
weixin_38540819
- 粉丝: 7
- 资源: 830
最新资源
- weixin小程序项目基于微信小程序的学生公寓电费信息管理系统+ssm.zip
- weixin小程序项目基于微信小程序的四六级词汇+ssm.zip
- 通用打印bar,计算平均等组件
- 基于simulink的中性点不接地和消弧线圈接地系统单相故障仿真分析
- weixin小程序项目基于微信小程序的童装商城的设计与实现+ssm.zip
- weixin小程序项目基于微信小程序的商品展示+ssm.zip
- weixin小程序项目基于微信小程序的社区团购+ssm.zip
- weixin小程序项目基于微信小程序的科创微应用平台设计与实现+ssm.zip
- weixin小程序项目基于微信平台的旅游出行必备商城小程序+ssm.zip
- weixin小程序项目基于微信小程序的S店客户管理系统+ssm.zip
- carsim,prescan,simulink三者联合仿真,软件版本为carsim2020.0,prescan8.5,matlab2020b,紧急避撞行人,自主道,纵向制动压力控制加横向前轮转角控制
- weixin小程序项目基于微信小程序的购物系统+php.zip
- weixin小程序项目基于微信的追星小程序+ssm.zip
- weixin小程序项目基于微信的设备故障报修管理系统设计与实现+ssm.zip
- weixin小程序项目基于微信的原创音乐小程序的设计与实现+ssm.zip
- weixin小程序项目基于Vue.js的校园防疫微信小程序开发+ssm.zip
资源上传下载、课程学习等过程中有任何疑问或建议,欢迎提出宝贵意见哦~我们会及时处理!
点击此处反馈


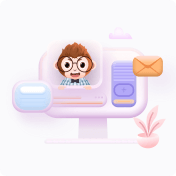