as an add-on com-
pensator to an existing fixed compensator. In [6], Jinzenji et al.
used the dual accelerometers to detect angular acceleration in
HDD and compensate for its effects on the position accuracy. In
[7], Usui et al. established an adaptive feedforward control with
the finite-impulse-response (FIR) filter. However, the gradient
algorithm for updating the coefficients of the FIR controller
relies on the exact internal model. White and Tomizuka [8]
developed an infinite-impulse-response (IIR) filter and the FIR
filter based on the filtered-x least mean-square (LMS) algorithm
to compensate for the effects of the disturbances. To assure con-
vergence of the filtered-x LMS algorithm, however, the product
of the unknown dynamics and its estimated inverse needs to be
strictly positive real. It is evident that in almost all of the earlier
feedforward control schemes, the mathematical models of the
disturbance dynamics must be known or partly known, and the
sensor model and disturbance dynamics are usually restricted
to be linear. The need for the disturbance dynamics is a major
drawback because they can be time varying, nonlinear, and can
rarely be modeled accurately.
Friction can cause tracking errors, large settling time, and
overshoot. The methods for friction compensation can be di-
vided into two categories, namely, the model-based [9]–[14]
and the nonmodel-based compensations [15]–[19]. In the
model-based approach, various friction models are proposed,
their parameters identified either offline or adaptively, and
the output of the friction models injected into the plant to
cancel the true friction force. The drawback of the model-
based friction compensator is the reliance on an accurate model;
thus, a simple model does not provide satisfactory friction
compensation, whereas a highly accurate model is difficult to
parameterize. The nonmodel-based techniques include using
0278-0046/$26.00 © 2010 IEEE
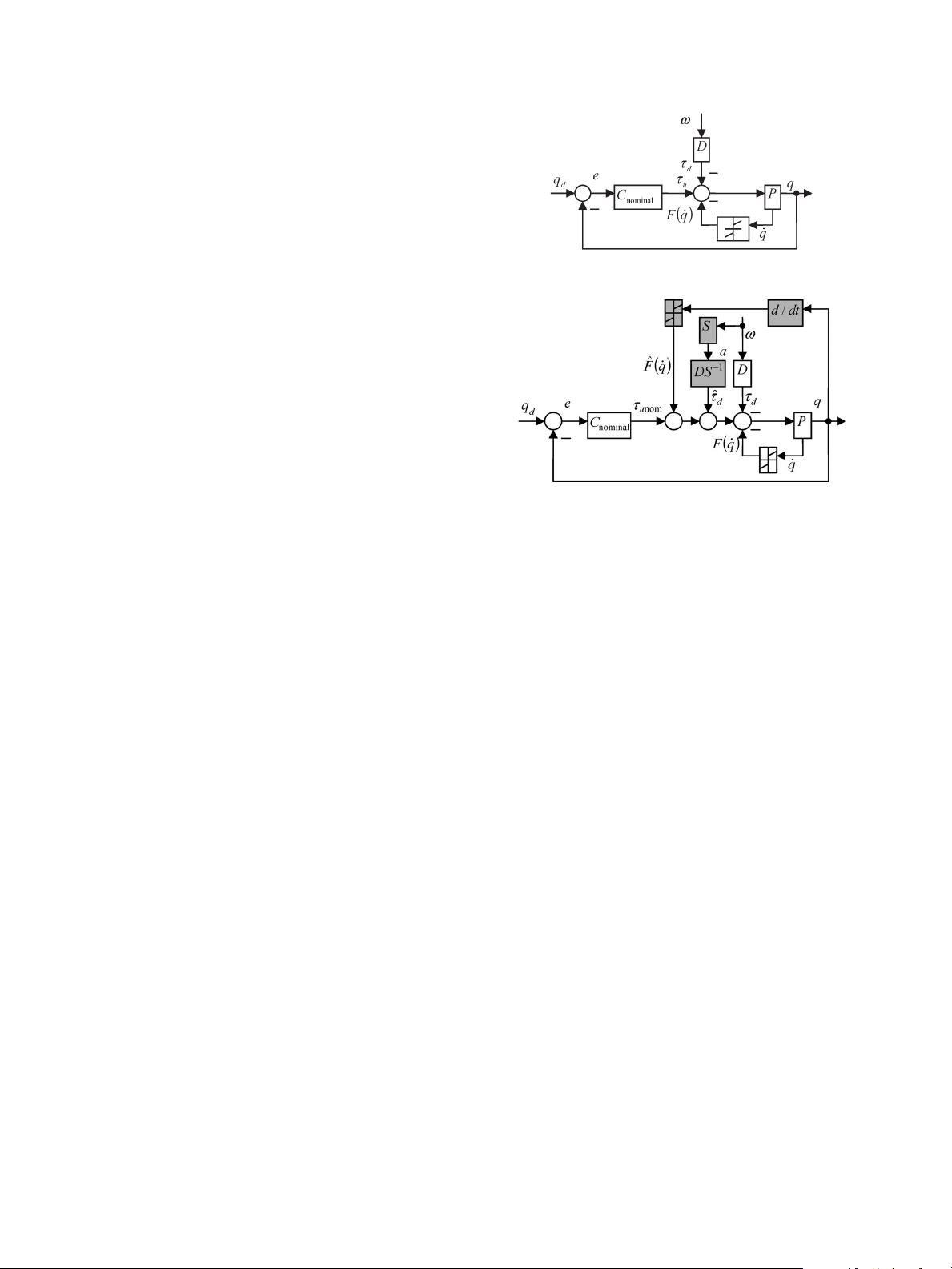
LAI et al.: DISTURBANCE AND FRICTION COMPENSATIONS IN HARD DISK DRIVES 785
disturbance observer [15], [16], fuzzy logic [17], as well as
Kalman filter [18], [19] to estimate and compensate for the fric-
tion force. The disturbance observer and Kalman filter have the
disadvantage in that a plant model is needed. The fuzzy logic
may also be too complicated to be used in the industry [10].
Because of the distinct advantages of neural networks (NNs)
as nonlinear controllers over conventional controllers in achiev-
ing desired performances, they have received considerable at-
tention in the control community [20]–[26]. The efficacy of NN
feedforward compensator in rejecting the effect of disturbances
for improving tracking accuracy was demonstrated in [27] and
[28]. In [27], Lin and Hsiao made use of the NN feedforward
control to eliminate the nonlinear disturbance torque in seeker
stabilizing loop. In [28], an adaptive NN feedforward compen-
sator was developed for the idle-speed control of a car engine.
Although these NN disturbance rejection schemes showed good
simulation results, there is a lack of theoretical results regarding
the stability analysis of the closed-loop system.
There are also some papers dedicated to friction compen-
sation using NNs. In [29], the NN is trained offline using
estimated friction force which is obtained by comparing the real
system output and the output of a virtually friction-free model.
Huang et al. [30], as well as Kim and Lewis [31], designed
adaptive schemes to bypass the need for offline training of
the NN. The problem related to [29]–[31] is that the NN tries
to approximate the friction hard nonlinearity via continuous
functions, and this may require many NN nodes and many
training iterations to yield good results. In [32], Selmic and
