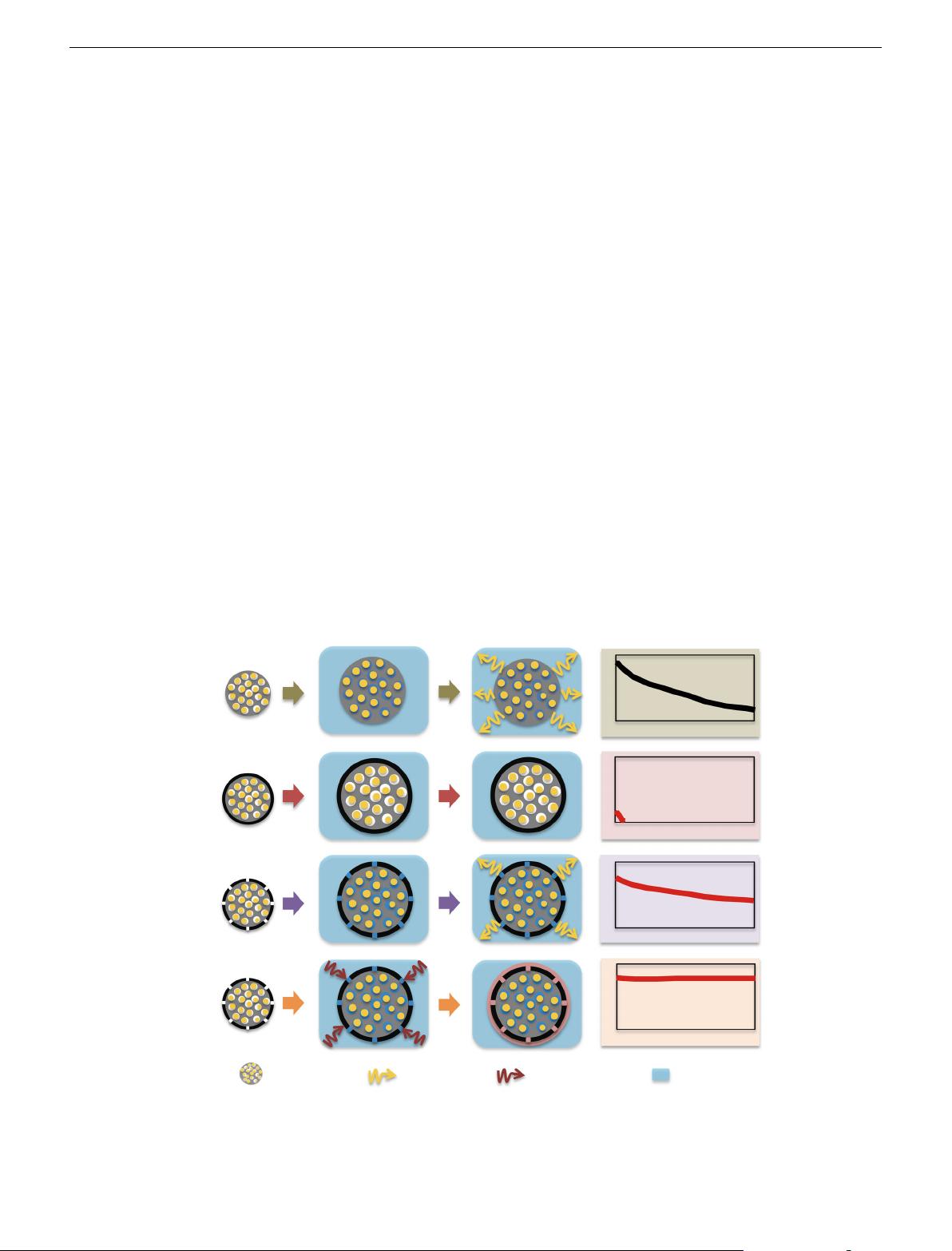
R
echargeable lithium–sulfur (Li–S) batteries are widely
expected to be the next-generation high-density energy
storage technology since the low-cost sulfur cathode has a
high theoretical specific capacity of 1672 mAh g
–11, 2
. The
operating mechanism of a Li–S battery is based on a series of
redox reactions between elemental sulfur (S
8
) and its polysulfide
derivatives Li
2
S
n
2−
(1 ≤ n ≤ 8). The cathode material experiences
a complex phase transition from solid S
8
to dissolved polysulfide
ions to insoluble Li
2
S
2
and Li
2
S. When combined with the
reversible lithium metal stripping/plating process at the anode,
the Li–S batteries provide a theoretical energy density of 2600
Wh/kg, which assumes the complete conversion of S
8
to Li
2
S
3
.
