
weixin_38662367
- 粉丝: 5
- 资源: 912
最新资源
- 西门子数控系统调试与通讯:828D、840D、808D的参数配置、梯形图修改及外部IO增加案例分享,西门子数控系统调试与配置手册:涉及828D、840D与808D系统的参数调整、梯形图修改与外部通讯实
- 中国各类互联网应用的用户规模数据.zip
- 中国各省地图(包含港澳台) 山西(shanxi)陕西(shanxi1)
- E000620医院体检医疗健康类网站模板+PHP+Mysql+响应式+CMS+建站模板
- 中国各省对应各市级地图json
- 大模型基础-30分钟一文了解大模型基础知识(人工智能必读).zip
- COMSOL模拟:二氧化碳充装与输气管道泄漏的耦合温度场分析,输出速度与温度分布,COMSOL模拟:二氧化碳充装与输气管道泄漏的耦合温度场分析,输出速度与温度分布,comsol 二氧化碳充装二氧化碳输
- 基于python开发的简单的windows桌面画笔功能,全部使用快捷键操作(python源码+图文教程),开箱即用,非常优质的资源
- C#上位机与西门子PLC通讯教程:数据读取存储、报表生成、报警历史查询及变量自定义配置实战案例详解,C#上位机与西门子PLC通讯教程:数据读取存储、报表生成、报警历史查询及变量自定义配置实战案例详解
- 基于遗传算法的锂电池二阶RC模型参数辨识技术研究-附Matlab程序与多种工况充放电数据集(DST、FUDs、US06、BJDST等八种),基于遗传算法的锂电池二阶RC模型参数辨识技术研究-附Ma
- 利用格子玻尔兹曼方法LBM D1Q3模型在Matlab中模拟一维扩散方程的研究,使用格子玻尔兹曼方法LBM D1Q3模拟一维扩散方程的Matlab实现与应用研究,使用格子玻尔兹曼方法LBM D1Q3模
- 流水线电机变频调速系统设计 MATLAB电路建模仿真
- 2022年美国各州基本经济统计数据.zip
- 基于Transformer的Matlab代码:数据回归与多场景预测工具箱,Transformer在数据回归分析中的应用-基于Matlab代码的实战教学,Transformer回归 Matlab代码
- Sigma-Delta ADC Matlab模型集合:包含CTSD调制器、FFT分析、动态静态特性仿真与教程,方便入门学习,Continuous-Time Sigma-Delta ADC Matlab
- 基于Comsol仿真的兰姆波导波在钢板中的传播及裂隙检测分析,Comsol仿真中兰姆波导波在有限尺寸钢板内传播的裂隙检测技术研究,Comsol仿真无损检测时产生的兰姆波 导波在宽度和厚度有限的钢板中传
资源上传下载、课程学习等过程中有任何疑问或建议,欢迎提出宝贵意见哦~我们会及时处理!
点击此处反馈


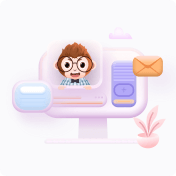