Lewis augmented their NN with some “jump approximation
functions” to achieve a better approximation of the friction
nonlinearity.
In this paper, we show that the tracking performance of an
HDD actuator can be improved by using two adaptive NNs,
each of which is tailored for a specific task. The first NN utilizes
accelerometer signal to detect external vibrations and compen-
sates for its effect on HDD position via feedforward action.
This disturbance-feedforward compensator can be interpreted
as a nonlinear FIR filter, which is the extension of linear FIR
filter whose basis function is linear. The second NN is designed
to compensate for the pivot friction. No dynamic knowledge
of the plant, sensor, disturbance, and friction is needed in the
design of the NN compensators. The stability of the proposed
scheme is analyzed by the Lyapunov criterion. Experimental
results show that the tracking performance of the HDDs can
improve significantly with the use of the NNs as compared to
the case without compensation.
This paper is organized as follows. Section II gives the prob-
lem statement. In Section III, we present our control structure.
The NN disturbance and friction compensators are derived
in Section IV. In Section V, detailed information about the
experiment will be given, followed by experimental results in
Section VI. Finally, in Section VII, conclusions will be drawn.
II. P
ROBLEM STATEMENT
The dynamics of the HDD system P can be expressed as
M ¨q + F (˙q)+τ
d
= τ
u
(1)
Fig. 1. Control structure of the HDD without additional compensations.
Fig. 2. Control structure with disturbance and friction compensations.
where q denotes the position of the VCM actuator, M is the
unknown system inertia, τ
u
is the control input torque, F (˙q)
represents the velocity-dependent friction force, and τ
d
is the
disturbance torque acting on the system input which i s caused
by external vibration ω via the dynamics D (Fig. 1). Note that
friction can also depend on position, but this dependence is
negligible [32] and thus is neglected in this paper.
Let q
d
be the desired position. The tracking error e can be
expressed as
e = q
d
− q. (2)
The usual control scheme for external vibration compen-
sation and friction compensation is shown in Fig. 2. There,
S represents the accelerometer which measures the external
vibration ω and generates the accelerometer signal a. If one
knows the accurate model for D, S, and friction, one can
construct the disturbance compensator as DS
−1
and the friction
compensator using the friction curve. However, in r eality, D
and friction are difficult to be modeled exactly, thus hindering
the full potential of the compensation scheme.
The objective is thus to design the disturbance-feedforward
compensator and friction compensator without explicit knowl-
edge about the disturbance model, sensor dynamics, and accu-
rate friction model.
III. O
VERALL CONTROL STRUCTURE AND INPUT
DATA PREPROCESSING
To bypass the need to explicitly model the disturbance,
sensor, and friction dynamic, we use NNs to construct our
compensators. As shown in Figs. 3 and 4, we use two NNs for
two different tasks.
The first NN, designed for disturbance attenuation, takes the
accelerometer signal a as input data. This signal path is purely
feedforward, thus we name the NN disturbance-feedforward
compensator NN
FF
. The second NN, designed for f riction
剩余8页未读,继续阅读
资源评论
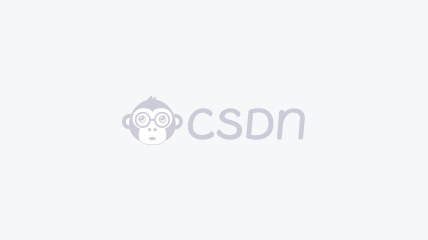

weixin_38713061
- 粉丝: 2
- 资源: 939
上传资源 快速赚钱
我的内容管理 展开
我的资源 快来上传第一个资源
我的收益
登录查看自己的收益我的积分 登录查看自己的积分
我的C币 登录后查看C币余额
我的收藏
我的下载
下载帮助

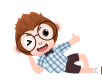
最新资源
资源上传下载、课程学习等过程中有任何疑问或建议,欢迎提出宝贵意见哦~我们会及时处理!
点击此处反馈


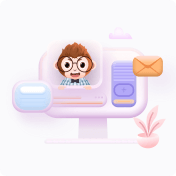
安全验证
文档复制为VIP权益,开通VIP直接复制
