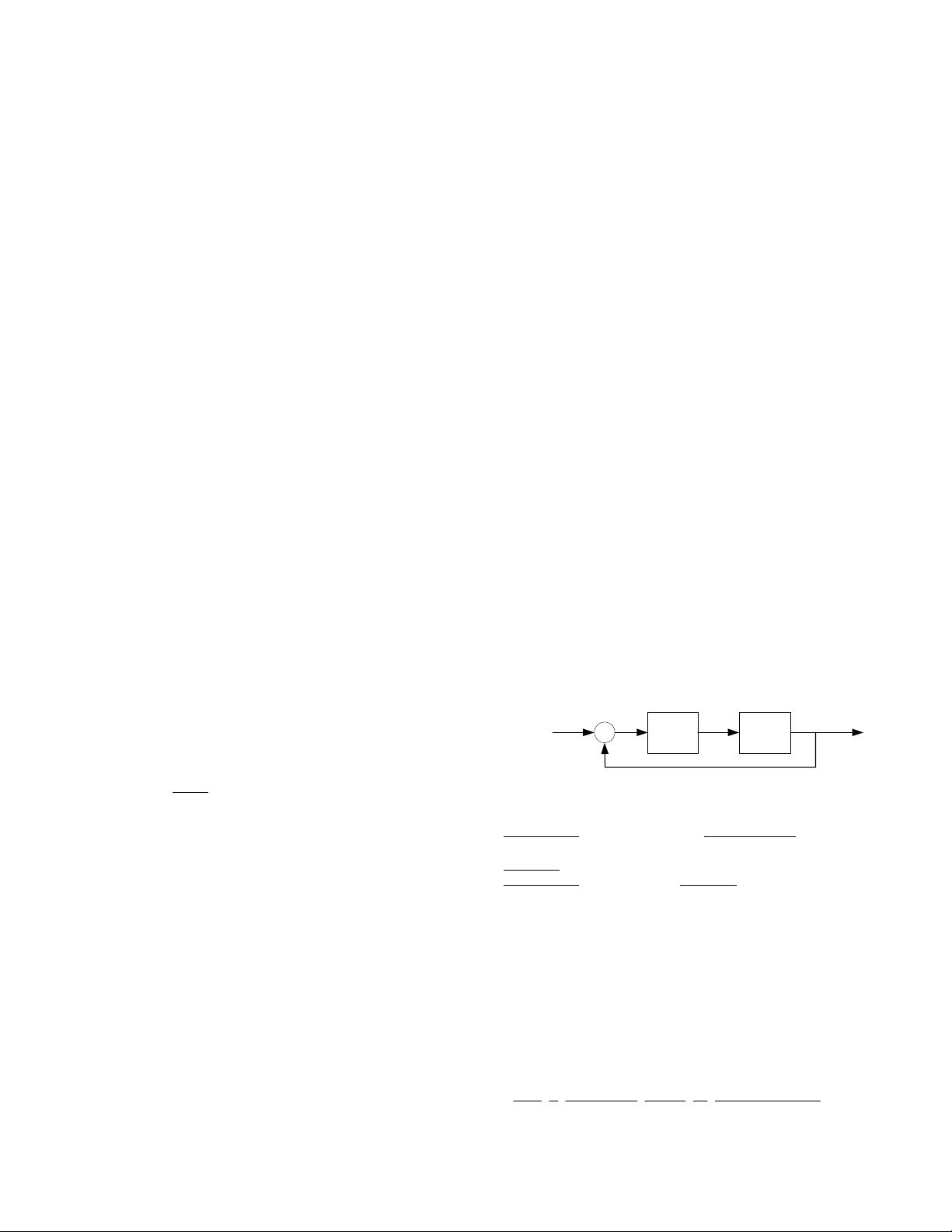
Scaling and Bandwidth-Parameterization Based
Controller Tuning
Zhiqiang Gao
Dept. of Electrical and Computer Engineering
Cleveland State University, Cleveland, Ohio 44115
Abstract: A new set of tools, including controller scaling,
controller parameterization and practical optimization, is
presented to standardize controller tuning. Controller scaling is
used to frequency-scale an existing controller for a large class of
plants, eliminating the repetitive controller tuning process for
plants that differ mainly in gain and bandwidth. Controller
parameterization makes the controller parameters a function of a
single variable, the loop-gain bandwidth, and greatly simplifies
the tuning process. Practical optimization is defined by
maximizing the bandwidth subject to the physical constraints,
which determine the limiting factors in performance.
Collectively, these new tools move controller tuning in the
direction of science.
