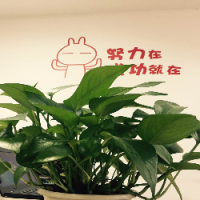

结冰架构
- 粉丝: 917
- 资源: 28万+
最新资源
- 基于fpga的交通灯设计,要求:A通道绿灯亮30S,黄灯亮5S,左拐灯亮15S,黄灯亮5S,这个过程中B通道一直亮红灯,之后A通道亮红灯,B通道绿灯亮40S,之后黄灯亮5S,之后左拐灯亮15S,之后黄
- 基于阶梯碳交易成本的含电转气-碳捕集(P2G-CCS)耦合的综合能源系统低碳经济优化调度,采用(Matlab+Yalmip+Cplex) 考虑P2G设备、碳捕集电厂、风电机组、光伏机组、CHP机组、燃
- 计及阶梯碳交易成本+多元储能(电储能、氢储能、气储能、热储能)+综合能源系统IES联合低碳优化调度(用Matlab+Yalmip+Cplex) 考虑机组和设备:热电联产机组、燃气机组、甲烷反应生成设备
- (OC)多代理实现 运行看效果
- visual basic 6 安装光盘文件
- 双碳+24小时分时综合能源系统低碳优化调度(用Matlab+Yalmip+Cplex) 包含新能源消纳、热电联产、电锅炉、储能电池、天然气、碳捕集CCS、计及碳交易市场等综合元素,实现系统总运行成本最
- 基恩士KV5500程序 基恩士KV5500,威伦通触摸屏,搭载KL-N20V.远程IO模块,KV-MC02V凸轮定位模块,KV-L2*V串行通信模块 全自动锂电池注液机 伺服轴进行位置控制,等
- 电力系统(30节点)机组组合优化调度 基于Matlab、yalmip、cpelx求解最优 针对机组组合问题,提出一种混合整数线性模型,相比传统方法,采用二进制变量和约束,节省计算时间优化收敛速度 为
- 基于门控循环单元GRU做多个特征变量输入,单个因变量输出的拟合预测建模 程序内注释详细,可学习性强 程序直接替数据就可以使用,不会替数据的可以免费指导替数据 程序语言是matlab的,需求版本是
- 图像处理领域的频域处理和复原:运动模糊和失焦模糊修复研究
- dmidecode-3.6
- 多目标遗传算法电力系统系统分布式电源选址定容(matlab程序) 基于IEEE14节点的电力系统多目标优化的遗传算法分布式电源选址定容 对于网损、容量和、电压稳定值的目标优化出来的选址定容 分为有DG
- Simulink 车用永磁同步电机弱磁控制 基于矢量控制 FOC
- GAPSO-LSTM,遗传粒子群优化算法来优化LSTM网络做预测,预测精度高于普通的PSO-LSTM 这里把遗传算法跟粒子群优化算法结合,指的不是用遗传算法来优化PSO的参数,而是解决PSO的容易收
- matlab实现PID控制四旋翼无人机综述模型-PID-四旋翼无人机-matlab
- 2024后台组保姆级学习路线.pdf
资源上传下载、课程学习等过程中有任何疑问或建议,欢迎提出宝贵意见哦~我们会及时处理!
点击此处反馈


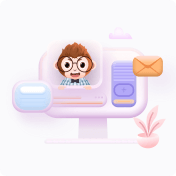