
tangtx2021
- 粉丝: 1
- 资源: 2万+
最新资源
- 国际象棋检测7-YOLO(v5至v9)、COCO、CreateML、Darknet、Paligemma、TFRecord数据集合集.rar
- 【一文搞懂:什么是集成学习-原理+python代码】
- 德普微一级代理 DP3145D SOT23-6 USB PD 协议单口控制器
- java毕设项目之学习视频资源库的系统+jsp(完整前后端+说明文档+mysql).zip
- 基于java实现的快速排序代码
- java毕设项目之游泳会员管理系统+vue(完整前后端+说明文档+mysql+lw).zip
- 巨潮资讯网5000只股票orgId-dict加密字典
- java毕设项目之中文学习系统的设计与实现+jsp(完整前后端+说明文档+mysql+lw).zip
- 德普微一级代理 DP021N03FGLI DFN5*6 DPMOS N-MOSFET 30V 180A 1.8mΩ
- java毕设项目之zy+养老服务平台设计+vue(完整前后端+说明文档+mysql+lw).zip
- 【java毕业设计】SpringBoot+Vue幼儿园管理系统 源码+sql脚本+论文 完整版
- 德普微一级代理 DP100N06MGL PDFN3.3*3.3 TRMOS N-MOSFET 60V, 8mΩ, 45A
- mongoose-free-6.9
- dnSpy-net-win32-222.zip
- 国际象棋检测8-YOLO(v5至v9)、COCO、CreateML、Darknet、Paligemma数据集合集.rar
- cvtocc-shanghai.hbm
资源上传下载、课程学习等过程中有任何疑问或建议,欢迎提出宝贵意见哦~我们会及时处理!
点击此处反馈


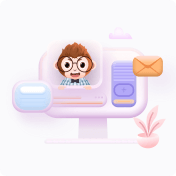