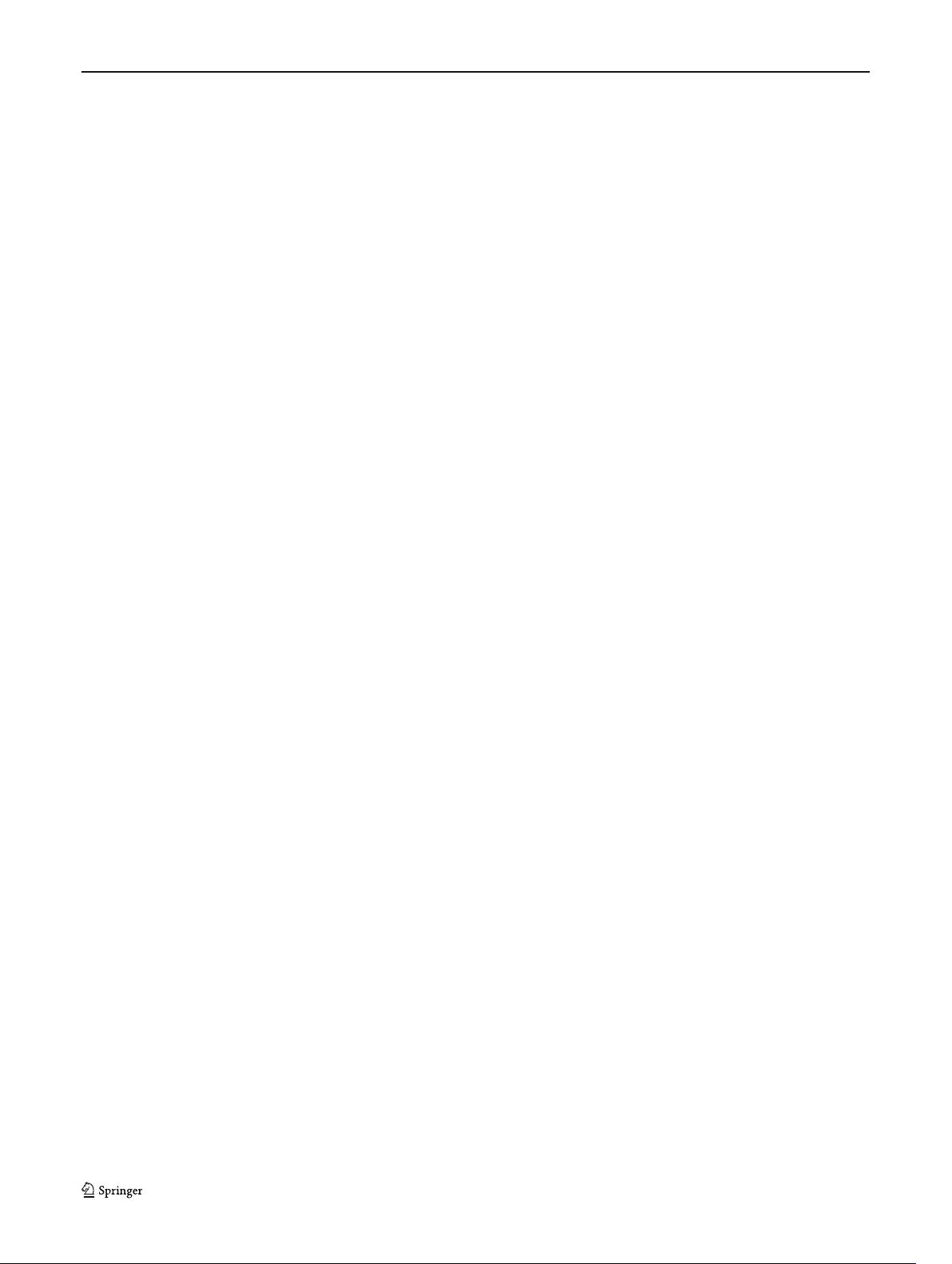
optimal fixture layout design using a rigid body model of the
fixture -workpiece system [1]. DeMeter also used a rigid
body model for the analysis and synthesis of optimal
fixture layouts and m inim um clampi ng force [2]. He
presented a finite element method (FEM) based support
layout optimization proce dure with computationally attrac-
tive qualities [3]. Li and Melko te used a nonline ar
programming method and a contact elasticity model to
solve the layou t optimization problem [4]. Two years later,
they presented a method for determining the optimal
clampin g force for a multiple clamp fixture sub jected to
quasi-static machini ng force [5]. They also presented an
optimal synthesis a pproach of fixture layout and clamping
force that considers workpiece dynamics during machining
[ 6]. A combined fixture layout and clamping force
optimization proce dure was presented. Other researchers
[7, 8] used the FEM for fixture design and analysis. Cai et
al. [9] extended the work of Menassa and De Vries [8]to
include synthesis of fixture layout for sheet metal assembly.
