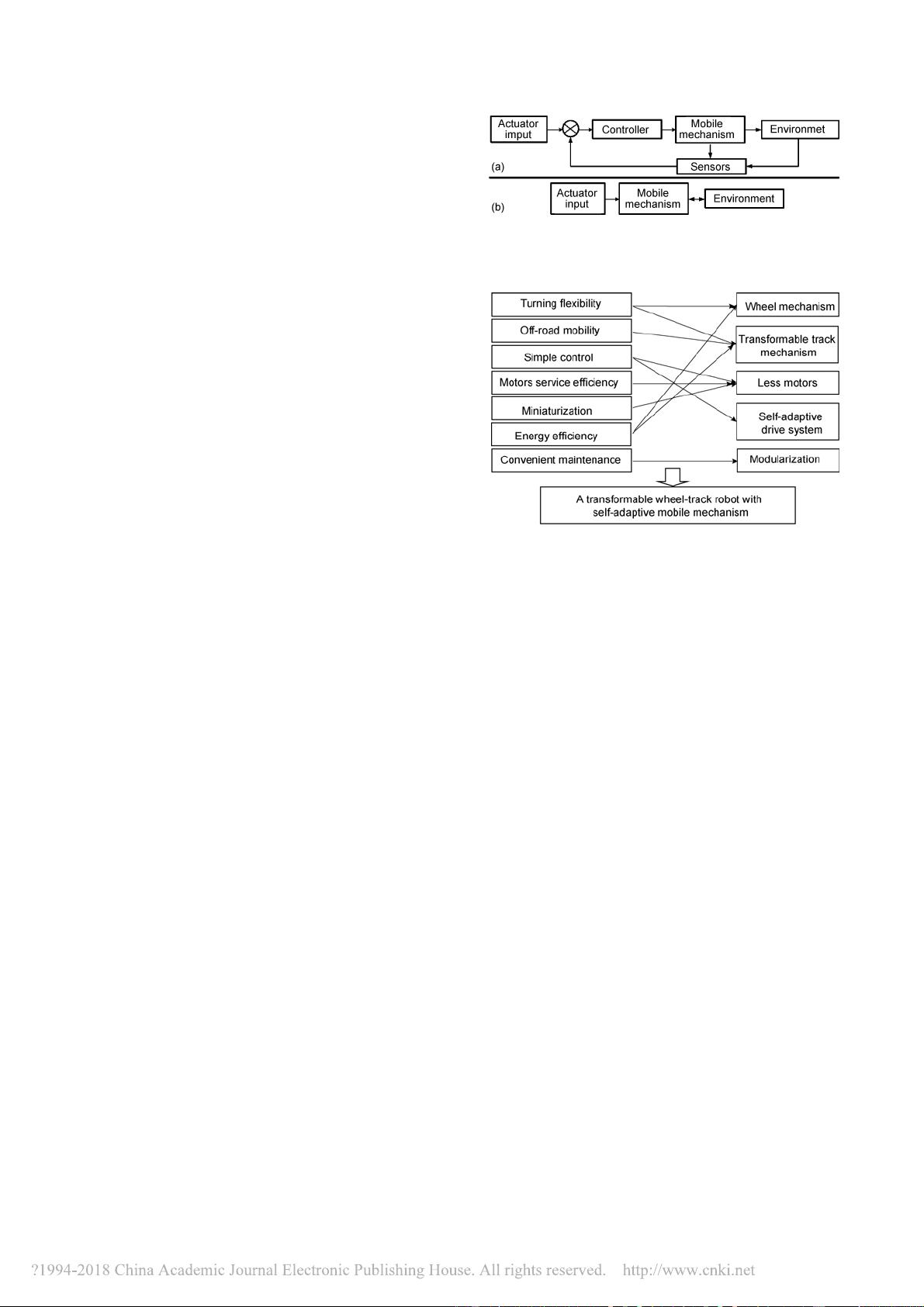
Li Z Q, et al. Sci China Tech Sci March (2011) Vol.54 No.3 611
adjust the contact area between the mobile mechanism and
the ground to provide the proper movement option. There-
fore, they generally have prominent adaptability and low
energy consumption. For example, CALEB-2 [1], VSTR [2,
3], ROBHAZ-DT [4–6], Single-Tracked [7], and VGTV [8]
are some typical robots that have been developed with
T-track mechanisms. AZIMUT [9], HYBRID Robot [10],
the wheel-track-leg Robot [11], and the miniature
wheel-track-leg mobile robot [12] are typical examples of
hybrid mechanism robots.
