没有合适的资源?快使用搜索试试~ 我知道了~
离线编程技术在机器人点焊项目中的应用.doc
1.该资源内容由用户上传,如若侵权请联系客服进行举报
2.虚拟产品一经售出概不退款(资源遇到问题,请及时私信上传者)
2.虚拟产品一经售出概不退款(资源遇到问题,请及时私信上传者)
版权申诉
0 下载量 149 浏览量
2023-07-13
21:20:58
上传
评论
收藏 1.89MB DOC 举报
温馨提示
离线编程技术在机器人点焊项目中的应用是一个关键的技术手段,它极大地提高了焊接机器人的工作效率和灵活性。焊接机器人,特别是点焊机器人,广泛应用于汽车制造业,以满足批量生产、高效和质量一致性的需求。离线编程技术的发展和完善,解决了传统现场示教方式中调试时间长、效率低下的问题。 离线编程技术首先在项目规划阶段就发挥了重要作用。通过软件环境,可以在投资前评估项目可行性,确定所需机器人数量和是否需要行走机构。根据焊钳重量和工件尺寸,选择合适的机器人型号,并利用仿真软件确定机器人与工件的最佳安装位置,避免现场示教时可能出现的可达性问题。 焊钳选型和焊点可达性验证是另一个关键环节。以前依赖于经验分析和标准件,但离线编程允许对每个焊点进行验证,确保焊钳无干涉并能适应不同工件,减少现场修改的困扰。通过定制非标准焊钳,可以更精确地匹配工件,提高焊接质量和效率。 路径优化是离线编程的一大优势。在计算机上,可以轻松调整机器人的焊点顺序,找到最优路径,减少姿态变换次数,同时避免机器人间的干涉,提高生产节拍。这在实际操作中可能因为时间限制难以实现,但在离线环境中可以多次尝试以达到最佳效果。 干涉区设置是多机器人协作时必须考虑的因素。通过离线编程,可以预先设定安全的机器人工作路径,避免因故障导致的碰撞事故。例如,通过优化路径,使得机器人在特定时间内避免同时进入干涉区,提高生产安全性。 离线编程技术的应用降低了首钢莫托曼机器人有限公司点焊项目的调试时间和成本,提高了工作效率,减少了错误和事故的发生。它使得复杂的焊接任务得以预先规划和优化,确保机器人在实际生产中的顺畅运行,提升了整体的生产效率和产品质量。这种技术的成熟和发展,无疑为现代汽车制造中的自动化焊接工艺带来了革命性的改变。
资源推荐
资源详情
资源评论
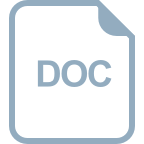
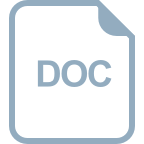