Qin et al. [10] established a n elastic contact model between
clamp and workpiece to optimize the clamping force with
an objective to minimize the position error of the
workpie ce. Deng and Melkote [11] presented a model-
based framework for determining the minimu m required
clampin g force, which ensure s the dynamic stability of a
fixture d workpiece during machining.
Most of the above studies used nonlinear programming
methods, which seldom gave global or near-global opti-
mum solutions. All of the fixture layout optimization
procedures must start with an initial feasible layout. In
addition, solutions obtained from these models are very
sensitive to the initial feasible fixture layout. The problem
of fixture design optimization is nonlinear because there is
no direct analytical relationship between the objective
function and design variables, i.e. between the machined
surface error and the fixture parameters (positions of locator
and clamp, and clamping forces ).
Previou s researchers had shown that genetic algorithm
(GA) was a useful technique in solving such optimiza-
tionproblems.WuandChan[12]usedtheGAto
determine the most statically stable fixture layout. Ishikawa
and Aoyama [13] applied GA to determine the optimal
clampin g condition for an elastic workpiece. Vallapuzha et
al. [14] used spatial coordinates to encode in the GA based
optimization of fixtu re layout. They also presented the
methodology and results of an extensive investigation into
the relative effectiveness of the main competing fixture
optimization methods, which showed that continuous GA
yielded the best quality solutions [15]. Krishnakumar and
Melkote [16] developed a fixture layout optimization
technique that used GA to find the fixture layout that
minimized the deformation of the machined surface due to
clamping and cutting force over the entire tool path.
Locator and clamp positions were specified with node
numbers. Krishnakumar et al. [17] presented an iterative
algorithm that minimized the workpiece elastic deformation
for the entire cutting process by alternative ly varying the
fixture layout and clamping force. Lai e t al. [18] set up an
analysis model that treated locator and clamps as the same
fixture layout elements for the flexible part deformation.
Hamedi [19] discussed a hybrid learning system that us ed
nonlinear FEA with a supportive combination of artificial
neural network (ANN) and GA. The ANN was used to
calculate workpiece maximum elastic deformation, the GA
was used t o determine the optimum clamping forces.
Kumar [20] proposed to combine the GA and ANN to
develop a fixture design system. Kaya [21] used the GA
and FEM to find the optimal locators and clamping
position s in 2D workpie ce and took chip removal effects
into ac count. Zhou et al. [
22] presented a GA based met hod
that optimized fixture layout and clamping force simulta-
neously. Some of the studies did not consider the
optimization of the layout for entire tool path. Some of
the studies used node numbers as design parameters.
Some of the studies addressed fixture layout or c lamping
force optimization methods but not both simultaneously.
And there were few stu dies taking friction and chip
removal into account. The effects of chip removal and
frictional contact cannot be neglected for achievin g a
more realistic and accurate workpiece-fixture layout
verific ation analysis [23], so it is essential to take chip
removal effects and friction effect into account to achieve a
better machining accuracy.
In this paper, the friction and chip removal are taken
into account to achieve the minimum degree of the
maximum deformat ion of the machined surfaces under
clampin g and cutting force and to uniform the deforma-
tion. A multi-objective optimization model is established.
An op timization process based on GA and FEM is
presented to find the optimal fixture layout and clamping
force. Finally, the resu lt of the multi-objective optimiza-
tion model is compared with the single objective
optimization method and the experience method for a low
rigidity workpiece.
3 A multi-objective optimization model for fixture
design
A feasible fixture layout has to satisfy three constraints.
First, the locators and clamps cannot apply tensile forces on
the workpiece. Second, the Coulomb friction constraint
must be satisfied at all fixture-workpiece contact points.
The positions of fixture element-workpiece contact points
must be in the candidate regions. For a problem involving p
fixture element-workpiece contacts and n machining load
Int J Adv Manuf Technol