For the above robots, most have many degrees of free-
dom (DOF) and adopt active drive systems of the type de-
scribed in Figure 1(a). Each DOF of the mobile mechanism
is driven directly by a motor. That is, they need many mo-
tors. When the robot moves over rough terrain, it has to
collect sufficient information about its environment for the
control system by sensors. Based on the analysis of this
information, the robot can use its own control system to
drive every DOF to change its locomotion mode or posture
to adapt itself to the rough terrain [14, 15]. Therefore, many
high-accuracy sensors are mounted on the robot However,
the feedback information varies with changes in the terrain,
adding complexity to the robot’s control system. Meanwhile,
the control system has to spend much more time in deter-
mining proper locomotion mode or posture of the mobile
mechanisms. As a result, the robot may experience a
time-lag in its motions when it meets obstacles and negoti-
ates them.
Based on the above considerations and the analysis of the
constraint relation between the mobile mechanism and the
ground, a transformable wheel-track robot (NEZA-I) with
self-adaptive mobile mechanisms is proposed and devel-
oped. As shown in Figure 2, the robot should possess the
following features:
1) Mobile mechanism of the robot can move with differ-
ent locomotion modes and postures to adapt itself to the
complex and unpredictable environments.
2) The drive system of the robot ensures that the robot
has the self-adaptability to navigate in unstructured terrains.
It can also simplify the robot’s control algorithms and make
the robot’s motion less dependent upon its control system
while the robot adjusts its locomotion mode and posture.
Meanwhile, it can also make motor more efficient.
In this paper the mechanism structure, the self-adaptive
drive system, and the locomotion mode and posture of the
NEZA-I robot are briefly presented, the kinematic relation
among parts of the TWT unit is analyzed, and the math-
ematic model of the constraint relation between the mobile
mechanism and the ground is set up for the NEZA-I robot to
go through some typical unstructured environments. The
mechanism parameters, which influence the self-
adapta-
bility of the robot, are analyzed and optimized. Finally,
experiments are introduced to validate the robot’s mobility
and verify the reasonability of the MGCR model and the
analysis method for mechanism parameters.
Figure 1 Design concept of the drive system of NEZA-I robot. (a) A
typical active drive system; (b) proposal for a self-adaptive drive system.
Figure 2 Design concept for NEZA-I.
2 Transformable wheel-track robot
As shown in Figure 3, the robot consists of a control system
unit, double symmetric TWT units, and a rear-wheel unit.
Each TWT unit is composed of a transformable track
mechanism and a drive wheel mechanism. The rear-wheel
unit is fixed on the rear of the control box and is composed
of two rear frames, two rear springs, two rear wheels, and
two L-links. For the NEZA-I robot, the TWT unit is its
main mobile mechanism and the rear-wheel unit is a mobil-
ity assistant mechanism. Driven by only one servomotor,
each TWT unit can efficiently move over different unstruc-
tured terrains by selecting the locomotion mode between
track mode and wheel mode, and autonomously adjusting
the locomotion mode and track configuration according to
changes in the terrain. When the robot encounters a high
obstacle, the rear-wheel mechanism can support the robot to
prevent it from overturning. The rear-wheel mechanism can
also improve performance in negotiating obstacles.
It is thus necessary to design the drive system of mobile
mechanism reasonably since the drive system is an essential
part for the mobile mechanism of the NEZA-I robot. When
the robot goes through the unstructured environment, the
constraint forces from environment that act on the mobile
mechanism varies with the robot’s location. To improve the
motor’s efficiency and to simplify the robot’s control algo-
rithms and make the robot less dependent upon the control
system while the robot adjusts its locomotion mode and
posture, we propose a self-adaptive drive system based on a