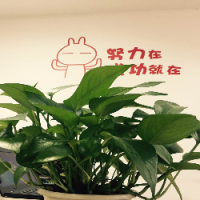

结冰架构
- 粉丝: 902
- 资源: 28万+
最新资源
- nuget 库官方下载包,可使用解压文件打开解压使用
- 非wine、原生Linux迅雷安装包deb文件,支持Ubuntu、UOS统信、深度Deepin、LinuxMint、Debain系通用
- KUKA机器人安装包,与PROFINET软件包
- 船舶燃料消耗和二氧化碳排放分析数据集,燃料消耗和碳排放关联分析数据
- req-sign、bd-ticket-ree-public加密算法(JS)
- 全自动批量建站快速养权重站系统【纯静态html站群版】:(GPT4.0自动根据关键词写文章+自动发布+自定义友链+自动文章内链+20%页面加提权词)
- 串联式、并联式、混联式混合动力系统simulink控制策略模型(串联式、并联式、混联式每个都是独立的需要单独说拿哪个,默认是混联式RB) 有基于逻辑门限值、状态机的规则控制策略(RB)、基于等效燃油
- 法码滋.exe法码滋2.exe法码滋3.exe
- python-geohash-0.8.5-cp38-cp38-win-amd64
- Matlab根据flac、pfc或其他软件导出的坐标及应力、位移数据再现云图 案例包括导出在flac6.0中导出位移的fish代码(也可以自己先准备软件导出的坐标数据及对应点的位移或应力数据,可根据需
资源上传下载、课程学习等过程中有任何疑问或建议,欢迎提出宝贵意见哦~我们会及时处理!
点击此处反馈


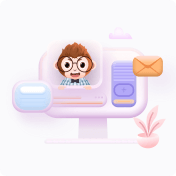