
sqskdjj
- 粉丝: 0
- 资源: 4万+
最新资源
- Python asdasdas
- 基于NGSIM数据集的驾驶风格特征提取与高斯聚类分析:从换道工况探究驾驶风格多样性,驾驶风格,高斯聚类,特征提取,NGSIM 利用公开数据集#NGSIM(i-80,US101)中基于道工况的驾驶风格特
- 基于协同过滤的旅游景点与路线推荐系统:个性化推荐、管理功能与Django框架实现 ,旅游景点推荐系统 旅游路线推荐系统 使用基于协同过滤的方法,为用户推荐一座城市的景点或路线,同时实现登陆、查看景点信
- Python自动化办公源码-01批量更改Excel文件中200多个工作表的内容
- PLC三菱FX3U-48MRT控制器资料:STM32F103VET6芯片、多路输入输出、通信接口与指示灯,源码及原理图包含,PLC三菱PLC FX3U-48MRT 源码,原理图,PCBFX3U PL
- 深度学习乐园项目案例分享:A057-PCC Net模型实现行人数量统计
- STM32BMS动力电池管理系统仿真:探究物理模型与多样控制策略的关键技术及应用,STM32bms动力电池管理系统仿真 Battery Simulink电池平衡控制策略模型 动力电池管理系统仿真 BM
- 计算机视觉领域HALCON内存管理和缓存机制详解及其应用
- "C#读写台达PLC源代码详解:寄存器的读写操作、通讯协议详解与寄存器通讯对照表,专为工程师速成参考",C#读写台达PLC源代码,分别操控D、M、X、Y、T寄存器的读写,代码注释详细、分类说明,附带文
- 基于ASPIC开发流程的VCU整车管理控制器策略文档:应用层软件与快速原型开发,VCU整车管理控制器?策略文档,量产车型使用 快速原型开发 整车管理系统策略开发,应用层软件,在车型最新版本软件 按
- 基于粒子群算法的虚拟储能系统集成在智能楼宇微网优化调度中的实现,储能 智能楼宇 采用matlab编程,程序采用粒子群算法,将储能系统集成到楼宇微网优化调度模型中,通过在温度舒适度范围内对楼宇室温进行
- 西门子S-InOrder管理层序:博图V15.1下的控制台与A2伺服驱动器通讯控制程序实现与调试,西门子1200控制台达A2伺服485通讯控制程序,博图V15.1 ,西门子; 1200控制台; 达A2
- Halcon图像处理领域的灰度值插值方法研究及应用
- 基于Simulink仿真的双容水箱恒水位控制系统设计与参数优化研究,双容水箱恒水位控制系统,约8k字 基于SIMULINK仿真环境,在假设双容水箱的数学建模后,采用PID控制算法,分别选用单回路控制
- 基于java+ssm+mysql的仓库管理系统 源码+数据库+论文(高分毕设项目).zip
- 基于java+ssm+mysql的餐厅点餐系统 源码+数据库+论文(高分毕设项目).zip
资源上传下载、课程学习等过程中有任何疑问或建议,欢迎提出宝贵意见哦~我们会及时处理!
点击此处反馈


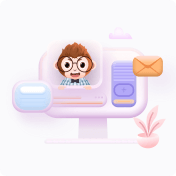