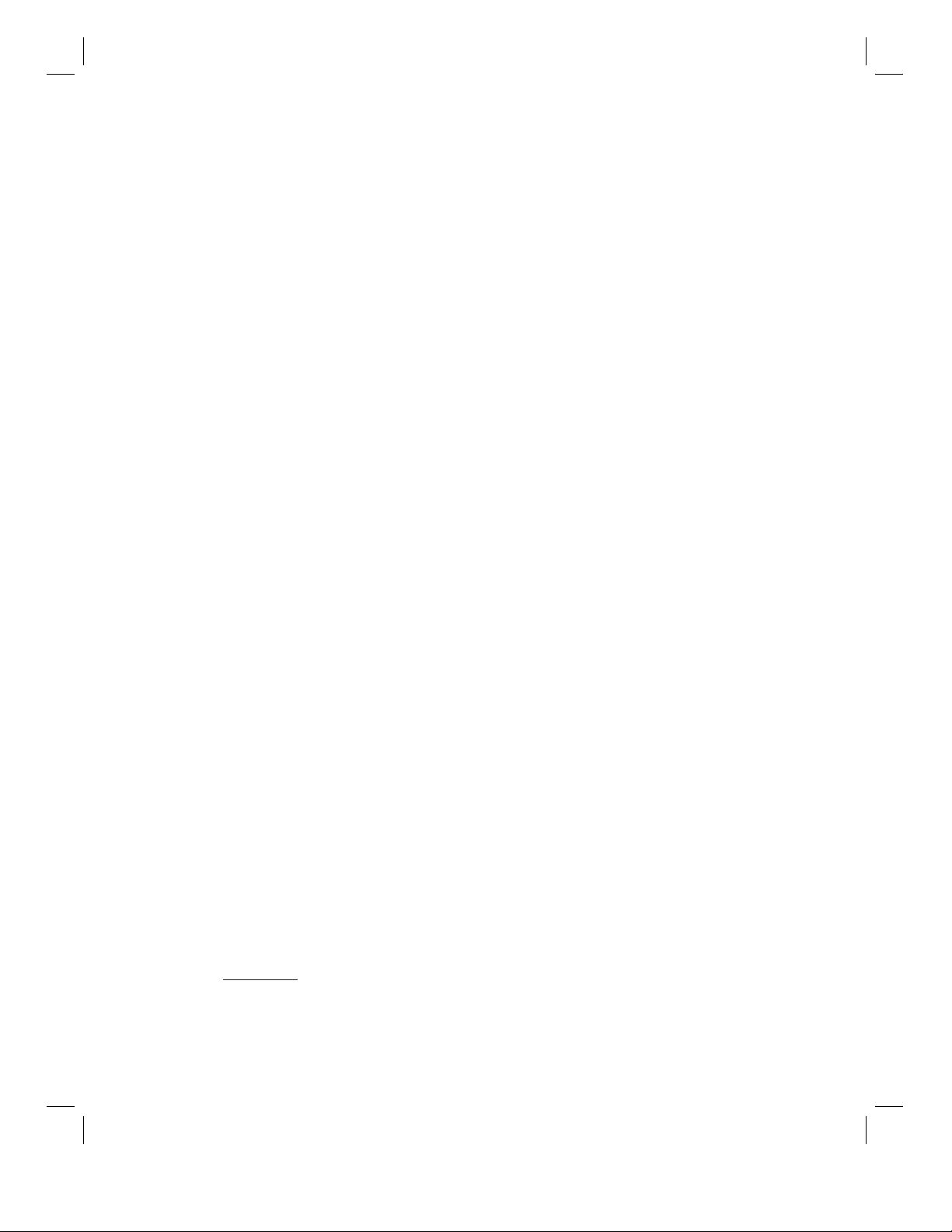
Integre Technical Publishing Co., Inc. Liu January 13, 2000 8:45 a.m. chap1 page 5
Section 1.1 Digital Control 5
give the output u(t) of the analog controller and the observed position y(t) of the arm as a
function of time. The solid lines in the lower and upper graphs give, respectively, the analog
control signal constructed from the digital outputs of the controller and the resultant observed
position y(t) of the arm. At the sampling rate shown here, the analog and digital versions are
essentially the same. The solid lines in Figure 1–2(b) give the behavior of the digital version
when the sampling period is increased by 2.5 times. The oscillatory motion of the arm is more
pronounced but remains small enough to be acceptable. However, when the sampling period
is increased by five times, as shown in Figure 1–2(c), the arm requires larger and larger control
to stay in the desired position; when this occurs, the system is said to have become unstable.
In general, the faster a plant can and must respond to changes in the reference input,
the faster the input to its actuator varies, and the shorter the sampling period should be. We
can measure the responsiveness of the overall system by its rise time R. This term refers to
the amount of time that the plant takes to reach some small neighborhood around the final
state in response to a step change in the reference input. In the example in Figure 1–2, a small
neighborhood of the final state means the values of y(t) that are within 5 percent of the final
value. Hence, the rise time of that system is approximately equal to 2.5.
A good rule of thumb is the ratio R/T of rise time to sampling period is from 10 to
20 [AsWi, FrPW].
2
In other words, there are 10 to 20 sampling periods within the rise time.
A sampling period of R/10 should give an acceptably smooth response. However, a shorter
sampling period (and hence a faster sampling rate) is likely to reduce the oscillation in the
system response even further. For example, the sampling period used to obtain Figure 1–2(b)
is around R/10, while the sampling period used to obtain Figure 1–2(a) is around R/20.
The above rule is also commonly stated in terms of the bandwidth, ω, of the system.
The bandwidth of the overall system is approximately equal to 1/2R Hz. So the sampling
rate (i.e., the inverse of sampling period) recommended above is 20 to 40 times the system
bandwidth ω. The theoretical lower limit of sampling rate is dictated by Nyquist sampling
theorem [Shan]. The theorem says that any time-continuous signal of bandwidth ω can be
reproduced faithfully from its sampled values if and only if the sampling rate is 2ω or higher.
We see that the recommended sampling rate for simple controllers is significantly higher than
this lower bound. The high sampling rate makes it possible to keep the control input small and
the control-law computation and digital-to-analog conversion of the controller simple.
Multirate Systems. A plant typically has more than one degree of freedom. Its state
is defined by multiple state variables (e.g., the rotation speed, temperature, etc. of an engine
or the tension and position of a video tape). Therefore, it is monitored by multiple sensors and
controlled by multiple actuators. We can think of a multivariate (i.e., multi-input/multi-output)
controller for such a plant as a system of single-output controllers.
Because different state variables may have different dynamics, the sampling periods
required to achieve smooth responses from the perspective of different state variables may
be different. [For example, because the rotation speed of a engine changes faster than its
2
Sampling periods smaller than this range may have an adverse effect. The reason is that quantization error
becomes dominant when the difference in analogy sample readings taken in consecutive sampling periods becomes
comparable or even smaller than the quantization granularity.
评论0
最新资源