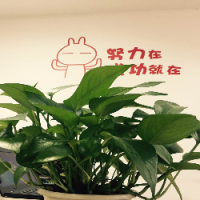

结冰架构
- 粉丝: 921
- 资源: 28万+
最新资源
- 绩效考核管理制度.doc
- 企业绩效考核制度及方案(实例).doc
- 长虹集团绩效管理手册.doc
- 绩效考核制度.doc
- 美的干部绩效考核办法.doc
- 生产型企业绩效考核方案.doc
- 中国联通:绩效管理操作手册.doc
- 公司绩效考核全套流程表格.docx
- 中通关键岗位薪酬设计方案.doc
- “探讨功率因素调节中MPPT和SVPWM技术在三相光伏并网逆变器仿真模型中的应用:精确谐波畸变控制与性能优化”,500kW三相光伏并网逆变器的仿真模型: 1.光伏PV, DC DC采用MPPT最大功率
- buildnumber-maven-plugin-javadoc-1.2-7.el7.x64-86.rpm.tar.gz
- DSP2837系列串口升级方案:基于VS2013的双核与单核升级解决方案及源代码分享,DSP28377D串口升级方案 串口双核升级,上位机采用vs2013开发 稍微修改可支持2837x系列的单、双核
- bwidget-1.9.0-6.el7.x64-86.rpm.tar.gz
- 蓄电池与超级电容混合储能系统的功率分配及SOC管理策略-基于Matlab Simulink仿真模型探究,蓄电池与超级电容混合储能并网matlab simulink仿真模型 (1)混合储能采用低通滤
- byacc-1.9.20130304-3.el7.x64-86.rpm.tar.gz
- 1737485585760.png
资源上传下载、课程学习等过程中有任何疑问或建议,欢迎提出宝贵意见哦~我们会及时处理!
点击此处反馈


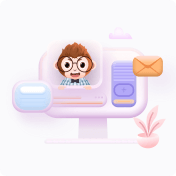