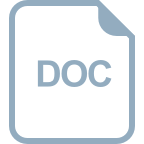
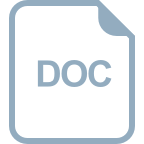
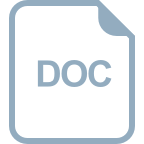
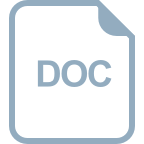
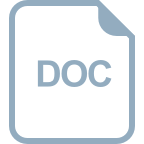
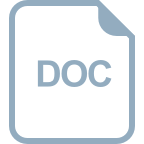
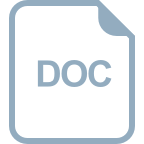
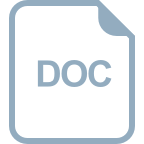
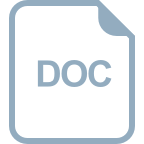
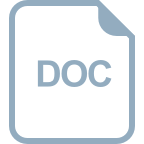
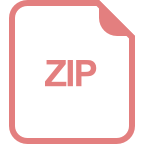
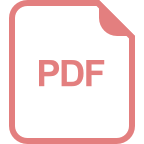
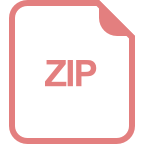
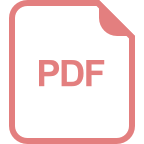
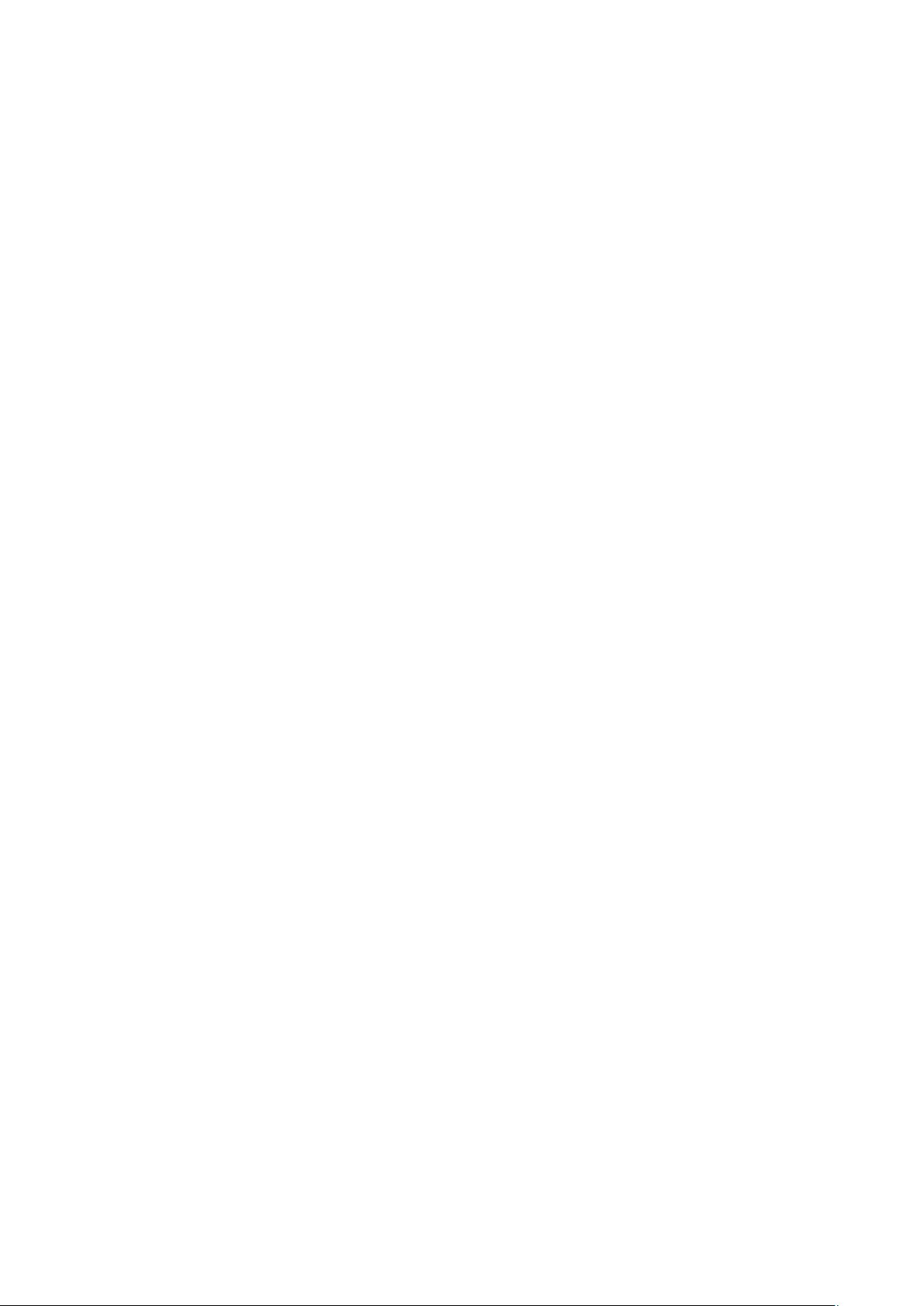
离线编程技术在机器人点焊项目中的应用
焊接机器人是在工业机器人基础上发展起来的先进焊接设备,是从事焊接(包括切割
与喷涂)的工业机器人,主要用于工业自动化领域,其广泛应用于汽车及其零部件制造、摩
托车、工程机械等行业,在汽车生产的冲压、焊装、涂装、总装四大生产工艺过程都有广泛
应用,其中应用最多的以弧焊、点焊为主。近年来,汽车制造的批量化、高效率和对产品质
量一致性的要求,使机器人生产方式在汽车焊接中获得了大量应用。而汽车制造和汽车零部
件生产企业中的焊接机器人成为工业机器人的最主要用户。汽车工业中车身焊装的主要工序
是点焊和弧焊,据统计点焊占 95%。随着焊接机器人的大量应用,各厂商面临着如何提高
其工作效率和使其发挥更大的作用的问题,而机器人的灵活性和智能性很大程度上取决于机
器人的编程能力,在这种需求下,机器人离线编程技术得到了发展和完善,目前机器人离线
编程技术由于其具有编程不影响机器人工作并可通过仿真试验程序以及能够实现复杂运动
