
huayuya123
- 粉丝: 27
- 资源: 31万+
最新资源
- 基于IronPython的股票技术分析系统详细文档+全部资料+高分项目.zip
- 基于PaddleNLP搭建评论观点抽取和属性级情感分析模型,并基于前后端分离式架构完成属性级情感分析Web系统搭建,通过细粒度情感分析帮助用户和商家更好决策。详细文档+全部资料+高分项目.zip
- 基于pyltp的工具中文依存句法的四大名著人物情节分析系统、实现了人物篇幅分析,故事发生地分析,主要人物情绪变化分析,人物互动情况分析.详细文档+全部资料+高分
- 基于Saprk的用户行为分析系统详细文档+全部资料+高分项目.zip
- 基于Qt的学生信息管理系统。教师端:支持增删查改,班级成绩分析。学生端:查看成绩。详细文档+全部资料+高分项目.zip
- 基于RT-Thread系统的空气质量分析仪详细文档+全部资料+高分项目.zip
- 基于spark streaming和kafka,hbase的日志统计分析系统详细文档+全部资料+高分项目.zip
- 基于Spring Boot的在线问卷调查系统,登录注册、调查问卷模板、创建调查问卷、在线编辑模板、社交网站分享问卷、问卷结果分析与统计(图表展示)以及个人中心等
- 基于Strom的日志实时流量分析主动防御(CCFirewall)系统详细文档+全部资料+高分项目.zip
- 基于SpringBoot Mybatis 的毕业生就业信息分析系统详细文档+全部资料+高分项目.zip
- 基于Spring+SpringMVC+Mybatis+redis+Vue+Swagger2小程序商城+(vue)微信商城+综合管理后台+网站商城+运营商平台+A
- 基于Strom的实时流量分析防火墙系统详细文档+全部资料+高分项目.zip
- 基于tfs2.2.16代码,添加注释和分析,学习分布式存储系统详细文档+全部资料+高分项目.zip
- 基于ThinkPhp5.0+Vue开发的一套新零售直播点播知识付费系统,销推广关系管理+营销+直播的知识类电商系统,能够快速积累客户、会员数据分析、智能转化客户
- 基于UIE的舆论情感分析Web系统,支持单文本属性级情感分析及上传txt文件进行批量情感分析,并支持分析结果的可视化展示。 技术栈:后端:FastAPI + U
- 基于thinkphp和mysq舆情分析系统,详细文档+全部资料+高分项目.zip
资源上传下载、课程学习等过程中有任何疑问或建议,欢迎提出宝贵意见哦~我们会及时处理!
点击此处反馈


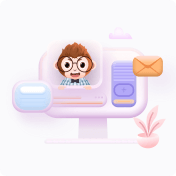