
m0_62051506
- 粉丝: 13
- 资源: 6万+
最新资源
- 图书管理系统( Spring+Spring MVC+JdbcTemplate)
- Java毕设项目-基于SSM框架的药房管理系统源码+数据库脚本.zip
- 上市公司研究报告20010101-20240929研究报告标题报告人员关联个股证券关联行业名称 数据来源:基于上市公司公告、年报等相关数据整理计算 数据范围:沪深京上市公司A股,包括主板、中小企业板
- 三相LCL型并网逆变器在dq旋转坐标系下,采用逆变器机侧电感电流反馈有源阻尼+网侧电流反馈控制策略,给出控制参数设计及Simulink仿真模型搭建,参数设计稳定,并网波形质量良好 三相LCL型并网逆
- 计算机体系结构论文格式
- 2-BPC(中国码)电波表对时模拟软件
- Java毕设项目-基于SSM框架的药房管理系统源码+数据库脚本(高分毕设)
- 基于CNN的快速VVC帧间编码方法及其应用与性能提升研究
- 网络安全-渗透攻防知识点面试题整合
- 基于梯度方向的VVC帧内编码中CU划分早终止算法研究与实现
- java图书管理系统(JSP+Servlet)
- 毕业设计基于单片机的室内有害气体检测系统源码+论文(高分毕设)
- 毕业设计 springBoot人力资源管理系统+毕业论文+前后端源代码
- 基于单片机的室内有害气体检测系统源码+论文(高分毕设)
- java图书管理系统-技术栈:JSP+Servlet+Tomcat9.0+IDEA+Mysql
- RBP神经网络PID自适应控制模型(送配套资料) Matlab仿真模型 与传统pid控制器相比,省去pid参数调节 附赠详解资料,包思路讲解,代码分析
资源上传下载、课程学习等过程中有任何疑问或建议,欢迎提出宝贵意见哦~我们会及时处理!
点击此处反馈


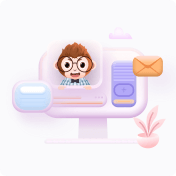