轨迹的编程等诸多优点,以及成为机器人研究领域的一大热点。
本文总结了离线编程技术在首钢莫托曼机器人有限公司点焊项目中的应用。离线编程
技术推广之前,首钢莫托曼公司点焊项目的程序编制和示教工作都在现场进行,包括工具尖
端点校准、程序流程编制、干涉区设置、再现检验、测试节拍等,而这些工作是一个循环往
复、不断优化的过程,尤其在多台机器人协同作业的工作站,这样的作业模式占用了大量调
试时间。为解决这一问题,首钢莫托曼公司从 05 年开始研究离线编程技术,以后逐步应用
到具体项目之中,通过不断积累经验,完善提高,使这一技术日趋成熟。
具体应用
从点焊项目的前期准备到具体实施,离线编程技术就在发挥着重要的作用,具体应用
如下:
1、 机器人选型和位置
离线编程技术能够在资本投资之前,鉴别项目是否可行。首先可以在软件环境中确定
项目方案,例如一个工作站需要几台机器人来完成点焊工作,机器人是否需要有行走机构,
等等。总体方案确定之后,可以根据焊钳重量、工件大小确定点焊机器人选型。借助仿真软
件还可以确定机器人与工件之间的安装位置,包括确定机器人底座高度,机器人与工件之间
距离。图 1 中一台点焊机器人需要兼顾三套工件,在确定夹具位置时,首先打开仿真软件自
带的可达性显示功能,图中浅黄色的部分即为机器人可达到的区域,以此为参考初步布置工
件位置。当焊钳确定之后,再逐一验证工件上焊点的可达性,确定工件的最终位置。这样的
前期工作可靠性很高,不会出现由于机器人和工件位置布置不合理,而造成现场示教时焊点
无法达到的事件发生。
资源评论
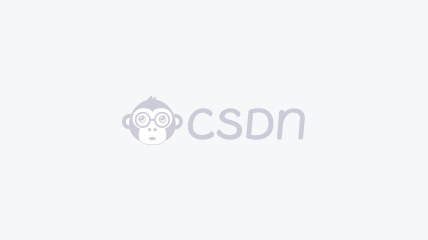

老帽爬新坡
- 粉丝: 92
- 资源: 2万+

下载权益

C知道特权

VIP文章

课程特权

开通VIP
上传资源 快速赚钱
我的内容管理 展开
我的资源 快来上传第一个资源
我的收益
登录查看自己的收益我的积分 登录查看自己的积分
我的C币 登录后查看C币余额
我的收藏
我的下载
下载帮助

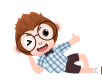
最新资源
资源上传下载、课程学习等过程中有任何疑问或建议,欢迎提出宝贵意见哦~我们会及时处理!
点击此处反馈


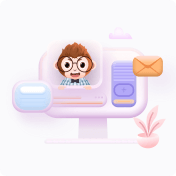
安全验证
文档复制为VIP权益,开通VIP直接复制
