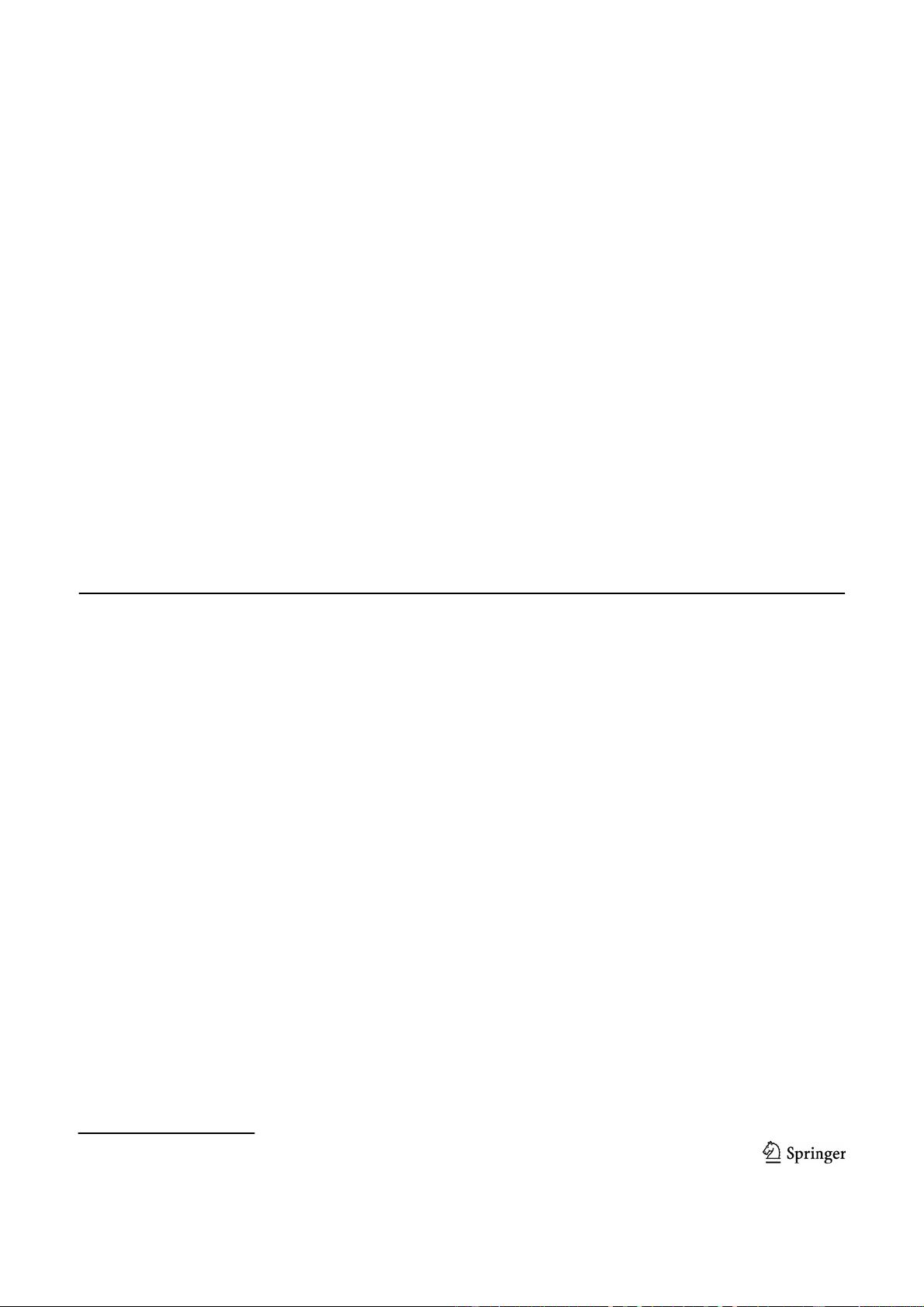
International Journal of Minerals, Metallurgy and Materials
Volume 17, Number 1, February 2010, Page 32
DOI: 10.1007/s12613-010-0106-1
Corresponding author: Hai-yan Tang E-mail: tanghaiyan@metall.ustb.edu.cn
© University of Science and Technology Beijing and Springer-Verlag Berlin Heidelberg 2010
Thermodynamic analysis on the formation mechanism of MgO·Al
2
O
3
spinel type inclusions in casing steel
Hai-yan Tang and Jing-she Li
School of Metallurgical and Ecological Engineering, University of Science and Technology Beijing, Beijing 100083, China
(Received: 21 December 2008; revised: 19 January 2009; accepted: 7 February 2009)
Abstract: MgO·Al
2
O
3
spinel type inclusions in casing steel were analyzed by scanning electron microscope (SEM) and energy dispersive
spectrometer (EDS). The results show that there are three forms. One is pure MgO·Al
2
O
3
spinel, another is the composite oxide of the
Mg-Al-Ca-Si-O system, and the third is the complex with oxide as a core covered by sulfide. The formation mechanisms were studied. The
influences of slag basicity and vacuum degree on the magnesium content during the vacuum treatment of molten steel and furnace lining in
molten steel were calculated with the coexistence theory of slag structure. The results show that the magnesium content increases with the
increase in slag basicity and aluminum content in molten steel, and decreases with the increase in CO partial pressure.
Keywords: magnesium-aluminum spinel; basicity; theoretical model; formation mechanism
1. Introduction
Casing is an important material for oil fields. It can rein-
force the wall of an oil well and protect the hole of the oil
well, and its destruction can lead to the failure throughout
the well. Therefore, not only high strength, uniform and sta-
ble quality, strong corrosion, and wear resistance are re-
quired for casings, but also the capacity to support all kinds
of loads such as pulling, pressing, twisting, and bending is
needed.
The tests show that the MgO·Al
2
O
3
spinel type inclusion
in the tube is one of the important factors affecting the qual-
ity of the casing. Therefore, it is very necessary to study its
formation mechanism and effect factors to control it in pro-
duction.
There have been some investigations [1-4] on the mecha-
nism of MgO·Al
2
O
3
spinel in stainless steel melts, but sys-
tematical theory analyses are few. Because it is difficult to
measure and calculate the activity of every component of a
multicomponent slag, the activities of some components are
often assumed to be 1 in most investigations. In fact, their
activities are impossible to be 1 for these components at
high temperature.
The coexistence theory is used to calculate the activity of
the slag component. Based on the thermodynamic data col-
lected by predecessors, the theory deals with many problems
such as oxidizing ability of slag, manganese distribution
between slag and steel, desulphurization and dephosphoriza-
tion ability of slag, and activity of molten salt and aqueous
solution, achieving uniform results with reality [5-13]. In
this theory, the mass action concentration of the component
is activity. In the paper, according to the actual production, the
mass action concentration model of
CaO-MgO-FeO-Al
2
O
3
-SiO
2
slag systems was chosen to calcu-
late the activities of components relative to the formation of
MgO·Al
2
O
3
spinel, and further to study the influence law of slag
components, vacuum treatment, and furnace lining on the mag-
nesium content in molten steel.
2. Forms of MgO·Al
2
O
3
spinel type inclusions
observed in casing steel
The composition of casing steel in the research (wt%) is
0.39 C, 0.22 Si, 1.52 Mn, 0.015 P, 0.007 S, 0.10 Mo, 0.020
Al, 0.12 V, 0.25 Cu, and 0.04 Cr.