
liulaoshi173
- 粉丝: 0
- 资源: 9万+
最新资源
- 2025年医师定期考核试题库及答案(通用版).docx
- 2025年医师定期考核题库及答案.docx
- 2025年医务人员行为规范与医务礼仪题库及答案(完整版).docx
- 2025年医务人员手卫生规范考试题及答案.docx
- 2025年医务人员手卫生规范考试题(附答案).docx
- 2025年医务人员手卫生规范考试题库(附答案).docx
- 2025年医学基础知识题库及答案(通用版).docx
- 2025年医务人员手卫生规范培训试题及答案.docx
- 2025年医务人员手卫生规范培训考试试题及答案.docx
- 2025年医学基础知识考试题库附含答案.docx
- 2025年医务人员手卫生规范知识题库及答案.docx
- 2025年医学基础知识试题库及答案(通用版).docx
- 2025年医学基础知识考试题库及答案(通用版).docx
- 2025年医学三基考试题库及答案(通用版).docx
- 2025年医学影像检查技术学试题库及答案.docx
- 2025年医用织物管理制度大全.docx
资源上传下载、课程学习等过程中有任何疑问或建议,欢迎提出宝贵意见哦~我们会及时处理!
点击此处反馈


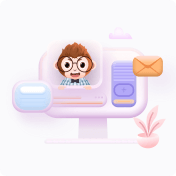