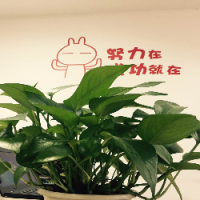

结冰架构
- 粉丝: 945
- 资源: 28万+
最新资源
- 【微信小程序源码】京东首页demo
- 《大闹天宫》动画美术风格中的中国传统元素分析_张星辉.caj
- VCU Simulink需求与功能开发文档:集成档位控制、ON Start启动、上下电管理、扭矩调控、能量优化与滑行回收的全方位控制系统需求说明,VCU Simulink需求与功能开发文档:集成档位控
- 基于COMSOL Multiphysics的三维岩石酸化过程模拟:探讨酸液在碳酸盐岩储层中的流动、传质与反应机制,利用COMSOL Multiphysics模拟三维岩石酸化过程:探讨酸液在碳酸盐岩储层
- 台达DVP PLC与西门子V20变频器通讯程序:可靠控制,自动化调整,接线与设置指南,台达DVP PLC与西门子V20变频器通讯程序:可靠控制,自动化调整,接线与设置指南,台达DVP PLC与3台西门
- 基于Python的Django-vue基于大数据的学习资源推送系统实现源码-说明文档-演示视频.zip
- PHP API 客户端,可让您与 deepseek API 进行交互 deepseek-php-client-2.0.3
- 【微信小程序源码】和茶网
- 自然启发MPPT优化技术,霜冰优化算法RIME在MPPT中对光伏局部遮阴情况的性能提升研究,霜冰算法RIME优化mppt,光伏mppt , 局部遮阴光伏mppt 2023年,H Su等人受到自然界霜冰
- 使用 PHP Deepseek 实现问答 ask-deepseek
- COMSOL Multiphysics中的comsol支架静态分析:基本原理、操作与结果分析,COMSOL Multiphysics中的comsol支架静态分析:基本原理、操作与结果分析,comsol
- 基于Python的Django-vue基于大数据的银行信用卡用户的数仓系统源码-说明文档-演示视频.zip
- 翱捷功能机常见空间问题的解决
- 西门子博途1500双驱同步编程实例分享,结构化编程、伺服同步运行、多用户权限登录,开发者必备的学习参考(版本v16),西门子博途V16全新双驱同步与三轴码垛程序:结构化编程框架,多用户权限控制,高值学
- DotSpatial库学习
- Delphi 12.5 控件之delphi实现腾讯签名算算法源代码.rar
资源上传下载、课程学习等过程中有任何疑问或建议,欢迎提出宝贵意见哦~我们会及时处理!
点击此处反馈


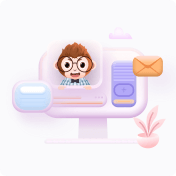