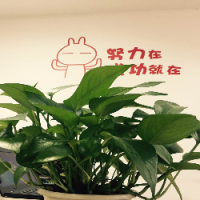

结冰架构
- 粉丝: 917
- 资源: 28万+
最新资源
- MATLAB代码:基于储能电站服务的冷热电多微网系统双层优化配置 关键词:储能电站 共享储能电站 冷热电多微网 双层优化配置 参考文档:《基于储能电站服务的冷热电多微网系统双层优化配置》完全复
- CarSim or TruckSim与Simulink联合仿真,使用键盘控制车辆加速,减速,转向,包含前进与后 档位切,支持自定义按键功能,支持拓展 提供carsim参数配置文件,导入即可运行 提供s
- COMSOL:AlGaAs纳米天线倍频产生(二次谐波非线性效应SHG)三维模型
- 内容介绍:考虑风光不确定性的微电网优化,机会约束描述风光不确定性,采用概率序列处理不确定问题 代码来源:原作者,非倒卖 代码说明:该代码主要贡献为不确定性处理和优化,可供大家学习参考
- 电动汽车 双层优化 选址定容 输配协同 时空优化 MATLAB代码:基于双层优化的电动汽车优化调度研究 参考文档:考虑大规模电动汽车接入电网的双层优化调度策略 仿真平台:MATLAB+CPLEX
- 基于拉丁超立方抽样的风,光,负荷场景生成方法 风电功率场景生成 ,光伏功率场景生成,负荷场景生成 通过后向场景削减BR得到典型场景及其概率 提供参考文献,完美复现 语言:MATLAB
- 西门子博途热力发电厂汽轮机控制系统程序画面案例,采用西门子S7-1516cpu,画面采用经典WINCC7.5 文件内容包含工艺流程图,电仪设计EPLAN图,及控制逻辑等 博图版本V16
- 51单片机PID法设计的开关电源Proteus仿真 功能描述如下: 1、220交流电输入整流滤波得到18 V直流,通过7805得到5v直流电给单片机供电; 2、18 V直流电经过开关变电路(buck
- 通过node Red的OPC UA节点,使用OPC UA server节点建立服务,量NX MCD作为客户端实现数据的交互 node Red+NX MCD轻松实现可视化界面的开发,实现远程控制,数据
- IM即时通讯APP源码搭建语音视频聊天交友软件
- Carsim和simulink联合仿真车辆状态估计 估计的状态为:横摆角速度,质心侧偏角,纵向车速,侧向车速 先基于滑模观测器SMO估计轮胎的纵向力和侧向力 ,再基于无迹卡尔曼UKF和容积卡尔曼CKF
- 三菱Q系列程序 三菱Q06UDV程序,搭配三菱MR-JE伺服,QD77MS16运动控制模块,QD70P8运动模块控制24轴运动,QX42.QY42P等输入输出模块 全自动iPad撕胶贴二维
- 负荷需求响应,matlab 在基于价格的需求侧管理模型研究中,首要任务便是建立负荷对价格的响应模型 有的文献中建立了价格型需求响应功率对电价的响应模型,认为两者之间是简单的线性关系 也有文献忽略了
- BYVIN 比德文知名厂家电动四轮车控制器代码,包含PCB文件,pdf原理图,代码齐全,风格很好
- 质子交膜燃料电池pemfc热管理水管理进气控制 固体氧化物燃料电池sofc 模糊控制,pid控制,模糊pid控制 自抗扰控制 bp-pid rbf-pid ga-pid pso-pid matlab
- 利用最小支持向量机LSSVM做拟合预测建模,数据要求是多列输入单列输出做拟合预测建模,程序内注释详细,直接替数据就可以用
资源上传下载、课程学习等过程中有任何疑问或建议,欢迎提出宝贵意见哦~我们会及时处理!
点击此处反馈


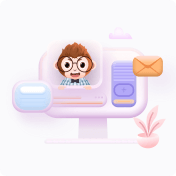
- 1
- 2
前往页