
文档爱好者
- 粉丝: 8
- 资源: 29万+
最新资源
- ks滑块加密算法与源代码
- 医护人员检测23-YOLOv8数据集合集.rar
- 1.电力系统短路故障引起电压暂降 2.不对称短路故障分析 包括:共两份自编word+相应matlab模型 1.短路故障的发生频次以及不同类型短路故障严重程度,本文选取三类典型的不对称短路展开研究
- C#连接sap NCO组件 X64版
- 开源基于51单片机的多功能智能闹钟设计,课设毕设借鉴参考
- 深度强化学习电气工程复现文章,适合小白学习 关键词:能量管理 深度学习 强化学习 深度强化学习 能源系统 优化调度 编程语言:python平台 主题:用于能源系统优化调度的深度强化学习算法的性能比较
- 泰州市2005-2024年近20年历史气象数据下载
- 盐城市2005-2024年近20年历史气象数据下载
- 连云港市2005-2024年近20年历史气象数据下载
- 南通市2005-2024年近20年历史气象数据下载
资源上传下载、课程学习等过程中有任何疑问或建议,欢迎提出宝贵意见哦~我们会及时处理!
点击此处反馈


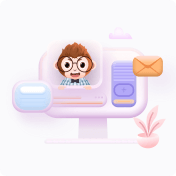