Keywords: Tuning, PID, Scaling, Auto-Scaling, Auto-Tuning,
Adaptive Self-Tuning, Gain-Scheduling, Disturbance Observer,
Computer Aided Controller Design
I.
Introduction
The proportional-integral-derivative (PID) controller, first
proposed by N. Minorsky in 1922 [1], is used in over 90% of
current industrial control applications [2]. In addition, the
controller parameters are still determined by rules of thumb, such
as look-up tables [3].
Classical control theory has successfully provided the analysis
and design tools for single-input single-output (SISO), linear,
time-invariant systems, since the 1940s. The PID design
approach moved from empirical (i.e., ad hoc tuning methods such
as Ziegler and Nichols tuning tables [3]) to analytical (i.e., pole
placement, frequency response). In particular, the frequency
response-based methods (Bode and Nyquist plots, stability
margins, lead-lag compensators) have proved to be especially
useful in solving control problems.
Historically, determining controller parameters to meet design
specifications (tuning
), rather than the design of the controller
itself, has been the main concern in industry. Most industrial
plants are inherently stable and consist of SISO subsystems.
Simple PID controllers implemented in a digital form can usually
meet the performance needs. But the problem of tuning has
hardly received much attention in the existing control theory. The
variety of ad-hoc tuning algorithms in industrial control products
shows the lack of in-depth understanding of the problem and the
need for further research.
The PID gains are commonly “tuned” on a trial-and-error basis in
practice. A general lack of knowledge regarding the relationship
between “design objectives” and “practical performance
measures” makes the use of well-known design techniques such
as Root Locus (pole-placement) and linear optimal control
difficult. For example, in pole-placement design, the objective is
to place the closed-loop poles at given locations, based on the
understanding of how the location of poles affects the transient
response of a system. Although the transient response is usually
an important design consideration, it is not the only issue in pole-
placement methods with which to contend. The pole-placement
method is ill-equipped to handle other common design
specifications including disturbance rejection, noise sensitivity,
stability margins, and smoothness of the control signal.
This lack of design insight leads to the heuristic nature of the
tuning methods implemented in industry. Furthermore, the
practice of control design and tuning tended in the direction of art
rather than science. This paper presents a comprehensive
approach that moves control design and tuning in the direction of
science.
The paper is organized as follows. Controller scaling is
introduced in Section II. Parameterization and optimization of
model-based controllers are discussed in Section III. Design,
parameterization, and optimization of a model-independent
controller design method are discussed in Section IV. Finally,
some concluding remarks are given in Section V.
II. Controller Scaling
A controller is generally not “portable”, i.e., a controller designed
for one plant is usually not applicable to another plant. The
objective of controller scaling is to make a good controller
“portable”, much like the filter design. With the bandwidth, pass
band, and stop band requirements given, the filter design is
straightforward. First, a unit bandwidth filter, such as an nth
order Chebeshev filter H(s), is found that meets the pass band and
stop band specifications; then it is frequency scaled by ω
0
to
achieve the desired bandwidth of ω
0
. It is shown in this section
that the controller design can be performed similarly.
2.1 Frequency Scale and Time Scale
Consider a unit feedback control system with the plant G
p
(s) and
the controller G
c
(s), as shown in Figure 2.1. Assume that G
c
(s)
was designed for desired command following, disturbance and
noise rejection, and stability robustness. Now, consider a similar
class of plants G
p
(s/ω
p
), for any given
ω
p
. Can a controller be
found without a repetition of the tedious loop shaping design
process?
(s)
-
(s)
r
ye
reference
input
output
G
c
G
Figure 2.1 Feedback Control Configuration
Definition2.1
: Denote
ω
p
as the frequency scale of the plant
G
p
(s/
ω
p
) with respect to G
p
(s), and
τ
p
=1/
ω
p
, the corresponding
time scale
.
Definition2.2
: Denote k as the gain scale of the plant kG
p
(s) with
respect to G
p
(s).
The differences in many industrial control problems can be
described in terms of the frequency and gain scales defined here,
such as the temperature processes with different time constants (in
first-order transfer functions), motion control problems with
different inertias, motor sizes and frictions.
The use of the scales allows the development of a generic solution
for a class of problems. Any linear time-invariant plant, strictly
proper and without a finite zero, can be reduced to one of the
following forms
2232
12
11 1 1 1 1
, , , , , , ...
121s(s+1)s 1sss s ss s
ξξξ
+++ +++
(2.1)
0-7803-7896-2/03/$17.00 ©2003 IEEE 4989
Proceedings of the American Control Conference
Denver, Colorado June 4-6, 2003
评论0