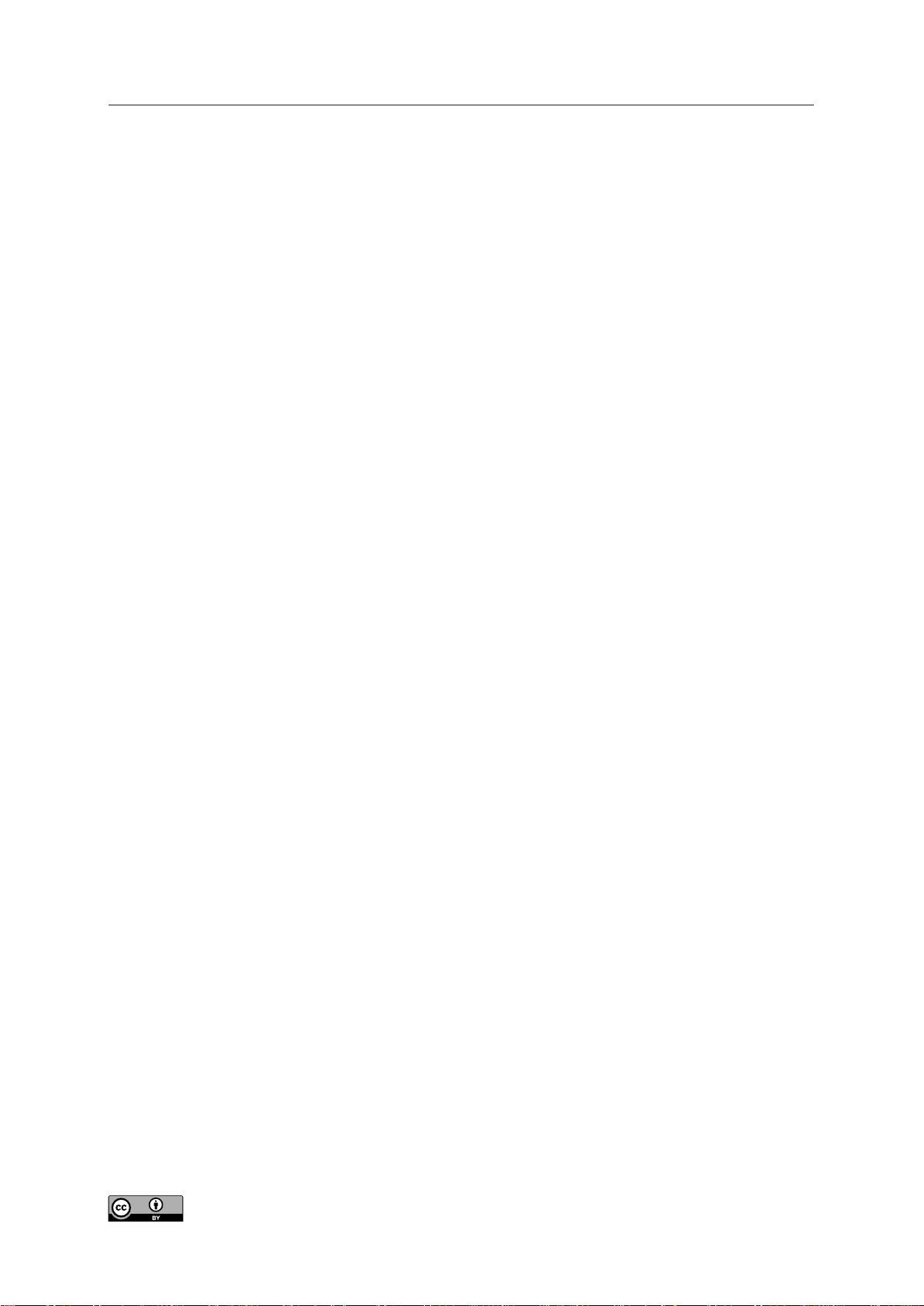
1
Content from this work may be used under the terms of the Creative Commons Attribution 3.0 licence. Any further distribution
of this work must maintain attribution to the author(s) and the title of the work, journal citation and DOI.
Published under licence by IOP Publishing Ltd
1234567890‘’“”
SAMSE IOP Publishing
IOP Conf. Series: Materials Science and Engineering 322 (2018) 072020 doi:10.1088/1757-899X/322/7/072020
Design of PID temperature control system based on STM32
Jianxin Zhang
1,2,3,4,*
, Hailin Li
1,3
, Kai Ma
1,3
, Liang Xue
1,3
, Bianhua Han
1,3
,
Yuemeng Dong
2,3
, Yue Tan
2,3
, Chengru Gu
2,3
1
Tianjin Key Laboratory of Optoelectronic Detection Technology and Systems,
Tianjin Polytechnic University, Tianjin, China
2
Tianjin Key Laboratory of Advanced Electrical Engineering and Energy Technology,
Tianjin Polytechnic University, Tianjin, China
3
Engineering Research Center of High Power Semiconductor Lighting Application
System Education Department, Tianjin Polytechnic University, Tianjin, China
4
State Key Laboratory of Hollow Fiber Membrane Materials and Processes, Tianjin
Polytechnic University, Tianjin, China
*Corresponding author e-mail: assen_zhjx@126.com
Abstract. A rapid and high-accuracy temperature control system was designed using
proportional-integral-derivative (PID) control algorithm with STM32 as micro-
controller unit (MCU). The temperature control system can be applied in the fields
which have high requirements on the response speed and accuracy of temperature
control. The temperature acquisition circuit in system adopted Pt1000 resistance
thermometer as temperature sensor. Through this acquisition circuit, the monitoring
actual temperature signal could be converted into voltage signal and transmitted into
MCU. A TLP521-1 photoelectric coupler was matched with BD237 power transistor
to drive the thermoelectric cooler (TEC) in FTA951 module. The effective electric
power of TEC was controlled by the pulse width modulation (PWM) signals which
generated by MCU. The PWM signal parameters could be adjusted timely by PID
algorithm according to the difference between monitoring actual temperature and set
temperature. The upper computer was used to input the set temperature and monitor
the system running state via serial port. The application experiment results show that
the temperature control system is featured by simple structure, rapid response speed,
good stability and high temperature control accuracy with the error less than ±0.5°C.
1. Introduction
As an important parameter in industrial manufacture [1] and scientific experiment [2], temperature
needs to be measured and controlled rapidly with high accuracy. Otherwise, the distinct temperature
errors will be harmful to the performance and precision of the whole measurement system [3],
especially in the field of modern instrument. For example, it is very important to correctly obtain the
accelerated lifetime prediction [4] and photo-electro-thermal properties [5] of LED light source
through providing a constant temperature environment with high accuracy and rapid response speed.
In another instance, the core parts of fiber optic gyroscope (FOG) is also sensitive to environment
temperature [6], a slight temperature change can cause the zero drift of FOG, so it is necessary to
provide accurate temperature control or temperature compensation [7]. Lots of practical applications
show that a rapid and high-accuracy temperature control system is worthy of further investigation.