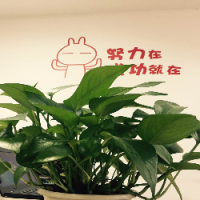

结冰架构
- 粉丝: 921
- 资源: 28万+
最新资源
- Fluent UDF编译与动态链接库调用配置指导-基于C/C++环境的应用与优化
- 基于宾汉姆流体粘度空间衰减的COMSOL三维离散裂隙恒压注浆模型研究,COMSOL 三维离散裂隙注浆模型 基于粘度空间衰减的宾汉姆流体注浆 裂隙采用随机分布的圆盘模型,恒压注浆 ,COMSOL
- 西门子PCS7 CFC常用功能及操作
- 伺服驱动器FPGA架构实现电流环、速度环与位置环等功能的优化方案,跨平台移植便捷,研究价值高,伺服驱动器,你还在为伺服驱动器 FPGA架构苦恼吗,本方案FPGA代码实现电流环 速度环 位置环
- unity转taptap登录、合规验证、成就三个插件4.5.2版本
- 基于欧姆龙CJ CP程序,解析全自动电池注液封装机控制系统设计与应用 涵盖IO模块控制、四轴模块轴控制、温控表读写及多工位转盘控制的全方位应用,omron欧姆龙CJ CP程序 欧姆龙CJ2M-CPU
- 基于PI控制器的单相逆变器闭环控制模型:电压电流双环控制实现优质波形输出及精准跟随matlab Simulink Plecs环境,基于PI控制器的单相逆变器闭环控制模型,采用电压电流双环控制 波形输
- Nacos-Server-2.5.0.zip
- L基于JAVA的网络通讯系统设计与实现(源码+系统+论文).rar
- 西门子S7-200SMART PLC在污水处理系统案例中的应用:大厂技术与国企项目的协同实践,PLC案例 污水处理系统 - 污水处理项目 某大厂技术给某国企做的污水处理项目,程序规范,图纸清晰,具有很
- Screenshot_20250122_092203.jpg
- PCS7 CFC模拟量监视块 MonAnL和MonAnS对比
- 基于核仁理论的混合能源联合外送协调调度与利润分配策略研究,1关键词:合作博弈;核仁法;混合能源;联合外送;经济运行;利润分配;matlab程序 2参考文献:大规模多源联合外送协调调度中基于核
- 基于核仁理论的三方联合运行协调调度与利润分配策略在混合能源联合外送中的应用matlab求解,1关键词:合作博弈;核仁法;混合能源;联合外送;经济运行;利润分配;matlab程序 2参考文献:
- 基于STM32F107串口转网络模块的设计与实现:UART TCP/IP以太网关源码全集,包括AD10 PCB与Keil MCU工程及VC6上位机源码,支持学习与生产 ,串口转网络模块源码,uart
- clutter-tests-1.26.2-2.el7.x64-86.rpm.tar.gz
资源上传下载、课程学习等过程中有任何疑问或建议,欢迎提出宝贵意见哦~我们会及时处理!
点击此处反馈


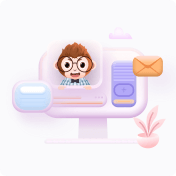