However, the commercialization of Li–S technology depends
on the solution to multiple critical issues that involve the
electrolyte and Li anode. For example, one of the key problems in
Li–S batteries has been the shuttle effect in the cathode that is
described as follows. First, the polysulfide ions that are formed at
the cathode are dissolved in the electrolyte and may diffuse to the
anode where they are reduced to lower polysulfides. Then, the
ions diffuse back to the cathode where they are reoxidized.
This back and forth transport, i.e., “shuttle” between the cathode
and anode may be continuous
4
and thus give rise to the
deposition of non-conductive Li
2
S
2
or Li
2
S on the Li anode,
the consumption of sulfur species and a poorly controlled
Li/electrolyte interface. These effects lead to a low Coulombic
efficiency, a high self-discharging rate and a fast decay in capacity
(Fig. 1a, the “no wrapping” case)
5
.
Various approaches have been devised to suppress the shuttle
effect
6–14
, among which a major strategy is to wrap the sulfur
material with a diffusion barrier layer to confine the solvated
polysulfides within the cathode material. The sulfur wrapping
strategy typically involves the preparation of carbon–sulfur
composite particles with a wrapping layer and then the wrapped
C/S composite is assembled into coin cells for testing. Such a
pre-battery-assembly wrapping approach has achieved good
results, which include a greatly suppressed shuttle effect and
improved cycling stability
15–17
. However, a dilemma exists in
designing the wrapping layer when using this approach, as
illustrated in Fig. 1b. If the preassembly wrapping layer was
designed to be perfectly compact and tight (to completely block
the polysulfide diffusion), the electrolyte would not infiltrate the
C/S composite in the assembled cell. Then, the battery will exhibit
poor performance. Alternatively, if the preassembly wrapping
layer was imperfectly designed with pores and/or cracks that
allow for the penetration of the electrolyte into the C/S composite,
solvated polysulfides can also leak out of the wrapping layer via
these defects, which can lead to improved but diminishing
performance (Fig. 1c). The latter scenario represents most sulfur
wrapping work reported to date
15–17
.
Here, for the first time, we propose and demonstrate an in situ
wrapping approach. In Fig. 1d, C/S composite particles are
imperfectly coated with a wrapping layer, and the material is
assembled into coin cells. The imperfect wrapping layer allows
the infiltration of adequate electrolyte into the C/S composite
particles. Significantly, a special functional additive is added to
the electrolyte to react with the initially imperfect wrapping layer
to form a second wrapping layer after the battery is assembled.
The second, post-assembled and in situ-formed wrapping layer is
designed to be compact and tight to completely block the shuttle
effect, which allows polysulfide dissolution into the electrolyte
within the interior of the wrapped composite particles. The coin
cells with an in situ wrapped C/S cathode demonstrate an initial
Polysulfides Electrolyte
Materials Cycling
Capacity Capacity
Functional additive
Capacity
Cycle number
Cycle number
Cycle number
Cycle number
Perfect in situ wrapping
Perfect pre-assembly
wrapping
Cell assembly
Imperfect pre-assembly
wrapping
Performance
Capacity
No wrapping
C/S composite
a
b
c
d
Fig. 1 Schematic illustration of the unique in situ wrapping strategy for lithium–sulfur cathode structures. a The no wrapping case, which exhibits severe
capacity decay during cycling. b Perfect wrapping of the C/S materials prior to battery assembly, which exhibits poor overall performance due to the lack of
electrolyte in the active material. c Imperfect wrapping of the cathode material prior to battery assembly, which exhibits improved cycle stability compared
with the no wrapping case. d Perfect post-assembly in situ wrapping of the cathode material, which exhibits ideal cycle stability using a blocking polysulfide
shuttle while allowing for electrolyte infiltration in the active material
ARTICLE NATURE COMMUNICATIONS | DOI: 10.1038/s41467-017-00656-8
2 NATURE COMMUNICATIONS
|
8: 479
|
DOI: 10.1038/s41467-017-00656-8
|
www.nature.com/naturecom munications